Workplace accident rates across the United States have been in decline for many years as a result of the dedication of health and safety professionals. However, those rates seem to have bottomed out over the last few years, stubbornly refusing to move any lower. This blog looks at those areas that have the highest rates of workplace accidents and what you can do to improve safety in your organization.
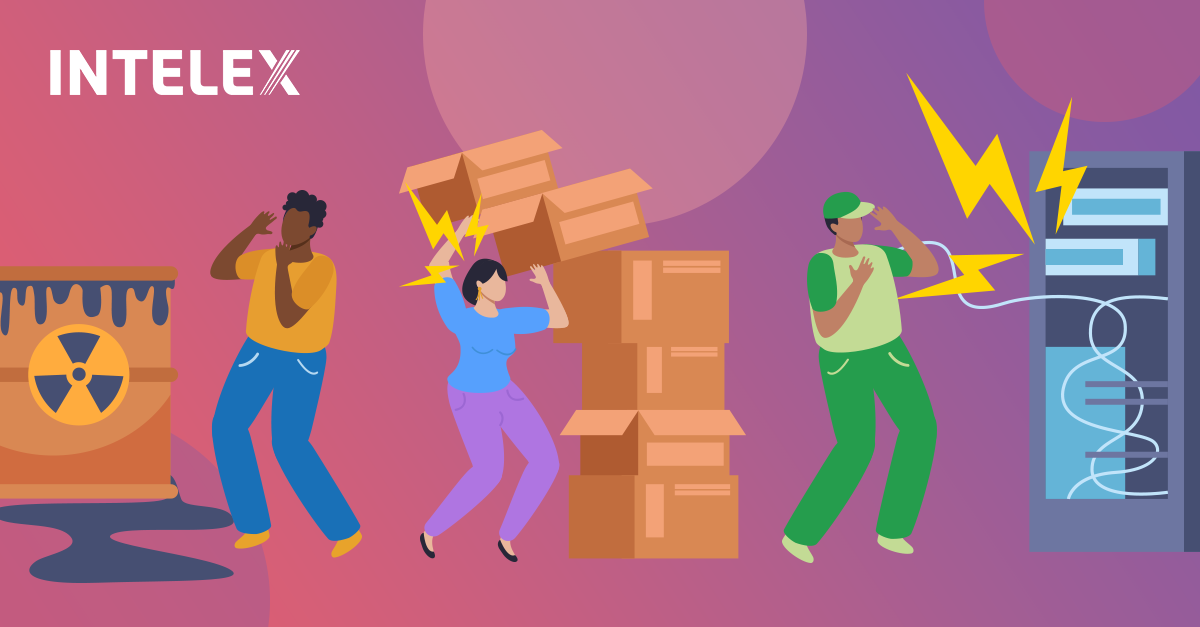
Highlights
The Role of Data and Leading Indicators
The Role of the Frontline Worker
Takeaways: What You Can Do To Reduce Workplace Accidents
How Intelex Can Help
Today’s U.S. workplaces are safer than they’ve ever been. Thanks to the tireless work of safety professionals creating strong safety cultures supported by cutting-edge technology, fatal and nonfatal workplace accidents have declined drastically over the last few decades. In addition, strong enforcement actions from regulatory agencies like the Occupational Safety and Health Administration (OSHA) … Read more...