Workplace Accident Rates Still Aren’t Low Enough: What You Can Do To Reduce Fatal and Nonfatal Injuries
August 8, 2023
Workplace accident rates across the United States have been in decline for many years as a result of the dedication of health and safety professionals. However, those rates seem to have bottomed out over the last few years, stubbornly refusing to move any lower. This blog looks at those areas that have the highest rates of workplace accidents and what you can do to improve safety in your organization.
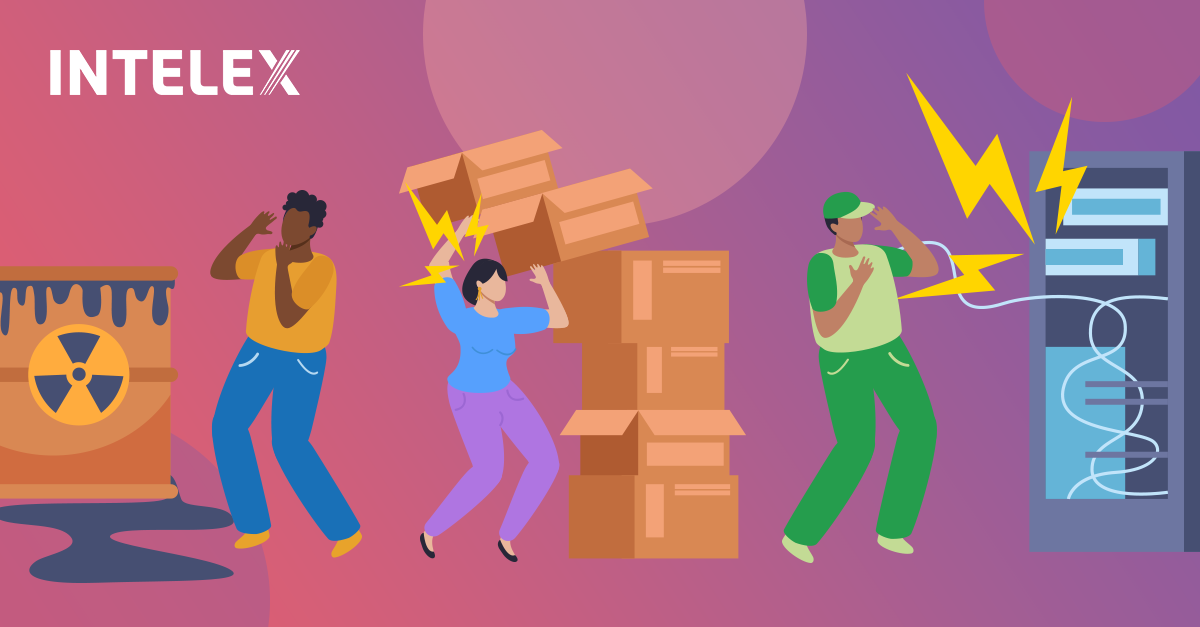
Highlights
The Role of Data and Leading Indicators
The Role of the Frontline Worker
Takeaways: What You Can Do To Reduce Workplace Accidents
How Intelex Can Help
Today’s U.S. workplaces are safer than they’ve ever been. Thanks to the tireless work of safety professionals creating strong safety cultures supported by cutting-edge technology, fatal and nonfatal workplace accidents have declined drastically over the last few decades. In addition, strong enforcement actions from regulatory agencies like the Occupational Safety and Health Administration (OSHA) continue to convey to employers the importance of keeping workers safe in the workplace.
However, despite that success, rates for workplace accidents resulting in fatalities and injuries continue to be higher than they ought to be. According to the Bureau of Labor Statistics, private employers reported 2.6 million nonfatal workplace injuries in 2021. At the same time, the 2021 rate for fatal workplace injuries was 5,190. While rates for both fatal and nonfatal incidents fluctuate over time, they have stubbornly remained essentially level for the last several years.
The hierarchy of workplace accidents is not the same for both fatal and nonfatal injuries, as shown in Table 1.
Incident Type (Fatal) | % | Incident Type (Nonfatal) | % |
---|---|---|---|
Transportation | 39 | Overexertion and Bodily Reaction | 30 |
Falls, Slips, Trips | 16 | Falls, Slips, Trips | 24 |
Violence by Persons or Animals | 16 | Contact with Objects and Equipment | 24 |
Contact with Objects and Equipment | 14 | Exposure to Harmful Substances or Environments | 12 |
Exposure to Harmful Substances or Environments | 13 | Transportation Incidents | 5 |
Fires and Explosions | 2 | Violence by Persons or Animals | 4 |
Overexertion and Bodily Reaction | <1 | Nonclassifiable | 1 |
Nonclassifiable | <1 | Fires and Explosions | <1 |
Table 2 shows the top five industries in which most fatal and nonfatal workplace accidents occurred in 2021, the most recent year in which complete data was available.
Industry (Fatal) | Deaths | Industry (Nonfatal) | Injuries |
---|---|---|---|
Construction | 986 | Education and Health Services | 287,300 |
Transportation and Warehousing | 976 | Government | 272,400 |
Government | 461 | Retail | 156,000 |
Agriculture, Forestry, Fishing and Hunting | 453 | Manufacturing | 137,000 |
Manufacturing | 383 | Transportation and Warehousing | 122,700 |
The Role of Data and Leading Indicators
Safety professionals are increasingly looking to data to provide deeper insights into trends and behaviors that can keep workers safe and prevent workplace accidents before they take place. Up until recently, manual processes have favored the traditional approach to safety based on lagging indicators derived from root-cause analysis, incident investigations and corrective actions. While this approach has seen considerable success in reducing fatal and nonfatal injuries over the years, lagging indicators require those injuries to have taken place before practitioners have the important data they need to promote continuous improvement in the safety management system. This reactive approach has been an important component of workplace safety for decades, and it will continue to provide important data when accidents do occur. However, it is also a reactive approach that does nothing to protect the people who have been hurt or killed. Nor does it promote a sense of trust in the organization’s safety culture.
Lagging indicators also suffer from becoming gradually less useful over time. Data analytics relies on large data sets to uncover trends, behaviors and safety hotspots across the organization to help prevent workplace accidents before they occur. However, as safety improves, a reactive approach will produce less data, making the predictive models less accurate. Eventually, continuous safety improvement will grind to a halt and be unable to close a persistent gap.
Leading indicators, in contrast, are derived from data and analysis that assess risk to determine the likelihood of events culminating in workplace accidents in the future. Instead of using data derived from incidents, leading indicators are built on data derived from inspections, training, observations and other frontline elements that have the potential to aggregate into incidents over time. By collecting and analyzing these risk factors, safety leaders can develop leading indicators that identify problems before they become workplace accidents that lead to fatal or nonfatal injuries.
Today’s safety management systems must incorporate both leading and lagging indicators to support a safety culture of continuous improvement, with leading indicators for prevention and lagging indicators to assess workplace accidents that happen. No workplace will ever be entirely without risk or incident, which means lagging indicators will continue to play an important role in providing data that can lead to incident reduction.
The Role of the Frontline Worker
There are no panaceas in workplace safety. Technology solutions, training, methods and standards are all critical components of safety, but none of them will provide a magic cure for helping to keep frontline workers safe.
Safety is a partnership between frontline workers and leadership. Frontline workers who bear the brunt of workplace accidents must feel that leadership cares about their safety. The first step towards a safer workplace is a strong safety culture in which everyone is a partner in preventing accidents.
A critical component of this safety culture is ensuring frontline workers are empowered to provide the data the organization needs to support leading indicators. Mobile digital solutions allow frontline workers to feed constant data into the management system in the form of observations from all across the workplace. Workers empowered with the ability to report observations at any time and any location become an army of always-on safety inspectors providing continuous safety data that can be used for analytics to derive leading indicators or sent back to the frontline workers in the form of bulletins or microlearning.
In a digitally empowered safety management system, frontline workers become process owners and active participants in their own safety culture to prevent workplace incidents before they happen, as shown in Figure 1.
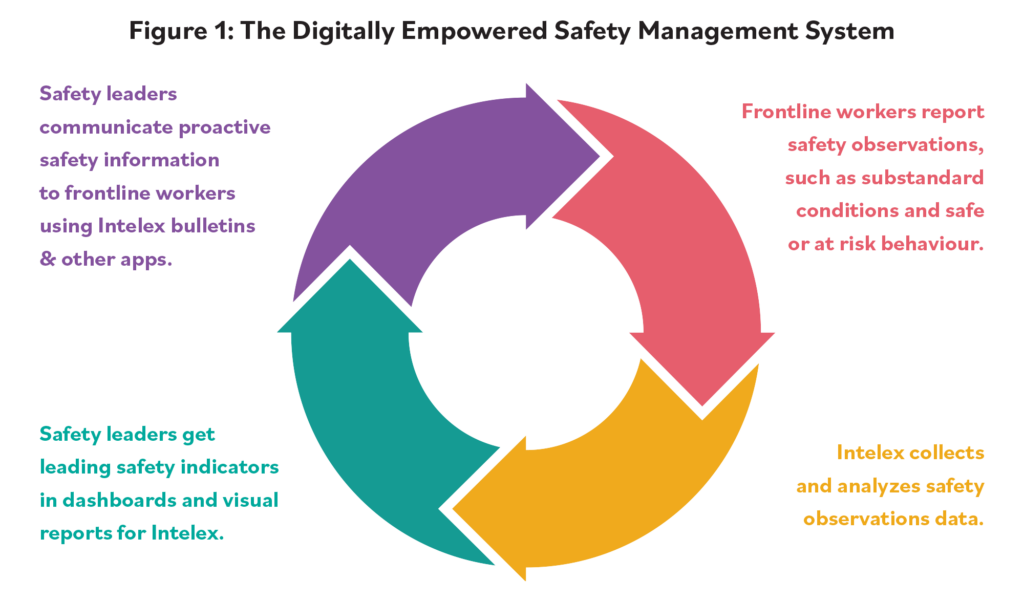
The most important data for supporting leading indicators are observations (a single instance of a behavior or condition that can be either safe or at-risk) and inspections (a collection of one or more observations). These two elements support four general principles, as shown in Table 3.
1. Incidents go down when inspections increase. | This is the first stage of collecting data for leading indicators. The more data you have, the more accurate your predictive models can be. |
2. Incident probability decreases as number and diversity of people performing inspections increases. | Inspections should not be activities performed only by inspectors. Everyone on the front line should be recording observations. This crowd-sourced approach from diverse observers increases the volume and quality of data. |
3. Too many safe inspections can be predictive of higher injury rates. | If no one is reporting at-risk, observations, things are not as they seem. New, unfamiliar issues might be growing unseen or workers might not be recording their observations properly, maybe because of error or fear of punishment. |
4. Having too many repeated at-risk observations is predictive of higher injury rates. | Digging more deeply into at-risk observations data will reveal if they are new issues that can b corrected or if they are persistent, reoccurring issues that require retraining or more extensive corrective actions. |
Takeaways: What You Can Do To Reduce Workplace Accidents
The work safety professionals have done over the years has significantly reduced the rates of workplace accidents. In 1992, the rate of workplace deaths per 100,000 workers was 5. Since 2014, that rate has descended to between 3.4 and 3.6 per 100,000 workers. The total number of deaths has descended from 6,217 in 1992 to 5,190 in 2021. While we always strive to reach 0 workplace accidents, the continued decline in fatal workplace accidents shows that the work of safety is having a real impact.
Nevertheless, as the workplace and the marketplace rapidly change, new safety challenges will present themselves. If safety professionals want to continue having an impact on reducing fatal and nonfatal injuries in the workplace, they will need to augment the traditional approaches to safety with a data-driven method built on leading indicators. Here are a few things to think about as we move into a new era of workplace safety.
Focus on the right events.
Every job has different levels of risk for fatal and nonfatal injuries. Every near miss or minor incident could have the potential for a SIF (serious injury or fatality) event, which means a rigorous root cause analysis will be critical in uncovering hidden risks and to prevent the possibility of those events culminating in future SIFs. Utilize the Hierarchy of Controls and prioritize the first three levels (Elimination, Substitution and Engineering Controls), as shown in Fig. 2, to reduce the likelihood of SIFs.
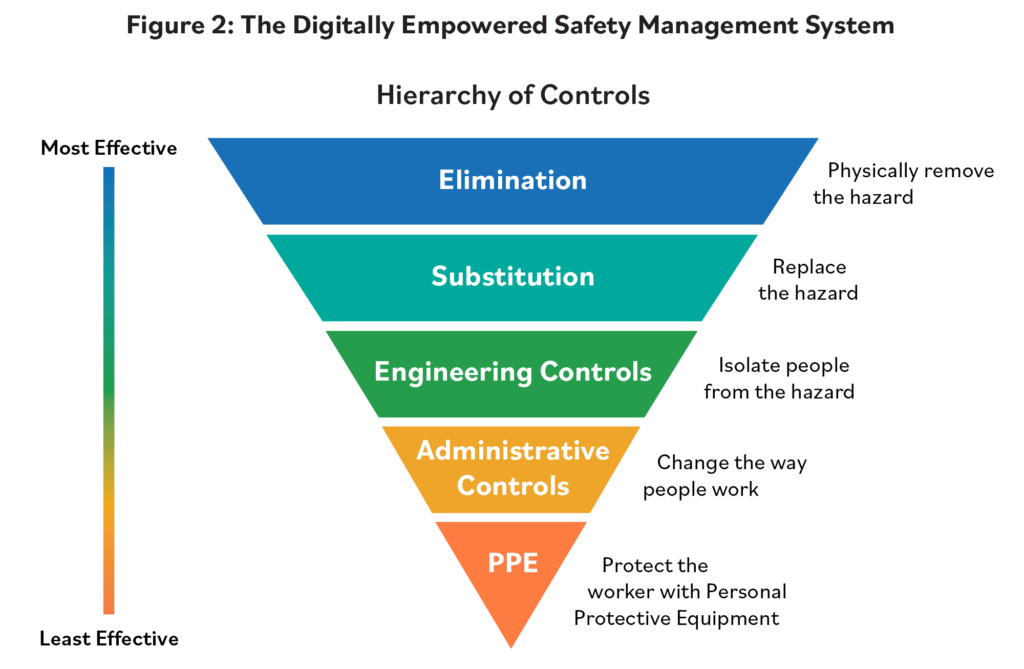
Form strong safety partnerships.
Frontline workers are stakeholders in their own safety and in the success of the organization. Empower frontline workers with the technology, training and autonomy they need to record observations and provide a continuous inflow of data to the safety management system to create an effective and efficient culture of safety.
Understand the work.
Purchasing a digital solution to support the safety management system will not work unless you understand how your frontline workers do their jobs. You need to understand the risks and complexities of every task before you know enough about the work to implement a digital solution. Many problems with implementing and adopting digital solutions have their origin in management not understanding the needs of frontline workers before purchasing new technology.
Mobile solutions are critical.
Frontline workers must be able to record observations anytime at any location to provide the continuous inflow of data to the safety management system. If workers in the field need to write down observations or wait to submit them on a desktop computer, most of those observations will never be recorded, and the flow of data needed to support leading indicators will be disrupted. Mobile solutions with easy access and a simple interface will facilitate easy reporting and produce the data the analytical models need to prevent workplace accidents.
How Intelex Can Help
Intelex applications support safety management systems that reduce injuries and empower frontline workers. By using mobile technology to collect continuous safety data through observations from the front line, organizations can generate leading indicators that identify safety trends and prevent incidents before they happen.
Applications such as Job Safety Analysis, Safety Observations and Audit Management can help organizations support a comprehensive safety management system built on data, training and frontline engagement.
Intelex is proud to support organizations like George’s Inc., Coats, Linde, SGS and many more in their work towards safety excellence in the workplace. As the world faces increased disruption and complexity, Intelex solutions bring the power of data and leading indicators to the front line to create a culture of safety partnership in which every worker plays a critical role keeping everyone in the organization safe.