Scott Gaddis
Scott Gaddis, VP and Global Practice Leader at Intelex Technologies in Toronto, Canada, drives thought leadership and partnerships in EHS. With extensive experience in global EHS leadership roles, including at Coveris and Bristol-Myers Squibb, Scott collaborates to enhance EHS capabilities globally. Scott holds a Master's degree in Occupational Safety and Health and is a published author and lecturer in the field.
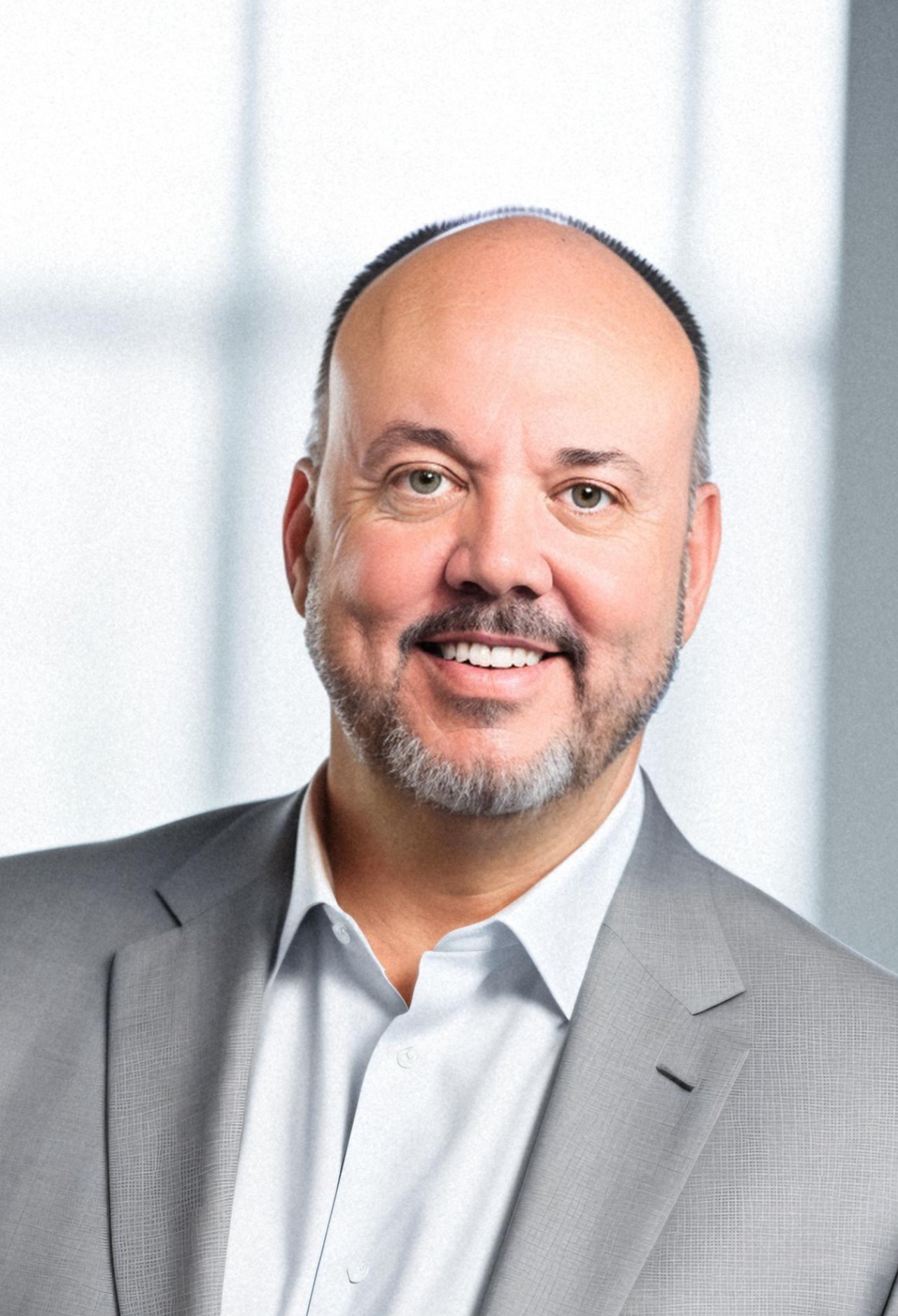