Proactive Safety: How to Build a Culture of Prevention and Employee Engagement
May 3, 2024
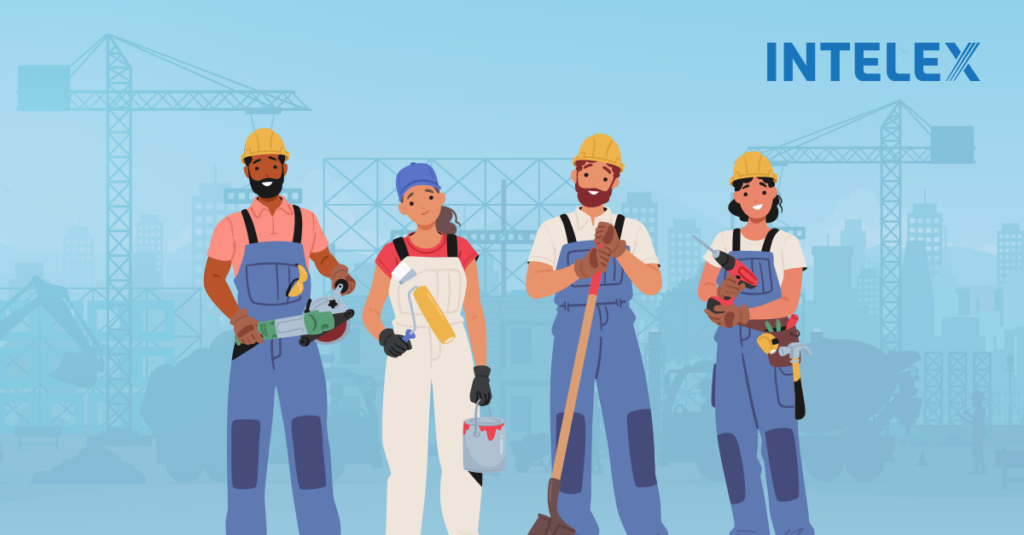
In an ideal world, every worker would come home safe and healthy at the end of the day. The reality is, however, that work environments are constantly evolving and becoming increasingly complex, introducing new challenges to employee safety and well-being. When organizations fail to manage these risks and changes effectively, this can compromise the overall safety of the workplace and potentially lead to injuries or even fatalities.
The U.S. Bureau of Labor Statistics reported 2.8 million injuries and illnesses in 2022, nearly 5,500 of which were fatal. When we consider that at least 80% of all incidents can be attributed to human factors involving individuals, organizations and working conditions, it is clear that safety management programs must prioritize prevention and proactive strategies to improve workplace outcomes and build a strong safety culture.
Today, a new generation of data-based tools is transforming safety from reactive to proactive, aiming at preventing injuries and fatalities before they happen. In this revolutionizing shift, organizations are using leading-edge technology and advanced analytics to assess data and improve safety standards with the active involvement of frontline workers. This blog examines how proactive safety strategies—supported by risk assessment, analysis of key data from leading and lagging indicators, employee engagement and advanced technology—create more secure work environments.
Understanding Proactive Safety and Its Key Elements
Proactive safety adopts a forward-thinking approach to identify and mitigate potential hazards before they become incidents, contrasting with reactive measures that address issues after they have taken place. To achieve this, organizations use advanced technology to optimally analyze data, which empowers safety professionals to spot patterns and implement corrective actions preemptively. This strategy’s main objective is to greatly decrease workplace injuries and fatalities, striving for zero harm.
A proactive safety program has a few key elements that are critical to creating a safe and secure work environment. These include conducting thorough risk assessments, prioritizing leading over lagging indicators as key data points, enhancing employee engagement and ensuring continuous improvement.
Risk Assessment and Hazard Identification
As a major component of proactive safety, risk assessment seeks to identify and evaluate hazards in the work environment ahead of incidents occurring, determine the level of danger in those hazards and assess the likelihood of harm that may occur. Risk assessment is the key principle behind Job Safety Analysis (identifying potential hazards associated with specific job tasks and developing preventive measures) and Job Hazard Analysis (a more comprehensive analysis that includes not only hazards but also potential risks and their management strategies).
In risk assessment, safety leaders use a risk matrix as an essential tool for evaluating and estimating the level of risk associated with identified hazards. It is valuable to determine whether potential risks are acceptable by scoring them and plotting these scores on a matrix chart. If a hazard’s risk rating escalates above acceptable levels, the matrix guides the implementation of effective measures to mitigate these risks. Essentially, risk assessment equips organizations with the right instruments to convert safety data into predictive safety models, ultimately helping to prevent incidents.
The Role of Data: Leading vs Lagging Indicators
Central to risk assessment and hazard identification is a critical indispensable element—data. Today, safety leaders in organizations have unrivaled access to massive datasets they can use to assess and mitigate hazards and incident rates. The metrics they collect fall into two main categories: leading indicators, which predict future events, and lagging indicators, which reflect past performances.
Traditionally, organizations have focused on analyzing lagging indicators, resulting from methods like root-cause analysis, incident investigations and corrective actions. Examples of lagging indicators include injury rates, lost workdays and equipment damage costs. As indicative as these metrics can be, they have a major drawback: they are retrospective, as they only measure incidents, fatalities and damages after they have occurred.
Recognizing these limitations, organizations are increasingly adopting leading indicators in their safety programs. By relying on metrics gathered from audits, inspections and observations, safety professionals can access actionable data to evaluate potential risks before they escalate into incidents. Organizations now implement holistic strategies in their safety programs that utilize both categories of indicators while prioritizing leading ones, which enables them to move beyond merely responding to past events and proactively enhance their safety performance.
Employee Engagement: Frontline Workers as Stakeholders
Actively involving frontline workers, who typically face the highest risks of incidents, is another key element of proactive safety. Organizations empower their workforce by providing relevant training, timely information on work-related issues and enabling open communication of safety concerns and suggestions. For example, frontline workers can now report near misses and other safety issues directly into an app-based safety management system using mobile devices, a functionality that works even in areas without internet availability.
In this approach, employees are active stakeholders in safety practices. They become an integral part of a bi-directional communication channel in which they are receivers and transmitters of critical safety data. This input from the frontlines provides organizations with actionable insights, serving as leading indicators that help to strengthen safety protocols and enhance the overall safety management system.
When workers feel engaged, they are more likely to be committed to their jobs and to contribute to the overall safety in the organization. As the ABC 2023 Safety Performance Report in construction shows, there is a marked decrease in workplace incidents when workers participate actively in the safety management system. Involving employees in reporting observations led to a 44% improvement in the Total Recordable Incident Rate (TRIR) and a 48% reduction in the Days Away, Restricted or Transferred (DART) rates. Safety outcomes in organizations can clearly benefit only if employees feel engaged and empowered.
Continuous Improvement: The Key to Ongoing Success
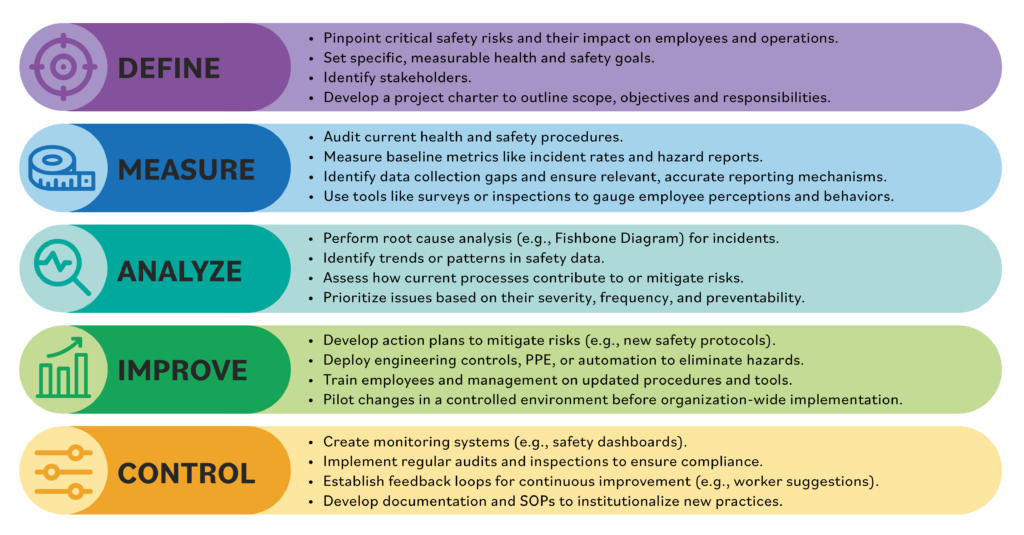
Beyond engaging employees, effective proactive safety is deeply rooted in an organization’s dedication to continually improving its safety programs. For a leading indicator program to succeed, it requires a clear vision, usually spanning a 2-5-year period, a straightforward strategy defining the logic for achieving that vision and a detailed plan outlining the specific steps to implement the strategy.
By embracing frameworks such as the DMAIC approach—comprising Define, Measure, Analyze, Improve and Control—in their safety programs, organizations can systematically refine their processes to enhance performance and achieve sustainable results. This involves a cyclical process of setting clear goals, collecting actionable data and analyzing findings. Once safety leaders are equipped with the right information, they can implement improvements and establish the right controls. Through this ongoing process, organizations can build a strong safety culture, guided by the principle of “Get Better Every Day.”
Advancing Proactive Safety through Technology
Today, proactive safety management programs integrate leading-edge technology to monitor hazards in real time, predict potential risks and deploy effective mitigation strategies faster than ever before. Artificial Intelligence leads these advancements with predictive analytics that foresee and prevent workplace incidents by enhancing decision-making processes. The Industrial Internet of Things (IIoT) further revolutionizes safety by integrating equipment and sensors for live monitoring and hazard detection. Machine learning algorithms refine these processes, learning from data to ensure continuous improvement of safety outcomes.
Beyond these, more and more organizations employ wearable devices to access real-time data and advanced analytics, enhancing operational safety. Augmented reality further supports this by simulating potential hazards and training scenarios to help workers improve their hazard recognition skills, decision-making abilities and emergency responses, ultimately decreasing accident risks and boosting workplace safety.
Intelex – A Strategic Partner in Proactive Safety
As a leading global provider of cloud-based EHS (Environment, Health and Safety) management software, Intelex adopts cutting-edge technology in its suite of applications to support organizations in reducing incident rates and enhancing their proactive safety culture.
Key components of this suite are Job Safety Analysis Software and Safety Observations Management Software. Job Safety Analysis enables safety leaders to conduct comprehensive hazard analyses across the organization. Through categorizing risks and using a configurable risk matrix, it assesses the likelihood and impact of potential threats. Safety Observations Management makes it easy for workers to accurately record and submit safety observations concerning behaviors, activities or situations in the field to proactively prevent workplace incidents.
Incident Reporting Software and Near Miss Reporting Software are two other essential tools for data gathering from the frontlines. Incident Reporting makes it easy to capture, analyze and prevent workplace incidents, including illnesses and injuries, environmental hazards and property damage. Near Miss Reporting empowers organizations to proactively identify and eliminate environmental, physical and behavioral risks and hazards by engaging frontline workers to record near miss data in real time.
Audit Management Software is another key application for developing proactive safety measures. It enables safety leaders to create a detailed structure for internal and external audit activity and data, with recurring and ad hoc standard audits for individual or multiple locations. This application is instrumental in reducing risks and streamlining audit processes by empowering effective risk management and enhancing regulatory compliance.
Case Study: Kloeckner Metals
Kloeckner Metals Corporation is a leading US-based enterprise specializing in full-line manufacturing, production and service center operations within the metals industry. Supported by a workforce of 2,200 people, Kloeckner Metals offers an extensive array of metal products, ranging from hot-roll items to structural materials, sheets, pipes and plates.
Following the phased implementation of Intelex Job Safety Analysis, Safety Incident Management, Action Plan Management and Audit Management applications, Kloeckner saw significant improvements in key safety metrics: a 55% improvement in OSHA recordables, a 43% reduction in restricted duty cases and a 62% decrease in lost-time injury cases.
These improvements also significantly boosted worker engagement. The company saw a 61% increase in employee participation in safety activities, a 26% rise in employees feeling empowered to take action in safety and a 56% improvement in satisfaction with the organization’s EHS environment.
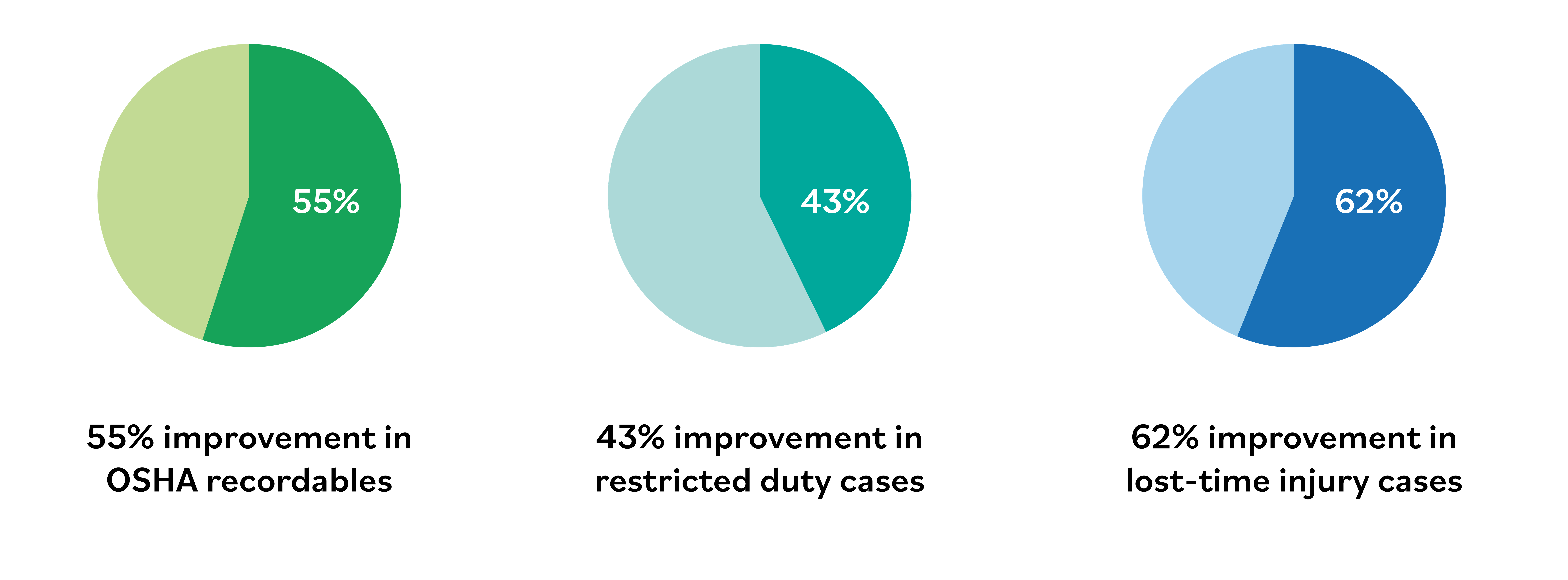
Figure 1: Kloeckner Metals’ Safety Performance Improvement with Intelex
Building a Robust Proactive Safety Culture: The Win-Win Strategy
In today’s world, businesses recognize that building a proactive safety culture is not only a strategic win-win for employers and employees but is also a major competitive advantage. According to Intelex’s global research, 75% of European organizations indicated they could lose business to competitors who can better demonstrate how they are improving health and safety. In North America, this number stands at 86%.
These findings highlight a significant pressure for organizations: not only to uphold EHS standards but also to surpass them by applying a strong, proactive approach to safety. Beyond preventing accidents and injuries, this approach enhances the overall workplace environment, boosts employee engagement and improves the organization’s performance and reputation.
As our world evolves, driven by new economic realities and technological advancements, organizations must continually evaluate, update and improve their safety programs to meet new workplace demands and emerging risks. By developing a proactive safety culture, supported by cutting-edge safety management programs, companies not only set themselves up for success but also build their reputation for corporate responsibility and commitment to their workers’ well-being. This focus on continuous improvement and forward-looking safety strategies ensures that organizations are resilient enough to adapt and prosper within the dynamic industrial landscape.
Take the next step in building a proactive safety culture! Watch our on-demand webinar, The Five Elements of a Successful Data-Driven Safety Culture, to explore how key data insights and proven strategies can elevate employee engagement, prevent incidents, and drive a culture of prevention.