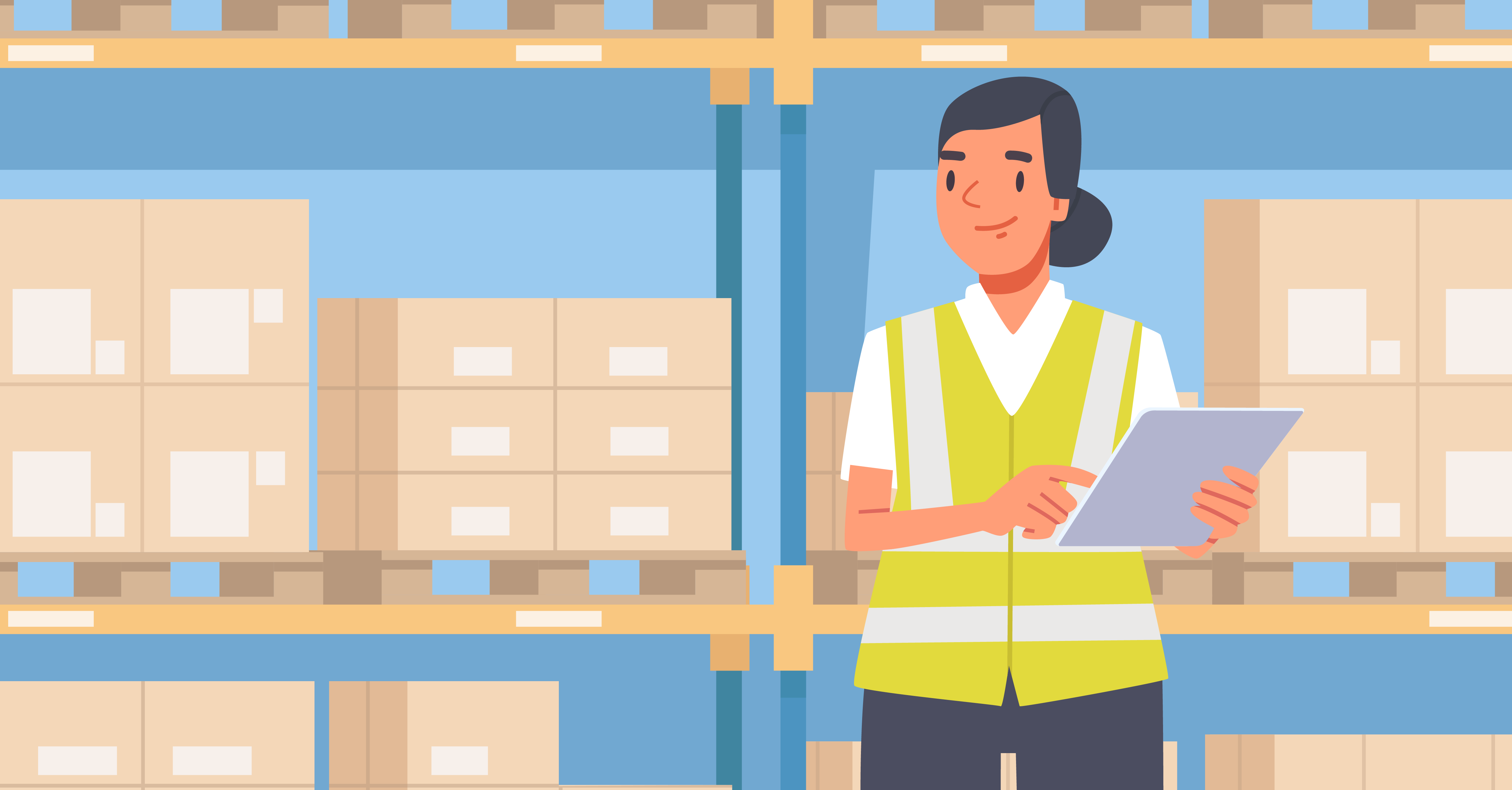
Why EHS Teams Choose Point Solutions (And Why There's a Better Way)
4 minute read As a modern EHS leader, you know it’s critical to digitize your safety program. The challenge for small or midsize businesses (SMBs) is knowing what kind of solution will actually work for your team. Picture this: Inspections are
Trending Posts
Latest Posts
- Health & Safety Management
Digital Transformation in EHS: Expert Tips for Getting It Right
Expert advice for leading a successful digital...
- Intelex News and Updates
Tap Into Knowledge, Tips, and Support in the Intelex Community
Learn about the Intelex Community. A hub exclusive to customers to connect with peers, get expert tips, solve problems faster, and get more value from your...
- Environmental Sustainability and ESG Reporting
Why Scope 3 Emissions Are the Next Big ESG Hurdle—and How to Tackle Them
Scope 3 emissions are the most complex—and increasingly mandatory—part of ESG reporting. See how you can tackle them with the right data, tools, and...
- Industry Trends and Insights
All In Together: A Personal Call to Action for Construction Safety Week 2025
Safety isn’t a department—it’s a shared commitment. In this personal message for Construction Safety Week 2025, Scott Gaddis calls on the industry to embrace true collaboration, close safety gaps, and leverage technology that empowers every worker to...
- Health & Safety Management
Culture vs. Compliance: Building a Sustainable and Balanced Safety Mindset
Discover strategies to align compliance and culture for stronger, safer workplaces. Learn how EHS leaders can drive engagement, accountability, and...
- Health & Safety Management
The 5 Biggest Safety Imbalances Holding Organizations Back — And How to Fix Them
The father of modern management, Peter Drucker, once said, “Efficiency is doing things right; effectiveness is doing the right things.” This distinction is particularly relevant in safety...