HelloFresh Is Using Quality Management Technology To Reduce Costs and Improve Efficiency
September 14, 2020
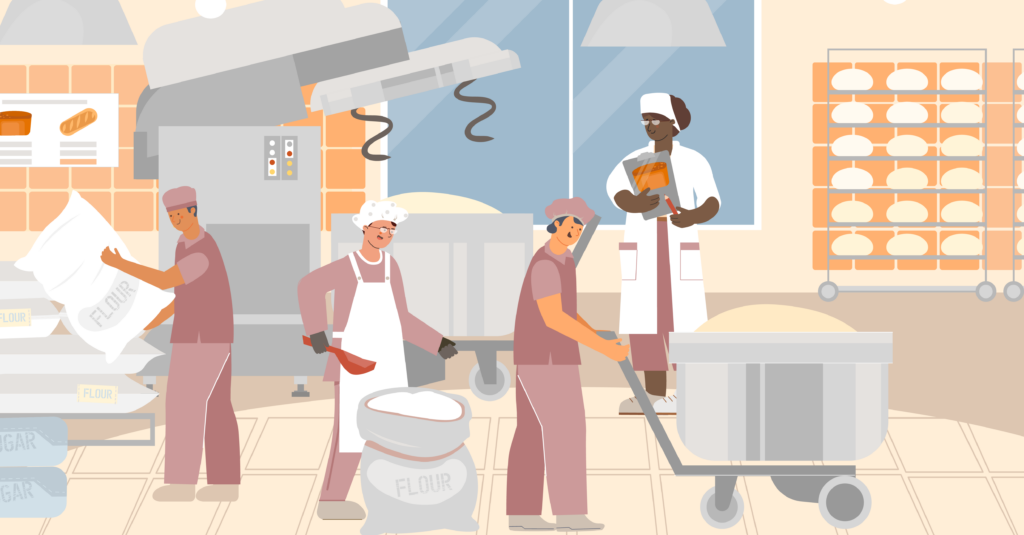
When families are counting on you for dinner, an unreliable supply chain is not an option. HelloFresh focuses on every step of the farm-to-door journey, shipping meal kits to millions of Americans, each filled with all of the ingredients necessary to prepare three to five different meals.
I recently found out how HelloFresh is using technology to reduce waste, improve quality processes and streamline supplier relations, all while doubling orders and revenue year-over-year.
It’s estimated that 40 percent of the food supply in the United States goes to waste because of over-portioning and wasteful distribution. Because of the attention to correct portioning, HelloFresh reduces the dinner food waste of its customers by at least 21 percent, resulting in a staggering reduction of food waste each week.
The company has over 2,500 employees in the United States who provide millions of meals that are carefully planned, carefully sourced and delivered to the front door of each subscriber at the time most convenient for them. Behind the scenes, a huge, data-driven technology platform acts as the engine that drives the business. This allows them to consistently manage supply chains and demand, and to optimize the customer experience as well as their business.
“The most essential part of this process is that procurement, quality, culinary and menu planning are constantly working together to ensure menus are designed to optimize seasonality. Then, on the back end of that, procurement is working with suppliers to get the highest quality product, followed by receiving inspection verifying incoming product to standards above and beyond regulatory requirements,” said Tim DeWolfe, Associate Director, Quality Systems at HelloFresh.
HelloFresh, which is the leading global provider of fresh food at home, turned to Intelex, the global leader in environmental, health, safety and quality (EHSQ) management software, as part of the company’s journey to optimize customer experience and improve supplier relationships. The Supplier Quality Management Team at HelloFresh is using Intelex to follow documentation requirements, conduct audits and follow up on supplier corrective actions to ensure families across North America can whip up delicious dinners.
“The partnership between HelloFresh and Intelex has given us the opportunity to take an out-of-the-box tool and mold it to our needs,” DeWolfe told me. “Through the last two years with Intelex, we’ve set up a document management system that supports Safe Quality Food (SQF) requirements. We’ve transitioned from a costly supplier management tool that lacks internal oversight to true internal Supplier Quality Management with audit functionality with Intelex, allowing us to focus time and effort to implement real corrective actions for some of our recurring problems.”
In 2017, HelloFresh became the first meal kit company to be SQF (Safe Quality Food) certified at all locations. This initiative required the backing of the director of quality, VP of operations, COO, CEO and president. When it was completed, it was celebrated throughout the company, since multiple functions beyond food safety were involved. The SQF certification was important to the company because it provides a competitive advantage, provides a framework for food quality efforts and helps DeWolfe and the Quality team organize priorities.
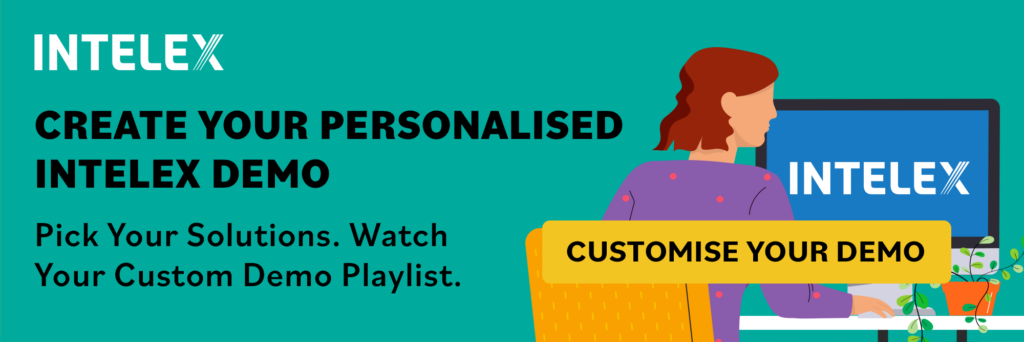