Loading Dock Safety: Integrating Risk Management, AI and Advanced Technologies
September 25, 2024
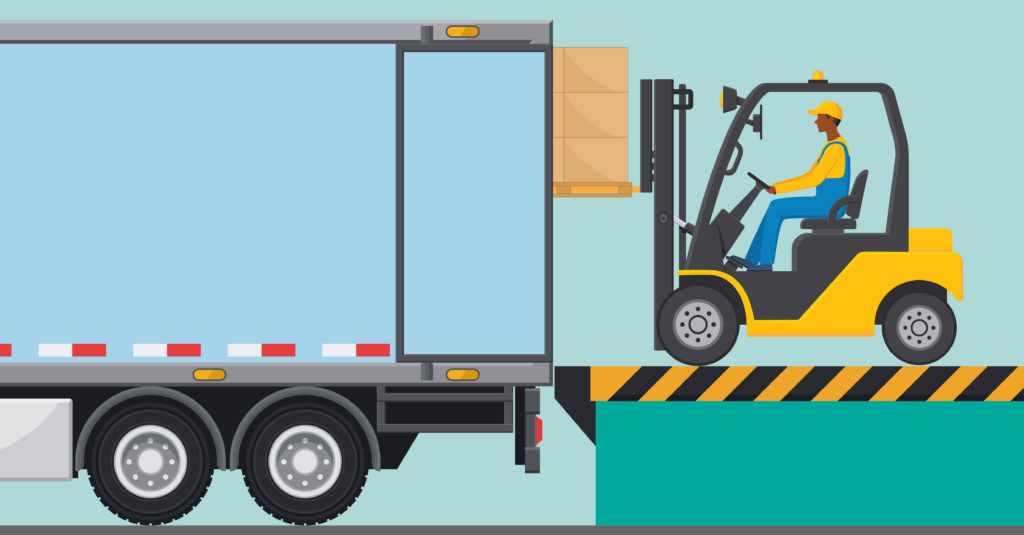
Loading docks are vital intersections in logistics where goods are transferred between trucks and storage areas. However, they also pose significant safety challenges that must be managed effectively to ensure a safe and secure workplace environment. This requires a multifaceted approach that includes traditional safety protocols and modern technology integration.
Foundational practices, such as workers trained in the proper loading and unloading techniques, and the use of personal protective equipment (PPE) is key. In addition, the implementation of AI-driven systems and advanced safety technologies, such as automated sensors and machine learning algorithms, can significantly reduce the risk of accidents even further. These technologies can monitor real-time activities, detect potential hazards and alert workers or shut down operations if unsafe conditions are identified. By combining human diligence with technological innovation, companies can create a safer and more efficient working environment at their loading docks.
In this blog post we explore various aspects of loading dock safety, from risk management and hazard prevention to the role of artificial intelligence (AI) and advanced safety technologies in enhancing workplace safety.
Effective Risk Management Strategies for Safer Loading Docks
Effective risk management is crucial for minimizing hazards at loading docks, where even minor oversights can lead to significant accidents. To mitigate these risks, it’s essential to first identify potential hazards, such as uneven surfaces, vehicle and pedestrian collisions and falling objects. This proactive approach requires more than just an initial assessment; it demands ongoing inspections and regular in-depth assessments to fully understand and address the dangers in loading dock operations. By conducting comprehensive risk assessments, companies can implement targeted control measures that reduce the likelihood of accidents and injuries, ensuring that every aspect of the loading process is as safe as possible.
Routine safety audits and inspections play a critical role in this process, serving as both a compliance check and a preventive measure. These audits help ensure that established safety protocols are not only followed but are also continuously updated to reflect new insights or emerging threats.
However, effective risk management goes beyond mere compliance; it’s also about fostering a culture of safety where continuous improvement is prioritized. This involves encouraging employees at all levels to actively participate in identifying and reporting potential hazards. By combining this human perspective with advanced tools such as predictive analytics and AI-driven monitoring systems, businesses can stay ahead of risks, creating a proactive safety strategy that adapts to changing conditions.
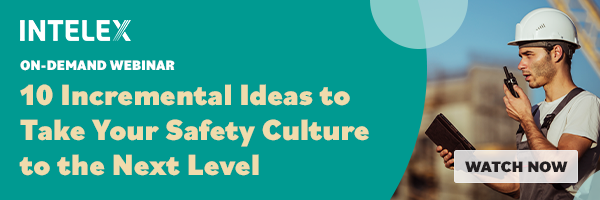
Proactive Measures for Preventing Loading Dock Hazards
Preventing hazards at loading docks requires a proactive approach that addresses both human factors and environmental conditions. This includes training on equipment operation, hazard recognition and emergency procedures. Regular refresher courses and practical drills can reinforce this knowledge, ensuring that all employees remain alert and prepared to handle any situation safely.
In addition to training, the loading dock’s physical environment plays a crucial role in hazard prevention. Implementing clear and visible signage is vital for directing traffic flow and alerting workers to potential dangers. Adequate lighting is equally important, as it ensures that all areas of the dock are well-lit, reducing the likelihood of accidents due to poor visibility. Designated pedestrian walkways that are clearly marked and separate from vehicle paths can greatly reduce the risk of collisions and other accidents.
Furthermore, regular maintenance of both equipment and infrastructure is essential. This includes keeping loading dock surfaces free of debris, ensuring that safety barriers and guards are functioning correctly and routinely inspecting and servicing equipment to prevent malfunctions.
Optimizing Loading Dock Safety with AI Technology
Artificial intelligence (AI) is increasingly playing a role in enhancing safety measures at loading docks. With AI-powered systems, loading docks can now benefit from real-time hazard detection and immediate response capabilities. For example, AI can monitor forklift movements and identify unsafe behaviors, such as speeding or improper loading techniques, triggering automatic alerts to interventions to prevent accidents before they happen.
One notable example of AI in loading dock safety is Protex AI. Protex AI integrates multiple safety technologies into a unified platform, using machine learning algorithms to predict potential hazards based on both historical data and real-time observations.
Building a Dynamic Safety Management System for Loading Dock Excellence
Overall, a robust safety management system (SMS) is essential for maintaining high safety standards at loading docks. It serves as the backbone of a company’s safety culture, integrating policies, procedures and best practices designed to identify, assess and mitigate risks. Key elements of a successful SMS include clearly defined roles and responsibilities, ensuring that everyone from management to frontline workers understands their part in maintaining a safe environment.
Incorporating a digital approach to safety management, such as utilizing software like Intelex, brings substantial benefits to this process. A digital SMS streamlines safety operations by providing real-time data and analytics, enabling companies to quickly identify potential hazards, track safety performance and ensure compliance with regulations. This technology facilitates more informed decision-making and allows for the seamless integration of AI-driven insights, which can further enhance risk management strategies.
Moreover, the best SMS is one that evolves—by continuously analyzing feedback and data, companies can refine and enhance their safety strategies, adapting to new challenges and ensuring their safety protocols remain effective and up to date. This commitment to continuous improvement not only protects employees but also enhances operational efficiency, creating a safer, more productive loading dock environment.
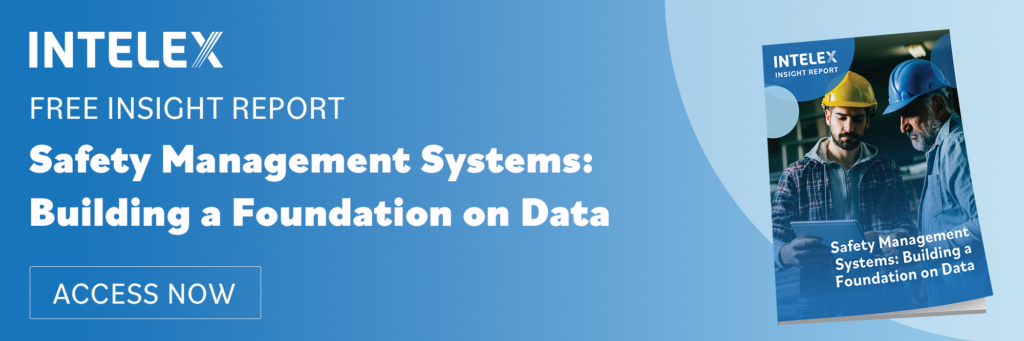
Using Advanced Technologies for Streamlining Loading Dock Safety
Recent advancements in safety technology have significantly improved how loading dock operations are conducted, making them safer and more efficient. For example, automated dock levers and vehicle restraint systems enhance efficiency while reducing risks associated with manual operations. In addition, sensor-based systems have emerged as a vital tool in monitoring environmental conditions, equipment status and personnel movements, helping to prevent accidents before they occur.
A Holistic Approach to Enhanced Loading Dock Safety
A holistic approach to loading dock safety involves proactive risk management, effective hazard prevention strategies and the integration of advanced safety technologies. Integrating AI-driven insights, such as Protex AI, and advanced technologies, such as sensors, into a digital safety management system like Intelex, allows organizations to significantly reduce risks while enhancing operational efficiency.
Continuous training and education also play a pivotal role in maintaining vigilance and ensuring that all personnel are informed about the latest safety protocols. This ongoing commitment to safety not only mitigates risks but also contributes to the organization’s long-term success and sustainability.
Ultimately, by prioritizing safety and investing in continuous improvement, companies can create a safer, more efficient loading dock environment, ensuring that employees can perform their duties confidently and securely. This comprehensive approach to safety not only safeguards employees but also strengthens the overall safety culture, leading to improved workplace efficiency and productivity.
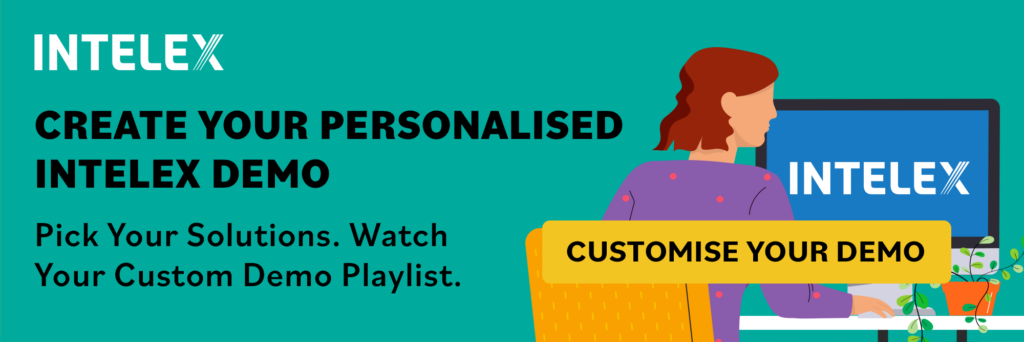