Key Principles and Technologies to Implementing a Robust Safety Program
August 24, 2021
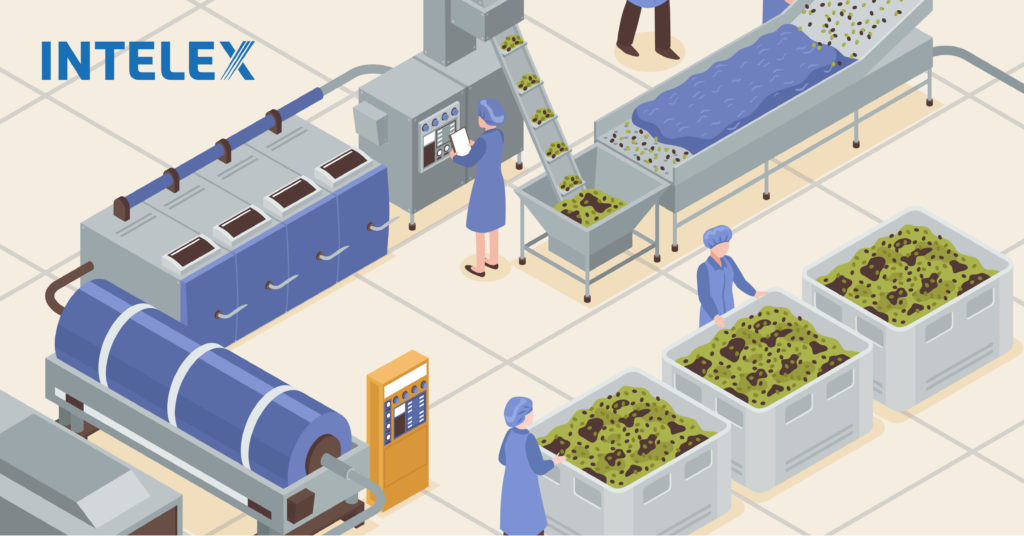
Creating a workplace that is striving to achieve and sustain safety performance success begins with one critical question: Is safety your organization’s principal value?
Achieving safety and health success is measured in various ways and with an ample set of metrics that quantify and qualify success. However, I would venture to guess that most organizations still look to a specific number of measures to define overall success: Metrics that measure loss, the time between failure, the duration of loss and the severity of the loss.
The reality is, most organizations still want to understand that loss and its severity are improving with time, and that’s okay. Yes, I said it: it’s okay.
Creating a workplace that is striving to achieve and sustain safety performance success begins with one critical question: Is safety a core value or better yet, is it the organization’s principal value? To define it in terms of safety and health, it’s the foundation upon which everything else is built. It’s easy to test, to see and yes, to feel when you land in it.
The attributes are many:
- You read it in things such as vision and mission statements when the senior leadership team is engaged and actively demonstrating their value.
- You see the plant manager and his or her direct team frequently on the manufacturing floor, learning from the frontline, and you understand safety is a critical metric – alongside other business metrics – in how the facility measures itself.
- Meetings start with safety, regardless of the meeting topic.
- You overhear chatter outside of work, like a maintenance contractor discussing how tough it was to work at your facility because safety is active, its value protected and the process governed.
- Safety is part of your employee objectives, and performance is measured and rewarded.
- You are stopped before making a poor decision by a co-worker and challenged on the safest way to perform, and yes, congratulated when you delivered safely.
- You feel it because it is real, it’s the norm and it’s “the way things are done around here.”
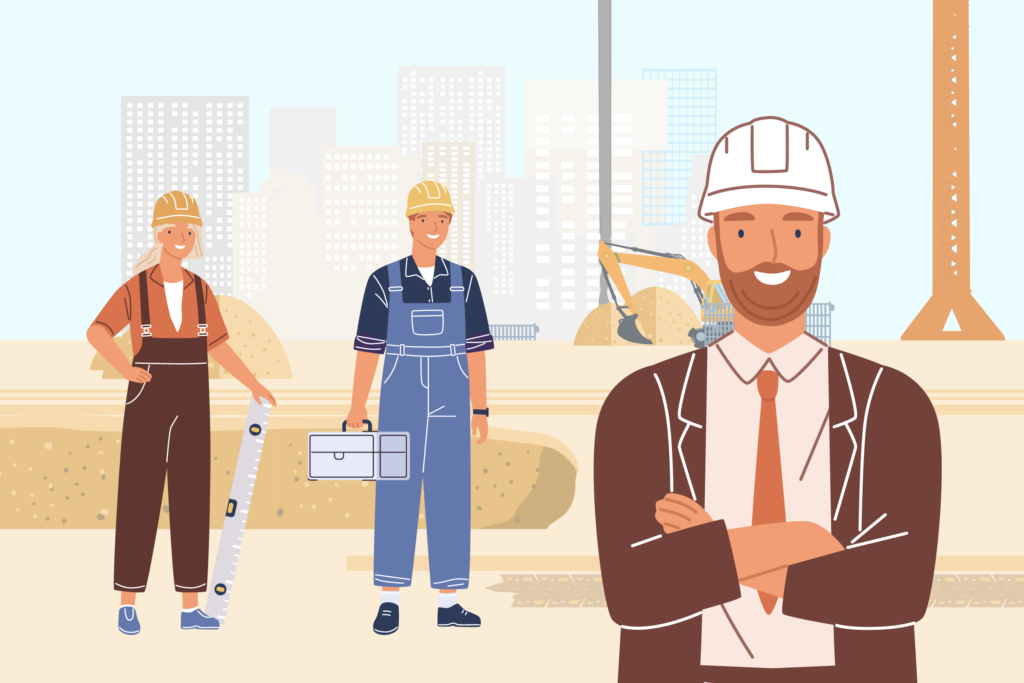
Empower the Safety Culture
In the past, organizations have been told that safety is a line-driven activity that must first be implemented at the bottom of an organization as a function of the management system and treated as a priority working its way to the top as a set of metrics. But the reverse is true; safety must start with an organization’s senior management team. Leadership must demonstrate an active commitment to safety and promote that commitment with passion throughout the entire organization. To improve the safety culture of an organization, the following should occur:
- The safety process must touch every person in the organization.
- Safety must be a permanent agenda item discussed at the start of every meeting.
- Every member of the organization must be held accountable for safety performance, but it starts with organizational leadership.
- Safety must be the operational fabric of a facility, not a separate function.
- Safety must be integral to every business activity.
OSHA concurs with this assessment, stating, “The best safety and health programs involve every level of the organization, instilling a safety culture that reduces accidents for workers and improves the bottom line for managers.” The agency adds, “When safety and health are part of the organization and a way of life, everyone wins.”
Under this approach, so-called “safety departments” do not exist. Safety professionals still have a vitally significant role, but it shifts to a resource function that empowers others through capability development and coaching and mentoring. The best safety programs are owned as shared accountability between the management team and the manufacturing line, utilizing cross-sectional employees on teams to develop and implement safety processes. Safety also must be aligned with all other business functions to ensure that it receives the resources and attention that it deserves.
Create Safety Leaders
To be successful, organizations should create career paths that turn employees into safety leaders by making sure that everyone is highly trained and motivated; not just to succeed, but to exceed expectations. Workers should be mentored to help them contribute to the safety process.
The organization also should develop a culture in which employees believe they can create and maintain a workplace free of illness and injury. The result of this investment will establish within workers a sense of ownership of the safety process and a shift within the organization from an independent to an interdependent culture. This can help drive employees to mitigate substandard behaviors and conditions, discuss the barriers laying within the work system and focus on eliminating the potential for injuries or lessening the effects of mistakes when they occur. Mistakes will occur.
According to OSHA, when a company’s safety culture is strong, “Everyone feels responsible for safety and pursues it daily; employees go beyond ‘the call of duty’ to identify unsafe conditions and behaviors and intervene to correct them.”
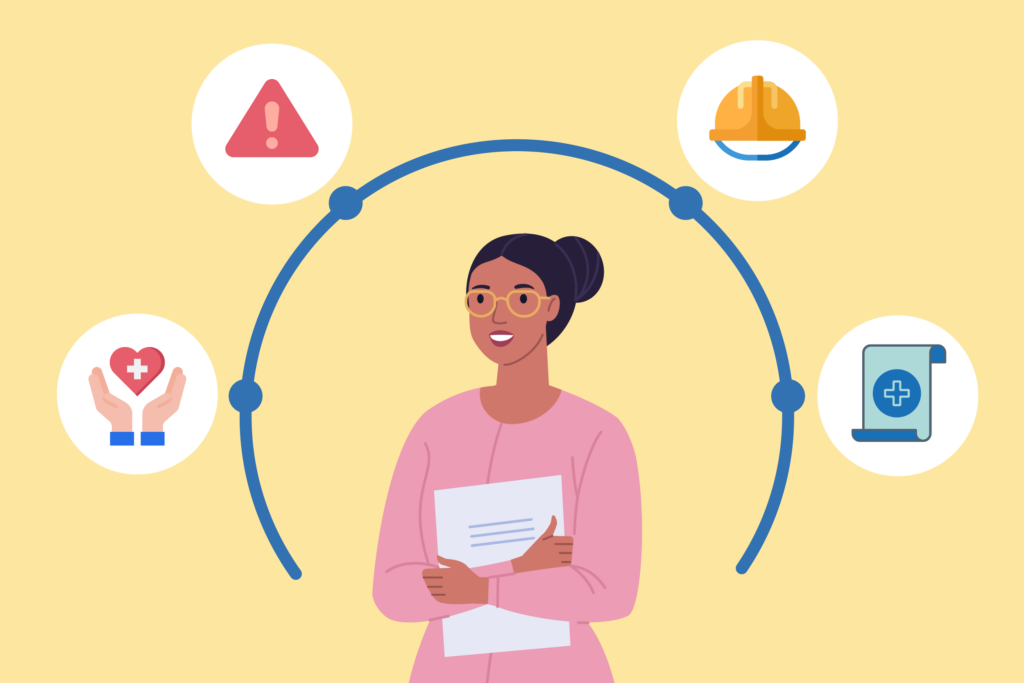
Develop a Process Model that Works
Adhering to a simple process model is a highly effective component of an overall strategy for improving an organization’s safety. The model below focuses on four aspects that are critical to creating a robust safety program:
Build safety leaders – Leaders must own and support the safety process wholeheartedly. They must communicate the importance of safety as well as the value and respect they have for the people who work in the organization. Besides, facility managers should meet regularly to review safety events and issues, track progress and establish future goals, teach safety training sessions and participate in mentoring.
Protect the physical environment – It’s essential to ensure that the overall environment is safe, equipment is properly cared for, operating practices are written and utilized and engineering standards are followed. To accomplish this, frequent audits and inspections that are specific to the manufacturing asset should be conducted. Design safety reviews of all equipment should be considered in a cradle-to-grave approach for ensuring the safety health of all equipment that poses a risk or loss. Establish extensive inspection programs to ensure compliance and be on the lookout for new technologies to reduce risk. Always ask yourself what you can do to make the physical workplace safer.
Invest in people – Investing in people is paramount to success. The best organizations will first seek to hire the right people and then develop their capabilities and skillsets. Be sure to include questions about safety as part of the hiring process, to understand a prospective employee’s knowledge of safety and to communicate your company’s commitment to safety. Also, require safety/loss control training for all manufacturing employees, assign mentors to new and transferred employees and provide annual written safety evaluations for all workers.
Embrace safe behavior and drive expectations – Changing organizational behavior is what transforms a facility from good to great. When passion for safety is driven by a leadership team, it filters to the manufacturing floor. It encourages workers to actively care about each other, fostering interdependence within the organization. The job of leadership is to mentor and coach employees to give themselves away in a way that builds others to care for the safety of the process. Teamwork is critical to success.
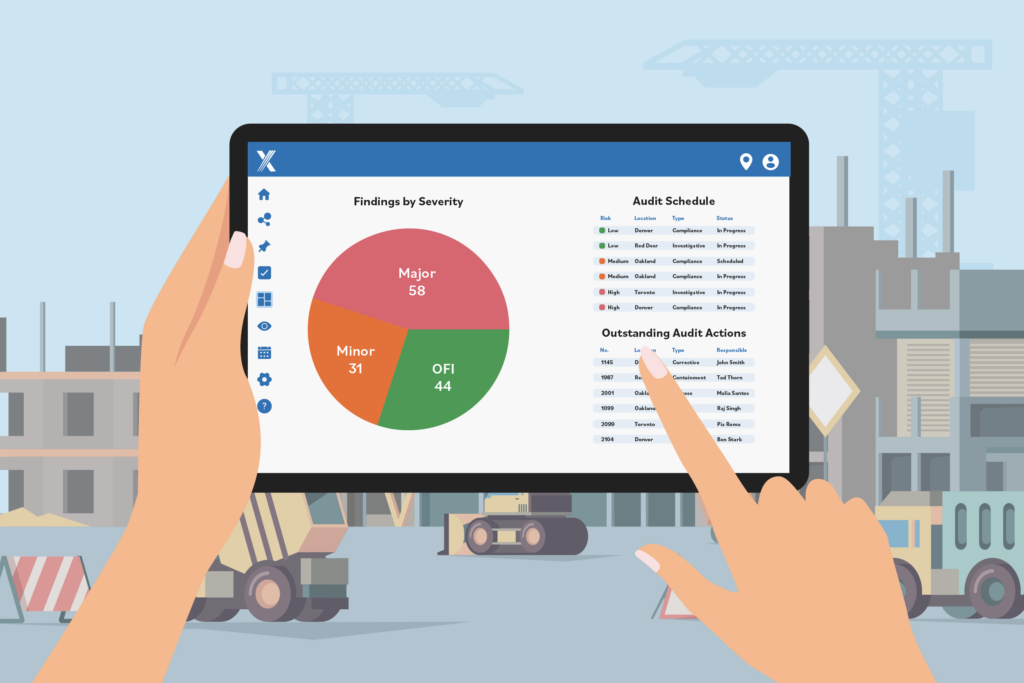
Supporting a Safety Program with Technology
A modern safety management system needs people, processes and technology to effectively minimize safety risk. With increasingly complex physical environments producing more safety data than ever before, the days of managing safety with spreadsheets are long over. Technology that manages data and helps maintain real-time communication is therefore an important part of a management system that supports a strong safety culture. It’s critical to have a robust technological solution that can analyze data from observations, incidents, audits and inspections to support leading indicators that prevent incidents from happening.
When frontline workers have access to mobile applications that provide real-time reporting of safety hazards, the management system collects significantly more data than it does if workers have to fill in paper forms or wait until they have access to a desktop. Workers can capture hazards immediately and submit the observation directly to the management system. Safety leaders can then send bulletins directly to workers’ mobile devices to augment their situational awareness, which helps them address hazards and correct unsafe behavior.
This feedback loop of real-time safety information helps frontline workers feel that they are partners in the safety culture. They participate in providing safety information and see how it positively impacts them and keeps their colleagues safe in the workplace. The result is frontline workers who take ownership of their safety and continuously look for opportunities to improve safety instead of waiting for top-down direction.
Conclusion
By following a simple process safety model and implementing the right technology, organizations can make good progress in achieving their goal of creating a safer workplace. But a successful safety program also must include honest self-inspection to support continuous improvement. This means building a system that enables production-level employees to communicate honestly to the most senior leader and vice versa. Measurement tools should also be established to help determine what is working and what is not. Don’t be afraid of failing or not reaching set goals. Finding mistakes will allow an organization to make changes and adjust the safety process to close any gaps.
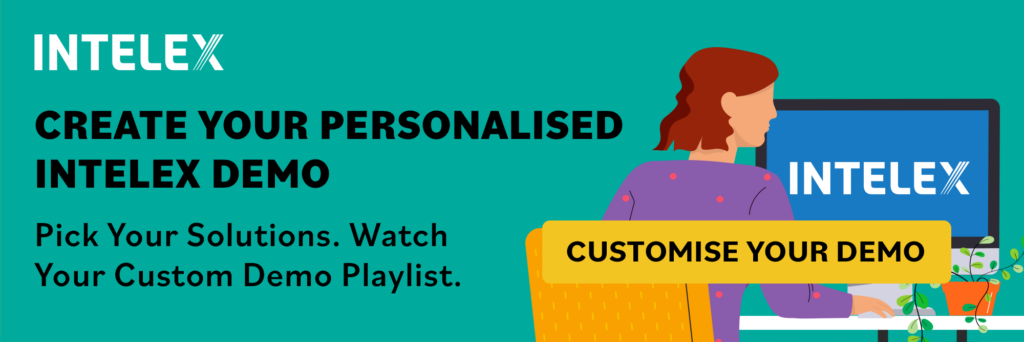