How Risk Management Can Prevent Slips, Trips and Falls
May 3, 2023
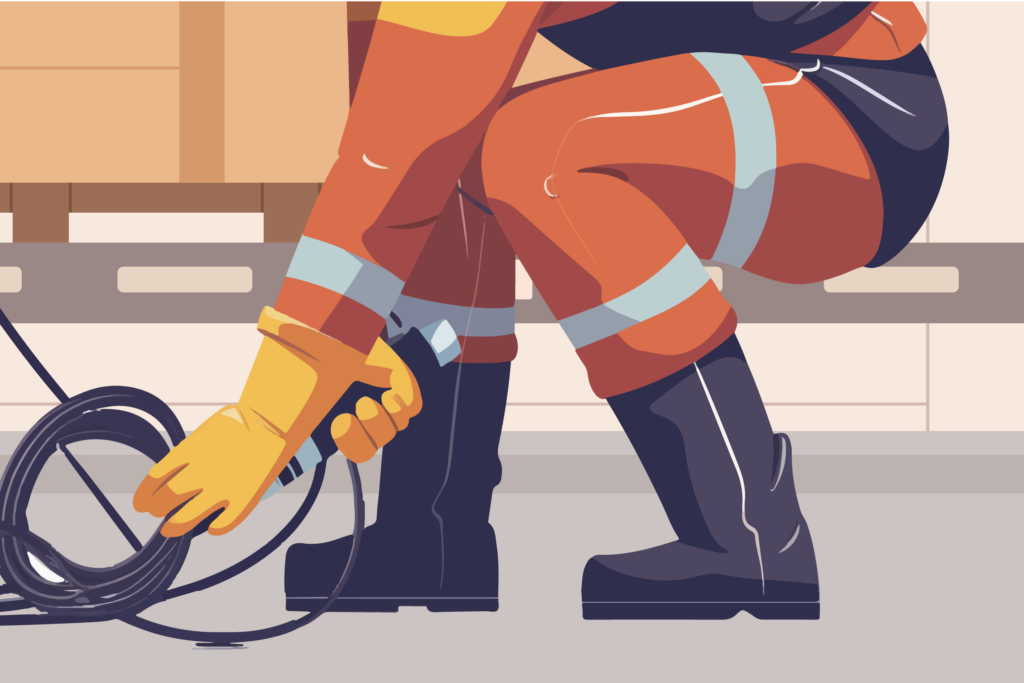
Fall protection solutions are essential to keep workers safe and ensure productivity. In 2020, the National Safety Council reported 127,680 work-related injuries that required days away from work. These are preventable injuries that are emotionally and financially debilitating for workers, and result in a financial loss for organizations and the wider economy.
In Part I of this series, Scott Gaddis, looks at how falls on the same level happen in the workplace and the impact they can have on workers. In Part II here, Scott examines the role of risk assessments in helping to prevent slips, trips and falls. Part III examines how hierarchy of controls can contribute to continuous safety improvement in fall prevention.
Risk Assessment to Prevent Falls on the Same Level
The objective of risk assessment and analysis is to understand the level of risk associated with the hazards found in the work environment as well as the concerns related to how people are navigating walking and working surfaces. All associated activities must be judged with criteria that help build a credible understanding of what is acceptable or not.
Most regulatory bodies require some form of risk assessment, and all follow a similar template:
- Identify risks to the worker associated with work activity.
- Identity hazards found in the work environment that pose a threat of loss.
- Provide details of identified risks or hazards and provide context to build understanding.
- Utilize a measurement system to evaluate risk understanding and decide precautions.
- Build controls that protect people and the work environment.
For the safety and health practitioner to manage walking and working surface risks with a degree of control that is equitable to the threat, a method of assessment process should be considered. The U.K.’s HSE has developed a risk assessment process that supports this well. The tool, largely adopted throughout Great Britain and the European Union, addresses risks through hazard understanding and evaluation and who may be affected. The assessment process focuses on prioritizing the risk. In this case, a hazard is identified as anything with the potential to harm workers. Risk is the likelihood of harm resulting from a hazard.
Risk Matrix to Evaluate Walking Working Surfaces
The risk matrix is a commonly used assessment tool for evaluating and estimating risk levels. The method assesses whether the hazard and possible risk are acceptable, scores them and then plots findings on a risk matrix to help decide the level of control. If the activity rating rises above acceptable levels, then controls are warranted at the level of control mandated or desired to lower scores to an acceptable level.
For every hazard identified during the walking-working surfaces inspection and for each associated activity, ask the question “What if?” What is the worst-case outcome regarding the hazard or concerning activity? Is it a fatality? A significant injury/permanent disability or permanent health effect? Is it a minor injury or even an environmental concern or something that could cause plant damage? Using the risk matrix, a judgment of the likelihood and severity of harm occurring can be made.
The severity (the degree or amount of expected loss) and the likelihood (how likely it is that the loss will occur) help determine the risk rating (the probability and severity of the risk before and after control actions are taken).
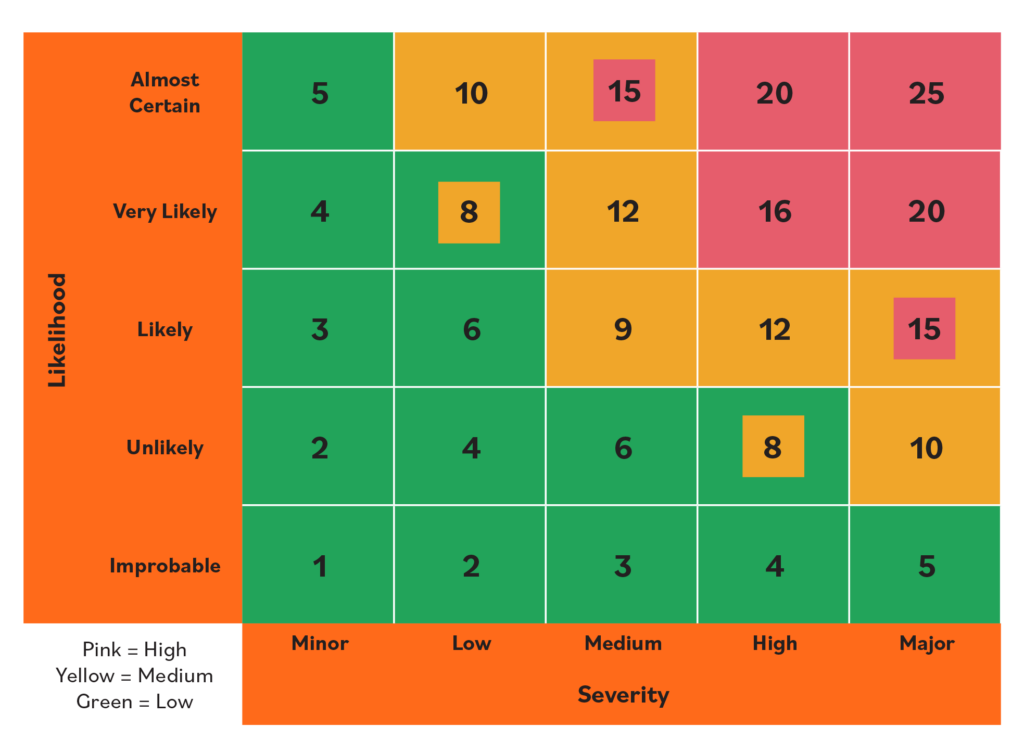
Using this approach of a five-point (5×5) matrix, you can estimate the likelihood (probability) and severity (consequence) within the five descriptive levels for likelihood and the five for the severity of consequence.
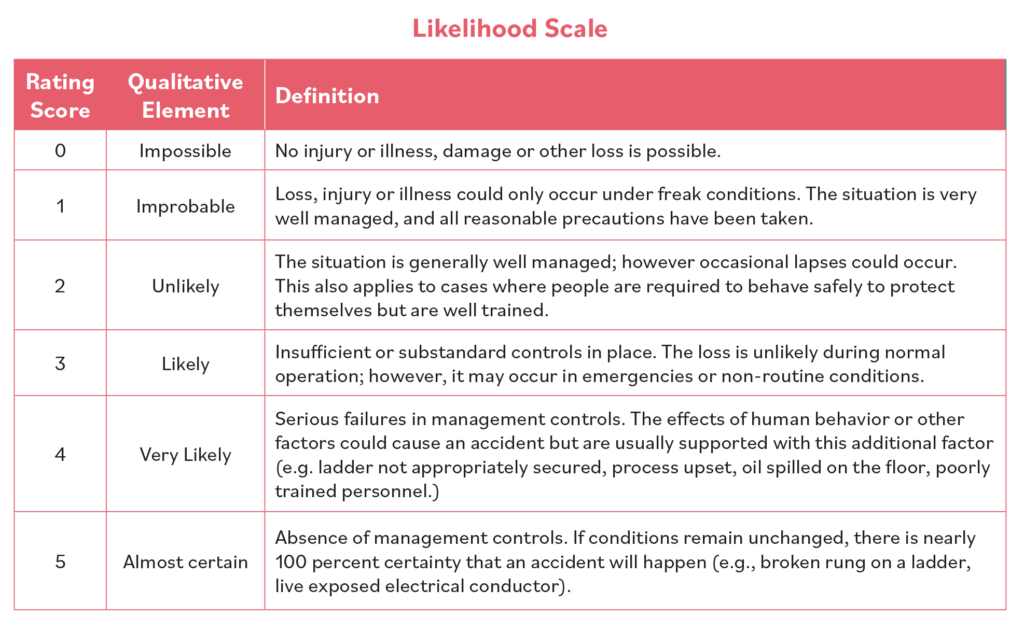
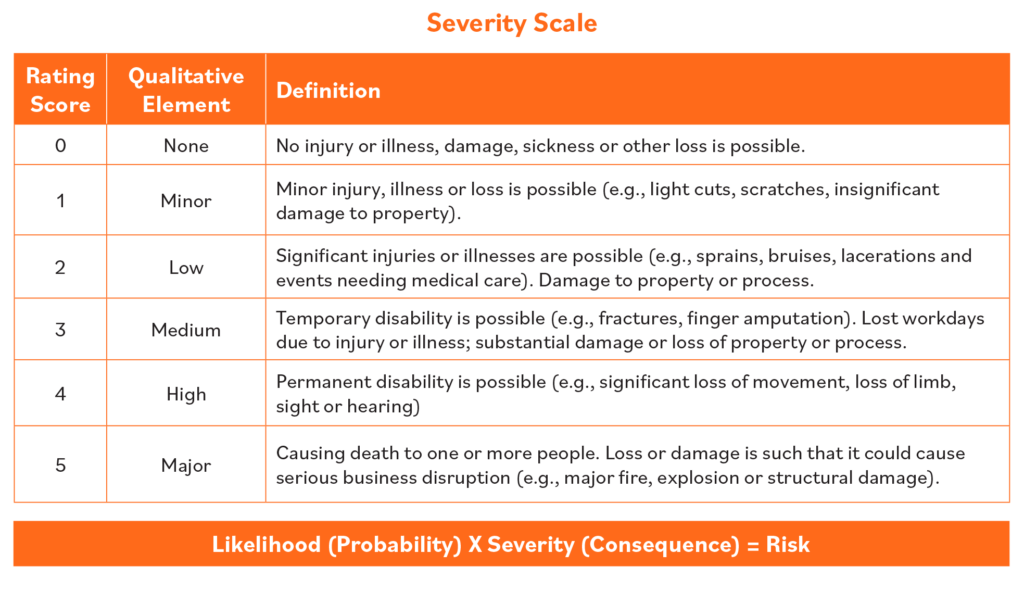
In the example shown in the photo below, a worker is expected to walk into the work area to feed raw material and must, at times, cross the machine frame to reach the other side where other tasks are performed. In this scenario, the worker steps up to the platform and onto a metal surface where most of the metal surface area is covered with a loose rubber mat. Worker interviews indicate that the mat is used because the surface becomes slippery. The mat appears to be in poor condition.
There also are two product roll stands 15” (38cm) above the work surface and they are empty with exposed sharp edges. Worker interviews indicate that these stands are empty because of the current machine setup requirements. The stands are struck often by workers performing tasks and have caused significant knee and shin injuries. Based on this scenario, the likelihood of falling is a “4,” which means very likely. This decision is based on the elevation change, poorly marked leading edge of the elevation change, the roll stands and the condition of the mat. The severity of falling in this situation also is a “4,” since—in a worst-case scenario—the consequence could result in permanent disability.
Given this information: Likelihood (4) x Severity (4) = Risk Rating (16). Referring now to the risk matrix (5×5 Matrix), it tells us that the hazards and work activity is a high risk, and the condition requires control to ensure the work environment is safe for work.
In the previous scenario, we started with a qualitative risk rating of 16, and mitigation action was required. While the worker still is expected to walk into the work area to feed raw material rolls and at times must cross the machine frame to perform other tasks, the leading edge is marked with a patterned contrasting color noting elevation change. The frayed rubber mat was removed and replaced with slip-resistant flooring material that adheres firmly to the metal surface. The roll stands were covered in a protective soft sleeve to minimize injury potential in a trip or fall. Additional signage was applied to warn workers of other hazards. Workers were trained on the new color scheme and operating procedures updated.
Based on this scenario, the likelihood of falling now is a “2,” which means it is unlikely based on the cumulative control actions. Severity from tripping or falling is estimated now as “3,” since in a worst-case outcome, the consequence still could result in temporary disability.
Considering this information: Likelihood (2) x Severity (3) = Risk Rating (6). This means that the risk is considered “tolerable.”
The purpose of risk assessment and evaluation is to assist the decision-making process based on the analysis regarding which hazards and associated risks require action and how to prioritize them. As referenced in the above scenario, clearly the risk of operating within the described work environment is now tolerable, but with additional risk reduction opportunities available if desired. Using these analytic tools is a vital fall protection solution to help lessen and ultimately prevent falls on the same level.
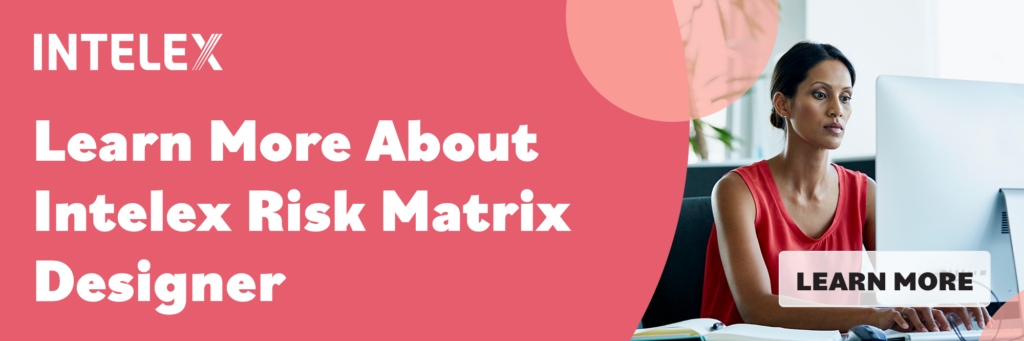
In Part III, we’ll look at using the Hierarchy of Controls to proactively manage the risk of falls in the workplace. In Part I, we discussed the types of slips, trips and falls and how they happen in the workplace.