How to Use AI for Workplace Safety with Intelex and Protex AI
December 14, 2023
Artificial intelligence (AI) is changing how we manage workplace health and safety. As safety management becomes increasingly complex, AI can reduce the burden of collecting, logging and analyzing safety data. It can be beneficial for managing data associated with leading indicators, which can help prevent incidents before they happen.
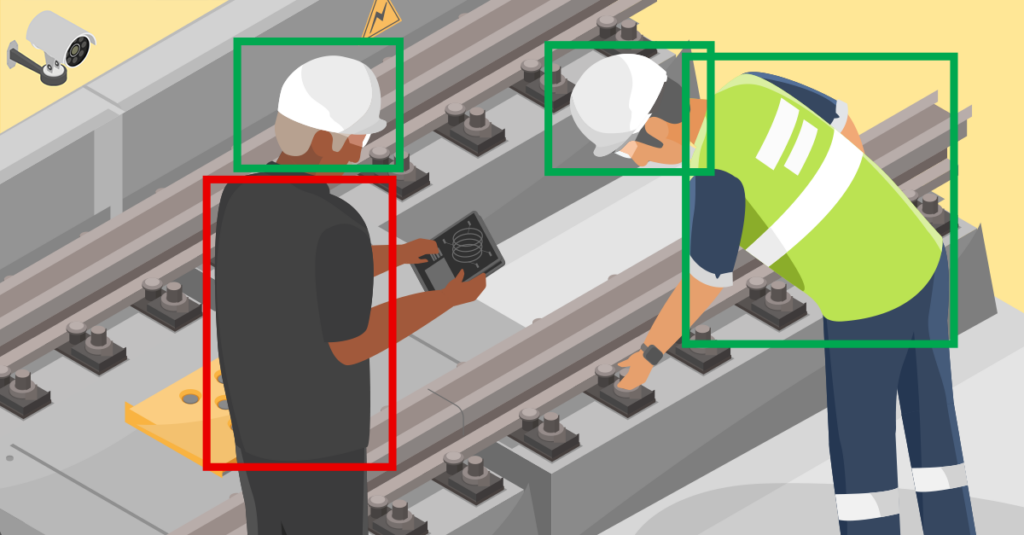
The partnership between Intelex and Protex AI marks a new stage in the evolution of workplace safety. Protex AI uses computer vision (CV) with AI, deep learning and closed-circuit television (CCTV) cameras to identify a range of safety hazards and events. It automatically categorizes events by hazard type, severity and more and then logs them in Intelex with all the key details. This allows safety leaders to capture events they would otherwise miss and streamlines the tedious task of incident and hazard reporting. Users can customize the event categories to determine which events they want Protex AI to send to the Intelex system. The result is enhanced visibility, better risk mitigation and improved safety KPIs.
In this blog written by Graham Freeman and Dave Rowland, we’ll look at how Intelex and Protex AI are enabling solutions that meet the challenges of today’s workplace.
What Is Proactive Safety?
Lagging and Leading Indicators
Safety has traditionally relied on lagging indicators, which are the data from previous incidents. Examples include incident rates, injuries and regulatory violations. Through incident investigations and various methods of root-cause analysis, safety leaders analyze the incident to understand what happened and why. The objective is to implement corrective actions to prevent the recurrence of such incidents.
Lagging indicators are important, but they have some shortcomings. First, the data for lagging indicators comes from incidents that have already occurred. The resulting corrective actions may prevent similar incidents from happening again, but that’s little comfort for injured workers. Further, as workplace safety improves because of corrective actions, incidents will go down, which means lagging indicators data will decrease. The result will be less data supporting dashboards or predictive models, which will produce a false impression of safety performance in the organization.
Leading indicators, on the other hand, precede incidents. They use activities like audits, inspections and observations to categorize potential workplace threats and to predict how they could culminate in incidents that cause fatalities, injuries or equipment damage. For example, regular observations of consistent events, such as pedestrians walking in vehicle-only zones, can highlight this as a high-risk activity that will eventually cause an incident. Armed with these leading indicators, safety leaders can implement corrective actions like training or communications to prevent an incident from happening in the first place.
A proactive safety culture is one in which leading and lagging indicators work together to prevent incidents and to derive insights from those that do happen. It is a two-way communication channel where regular observation data flows from the frontline worker to the management system. This process helps to track trends and communicate hazards back to frontline workers in real time. The constant flow of information into the management system helps safety leaders better understand the trends and behaviors that contribute to incidents, which is the first step in ensuring those incidents don’t occur in the first place.
The Human Factor
For a proactive safety culture to work effectively, participation from frontline workers is critical. Some leading indicators rely on continuous observations from the workers who are most likely to see high-risk behaviors or potential incidents. In a perfect workplace, frontline workers would have mobile devices that allow them to make real-time observations that go to the safety management system for tracking and communication.
However, the reality is that even frontline workers don’t see everything. In complex environments, such as manufacturing floors, the hectic pace of work means workers don’t always have the situational awareness to see and report every safety infraction or near miss. They might also lack the incentive to submit observations because they don’t have the training to understand the nature and category of the infractions they see. Many workers also report feeling that the organizational safety culture doesn’t support observations, making workers feel as though they are creating conflict by informing on their colleagues.
While there is ample technology on the market to help collect data for leading indicators, these tools are not a catch-all solution. Some technology, such as wearables, requires workers to switch them on, wear them correctly and never take them off. Predictably, workers don’t always do those things. Other organizations might do an excellent job of obtaining data from frontline workers but do a less-than-excellent job of managing that data, reporting it and communicating the results back to the workers who most need it to stay safe.
How Can Intelex and Protex AI Help?
A digital safety management system built with Intelex and Protex AI provides the continuous flow of data and analytics today’s organizations need to support a proactive safety culture.
Protex AI uses existing CCTV cameras and AI to continuously monitor the work environment and log activities that could lead to incidents. It provides a collection of precise rules and business logic to capture and categorize hazardous workplace activities, such as when workers are too close to moving objects, when vehicles are moving too quickly or when pedestrians are walking in vehicle-only zones. It can also show when workers are violating safety protocols by engaging in dangerous physical activity or when they are not wearing required personal protective equipment (PPE).
Protex AI augments human situational awareness by providing visibility into the activities workers don’t always see. It also eliminates the potential for bias and overcomes any hesitation workers may have in reporting observations using a mobile device. Instead, Protex AI supports reliable and continuous monitoring of the workplace. It anonymously captures minor safety lapses and categorizes them in the Protex database. Safety leaders can then implement corrective actions such as more training or safety controls to prevent incidents before they take place. Frontline workers don’t have to worry about turning it on or charging it, and they don’t have to train how to use it. Instead, Protex AI is a collaborative tool that operates alongside frontline workers to help prevent safety incidents.
Protex AI has been a critical part of the safety success story of Marks & Spencer, a UK retail organisation. After deploying Protex AI as part of its existing CCTV system, Marks & Spencer saw a 40 percent decrease in unsafe events within the first two weeks and 80 percent in the first three months. By capturing events with computer vision, safety leaders could take corrective action by enhancing training and controls, which supported the ongoing development of the organizational safety culture.
Protex AI can send safety data directly into the Intelex safety management system. Safety leaders then use Intelex dashboards and reports populated with data from Protex AI alongside other data within Intelex to get deep insights into the safety performance of their organization. With Protex AI capturing unreported behaviors and minor events, the Intelex safety management system can produce analytics with much greater depth and accuracy.
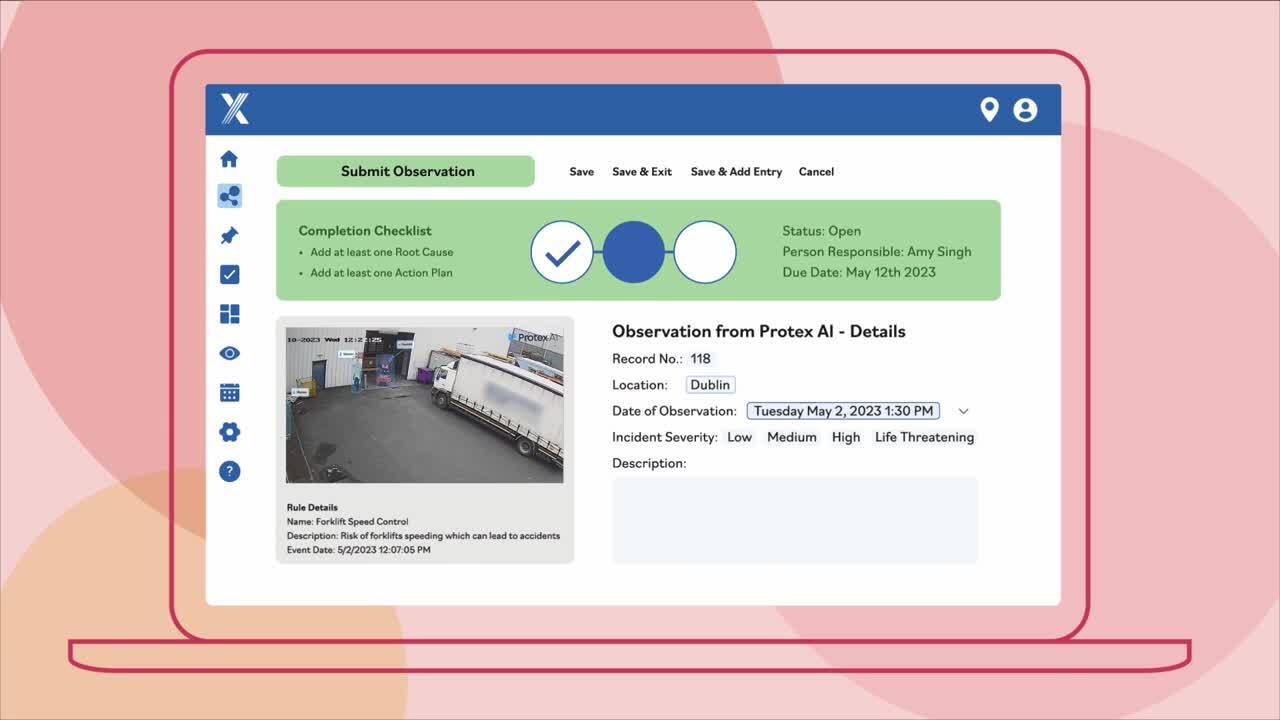
Use Case: Warehouse Safety
Warehouses are critical components of the global supply chain. They house hundreds of workers and machines in constant motion as they receive and send items. As a result of the frequent interaction of people and machinery, the relentless pace of work and the strenuous physical labor of the job, warehouses are high-risk environments for safety incidents. How would Protex AI and Intelex help to create a safer work environment in a warehouse?
Protex AI is the first stage of this approach. The warehouse safety team categorizes the actions it wants Protex AI to look for. Protex AI then uses the existing CCTV system to monitor the workplace, looking for those actions. The Intelex system records those actions and, if necessary, flags them for investigation and root cause analysis. Safety leaders then create controls to mitigate risk. Intelex can measure the effectiveness of these controls by assessing residual risk or tracking improvements in leading and lagging indicators.
Integrating AI Solutions for Enhanced Safety Culture
Cutting-edge technology is not a magic solution to every problem, especially in workplace safety. Building a strong safety management system requires effective planning, processes and communication for technology to provide the efficiency and analytics the modern workplace needs. People will always be the foundation of safety culture in every work environment.
However, with workplaces becoming even more complex, augmenting human situational awareness with advanced technology like Protex AI and Intelex is critical for ensuring organizations meet evolving safety challenges. AI solutions and data analytics hold the promise of making today’s workplaces safer. With a strong safety culture and a digital safety management system supported by Protex AI and Intelex, we are closer than ever to ensuring every worker gets home safely each night.