Preventing Slips, Trips, and Falls: Leveraging Controls and Continuous Improvement for a Safer Workplace
May 5, 2023
Did you know fall protection has been OSHA’s most frequently cited safety and health standard for 13 consecutive years?
In 2023 alone, there were 7,271 violations.
These seemingly innocuous incidents can lead to serious injuries, impacting both the well-being of workers and the operational efficiency of organizations. To address this critical issue, organizations must adopt a proactive approach, leveraging strategies such as the Hierarchy of Controls and embracing continuous improvement methodologies.
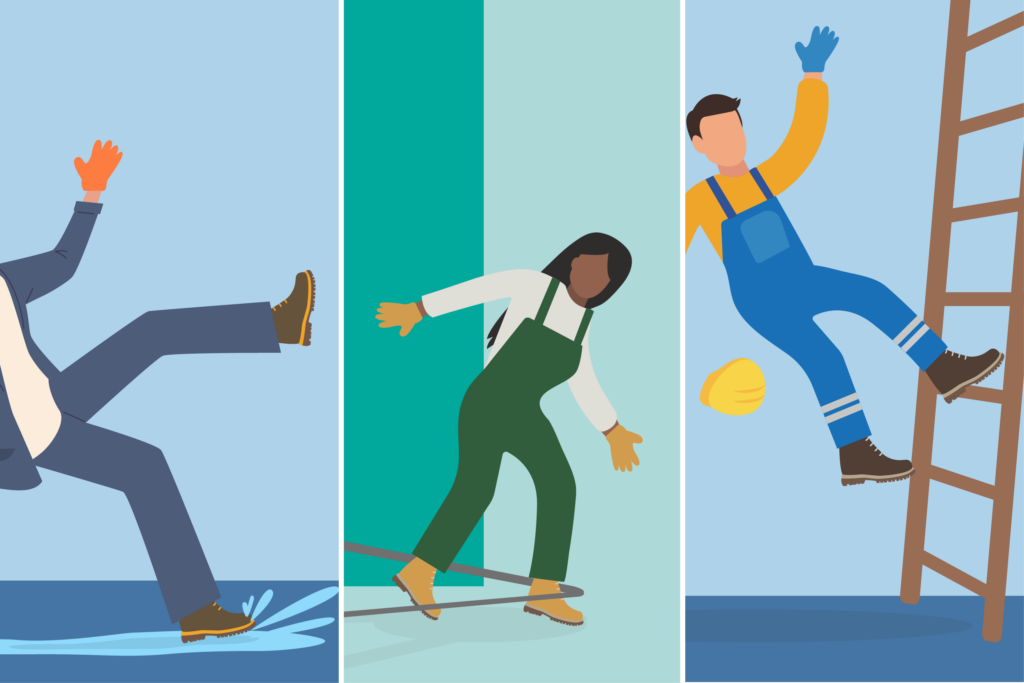
In this three-part series dedicated to fall prevention strategies, Scott Gaddis—Vice President, Global Practice Leader, Safety and Health at Intelex Technologies, ULC—provides his expert insight into the risks associated with pedestrian safety in the workplace and what employers need to do to mitigate them. Part I looks at common types of slips, trips and falls and how they occur. Part II discusses how risk assessment can help prevent slips and trips in the first place. Part III below examines how the hierarchy of controls can contribute to continuous safety improvement in slips, trips and falls prevention.
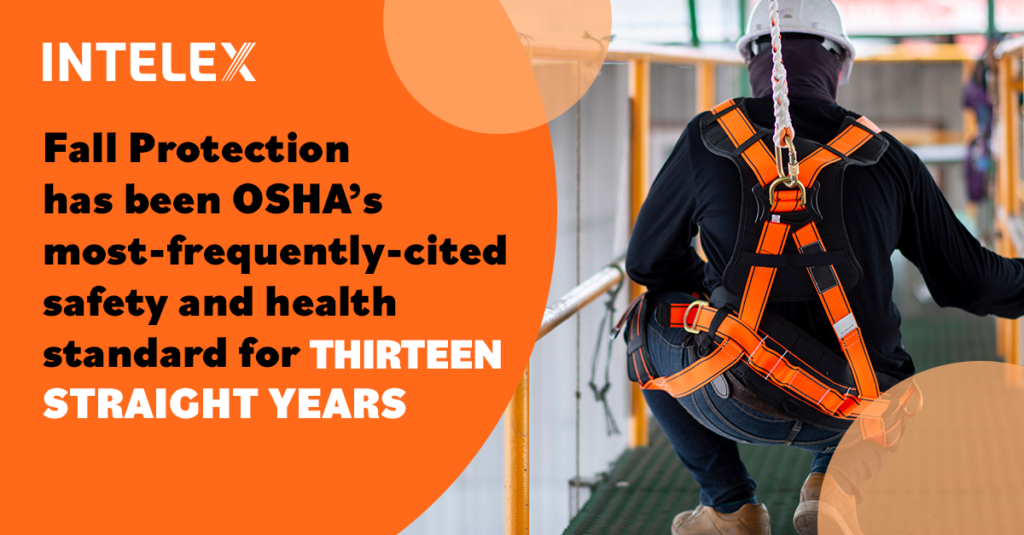
Employing the Hierarchy of Controls for Slips, Trips and Falls Prevention
Understanding control and how best to manage your walking working surfaces program are more significant than the outputs of the risk assessment process. The process defines good control actions specific to hazards and risks, but it is not the only process that can be used. While I’m a firm believer in the risk matrix and scoring approach, I also would recommend the widely accepted approach within the safety and health practice called the hierarchy of controls. This process is simple to understand and is quite useful in gauging the control appetite of the organization. It should serve as the overarching methodology for how we best deliver the right level of program control within the scope of walking-working surfaces programs.
The control hierarchy shows the most effective controls at the top, which are engineering solutions, followed by administrative controls and finally the reliance on personal protective equipment.
Though not intended to be an exhaustive list, it points out there are control considerations when dealing with improving the walking-working surfaces program.
Hierarchy of Control | Control Feature | Examples of Control |
---|---|---|
Elimination | Completely eliminate the hazard. | Eliminate motorized and material handling equipment from the facility. |
Substitution | Reduce a hazardous situation component, material and/or piece of equipment. | Install slip-resistant flooring. |
Engineering Controls | Isolate people from the identified hazard or risk. | Improve illumination to the walking-working surface. |
Administrative | These controls are changes that can include safety policies, rules, supervision, schedules and training. | Train workers on slips, trips and falls |
PPE | Protection worn by a worker to protect them or reduce loss threshold from a hazard. | Require slip-resistant footwear. |
Continuously Monitoring Slips, Trips and Falls
Like much of our past thinking, once a project is planned and executed, we tend to lean on the idea that the work is done. Business theorist and management expert W. Edwards Deming recognized this as an issue, and in the 1950s, he created a simple process approach that still is widely used to analyze and measure process deviation. Deming was a proponent that the work system needed to reside in a continuous feedback loop so that managers could identify and change the parts of the process that needed improvement. He called this the PDCA cycle for Plan, Do, Check and Act.
Applying this thinking, the reality is that many of us have dealt with poorly executed and implemented projects that created loss potential in the organization. Checking the process with a cadence required to maintain control is necessary.
Continuously monitoring your walking-working surfaces program ensures that you have gained control of the issues raised during the inspection process, that the control strategy eliminated the problem or reduced it to a tolerable risk level. The fundamental questions often asked are: did you achieve your goals, and can such goals be sustained? Factually and for the safety and health practitioner, what it means is that unless you genuinely can say that you’ve eliminated the deviation (issue) and it can’t come back, you are never done in looking for, evaluating and controlling risks in the work system. To put these insights into action in your workplace, download our Walking-Working Surface Inspection Checklist. It will help you understand the key surface categories and controls, the actions and responsibilities for preventing falls and the key items you should know for indoor and outdoor safety inspections.
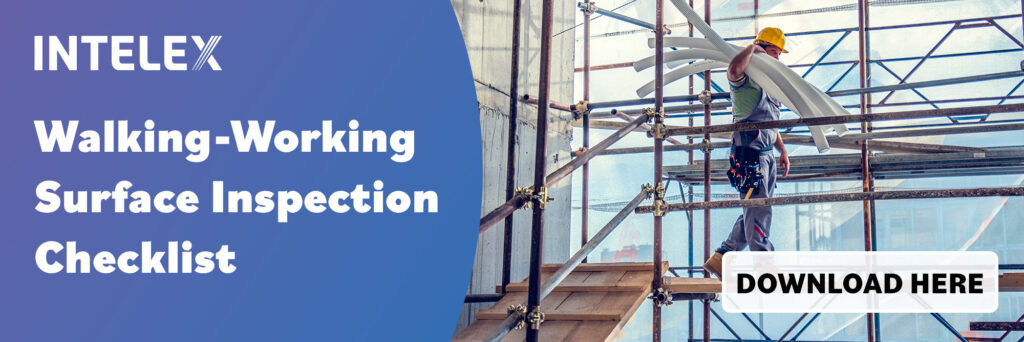
How to Prevent Slips, Trips and Falls FAQs
What specific criteria or indicators are used to determine if a risk level is “tolerable”?
Determining if a risk level is “tolerable” is often a complex process that involves both quantitative and qualitative measures. Tolerable risk is essentially a risk level that an organization can live with as a given, considering the benefits of the activities that generate the risk. It often reflects the organization’s compliance with legal requirements and its own internal safety standards, which incorporate industry best practices and benchmarks. To define tolerable risk, organizations may use a combination of incident data, historical benchmarks, regulatory thresholds, and stakeholder input, including the risk perceptions of workers and management. This information is then typically incorporated into a risk assessment framework or matrix, where different levels of risk are classified and managed accordingly.
How does Intelex EHS Software integrate with other safety management systems and processes within an organization?
Integrating Intelex EHS Software with other safety management systems and processes typically involves a detailed analysis of the existing systems to identify areas of compatibility and potential integration points. Intelex software is designed with interoperability in mind, allowing data to be shared and processes to be linked with other systems through APIs (Application Programming Interfaces) or data import/export functions. The extent to which Intelex can be integrated into an organization’s existing systems will depend on the technical specifications of those systems and the organization’s specific integration requirements. It often requires collaboration between IT specialists, EHS professionals, and the software provider to ensure a seamless integration that minimizes disruptions and maximizes the utility of all systems involved.
How Intelex EHS Software Can Help Create a Slips, Trips and Falls Prevention Program
Implementing an effective slips, trips, and falls prevention program requires not only a robust understanding of risks and controls but also a systematic approach to monitoring and continuous improvement. EHS software can play a valuable role in ensuring the success and sustainability of fall prevention efforts.
Here are four recommended Intelex applications:
Risk Matrix Designer: A Risk Matrix Designer streamlines the risk assessment process by providing a centralized platform for creating, documenting and managing risk matrices. This tool enables organizations to systematically evaluate the risks associated with specific jobs or tasks, identify potential hazards leading to slips, trips and falls, and implement control measures effectively. By digitizing this process, companies can enhance the accessibility of risk matrices, ensuring that workers have readily available information to perform tasks safely.
Safety Inspection Software: This software facilitates regular inspections of walking-working surfaces, enabling organizations to proactively identify and rectify hazards before incidents occur. Through a mobile application, safety inspections can be conducted by workers efficiently, and findings can be immediately documented and aggregated into insights that prompt corrective actions.
Incident Management Software: In the unfortunate event of a slip, trip or fall incident, timely and accurate reporting is crucial for effective resolution and prevention of future occurrences. Incident Management Software facilitates swift reporting, investigation and documentation of incidents. The software helps in identifying root causes, analyzing trends and implementing corrective actions to address underlying issues, thus contributing to a proactive approach in preventing similar incidents in the future.
Corrective and Preventive Action (CAPA) Software: CAPA software aids organizations in implementing corrective measures and preventive actions based on incident analyses and risk assessments. By tracking and managing corrective actions in a centralized system, organizations can systematically address the identified issues, implement controls to prevent recurrence and monitor the effectiveness of these measures over time. This ensures a continuous improvement loop that aligns with the principles of the PDCA (Plan, Do, Check, Act) cycle advocated by Deming.
Incorporating EHS software into the slips, trips and falls prevention strategy not only enhances efficiency but also contributes to a data-driven and proactive safety culture. By leveraging technology, organizations can systematically reduce the risk of falls, align with regulatory requirements and foster a workplace environment that prioritizes the well-being of employees.
Protect your workforce by staying ahead of slips, trips, and falls with proven strategies. Ready to enhance your safety program and reduce workplace hazards? Schedule a consultation with our experts today and discover how Intelex’s EHS software can help you implement the Hierarchy of Controls for effective, continuous improvement.
In case you missed the previous articles in the Slips, Trips and Falls series, Part I looks at common types of falls from the same level and how they occur. Part II discusses how risk assessment can help prevent slips and trips in the first place.