The 5 Biggest Safety Imbalances Holding Organizations Back — And How to Fix Them
April 15, 2025
10 minute read
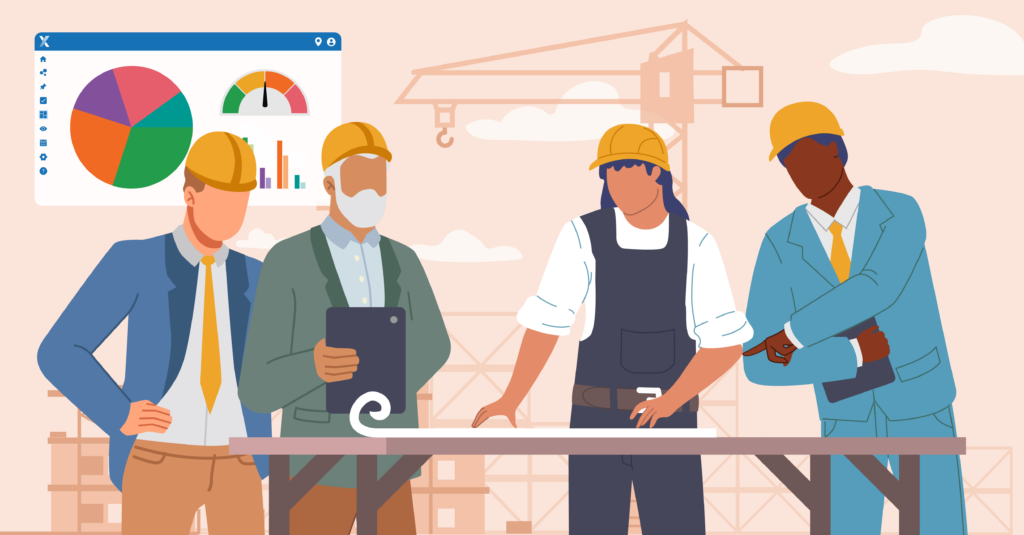
Introduction: The leadership imperative in safety
The father of modern management, Peter Drucker, once said, “Efficiency is doing things right; effectiveness is doing the right things.” This distinction is particularly relevant in safety management.
Many organizations emphasize compliance—ensuring they are doing things right—but authentic safety leadership ensures they are doing the right things to protect workers, embed safety into business strategy, and drive continuous improvement.
In my book, From Participation to Partnership – A Journey to Safety at the Front Line, I underscore the fact that the most effective safety programs are not built on compliance alone.
Trust, collaboration, and a deep connection with the workforce are equally crucial. The journey from engaging employees in safety to making them true partners in the process is the key to sustaining long-term safety excellence.
However, many companies still grapple with safety imbalances, where one aspect overshadows others. A truly balanced safety strategy integrates multiple dimensions of workplace safety, ensuring no single aspect dominates at the expense of others. This balanced approach is the cornerstone of sustainable workplace safety and a beacon of hope for organizations striving for safety excellence.
Table of contents
The evolution of workplace safety: How did we get here?
To appreciate the importance of balanced safety strategies, it helps to understand the historical context of safety.
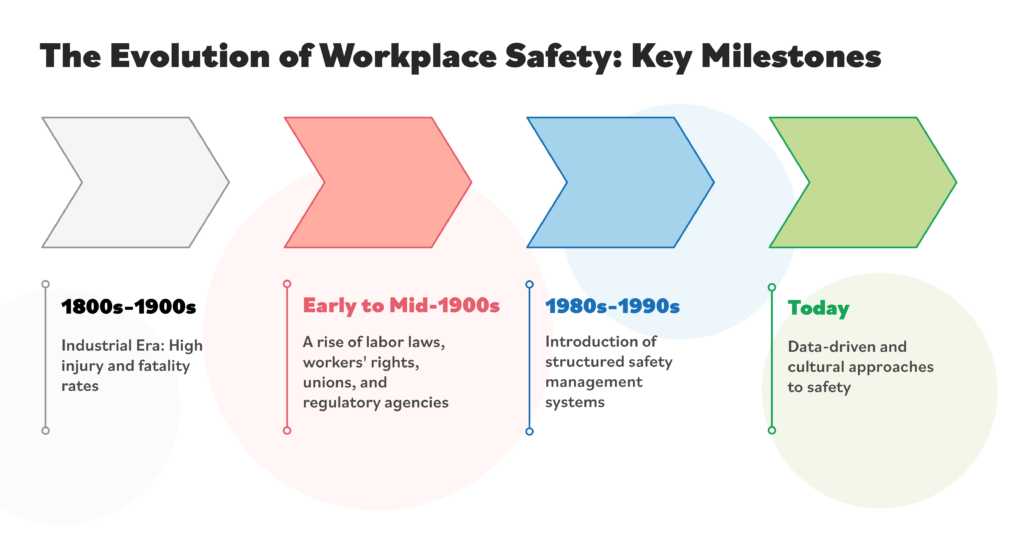
- Industrial Era (1800s–1900s): Safety was nonexistent in many industries, with high injury and fatality rates. Regulations were minimal, and employers often prioritized production over worker well-being.
- Early to Mid-1900s: A rise of labor laws sparked by tragic workplace disasters such as the 1911 Triangle Shirtwaist Factory Fire, led to the establishment of workers’ rights, unions, and even regulatory agencies that would follow like OSHA (Occupational Safety and Health Administration).
- 1980s-1990s: Organizations began implementing structured safety management systems such as ISO 45001, integrating safety into operational processes.
- Today: We have seen a shift toward data-driven and cultural approaches to safety. Modern organizations embrace analytics, predictive safety measures, and cultural transformation as key drivers of safety success.
These changes demonstrate why organizations must evolve beyond compliance and adopt a balanced, people-centered, and technology-enabled approach to safety.
The pressures that disrupt safety balance
Despite advancements in workplace safety, business priorities often conflict with safety objectives.
- Efficiency pressure: Forces organizations to meet deadlines and maximize productivity, sometimes at the expense of safety measures.
- Cost pressure: Limits training, equipment, and new technology investment or is directed to production-related activities.
- Innovation pressure: Prioritizes speed and production over safety considerations.
- Fatigue pressure: From increased workloads and long shifts leads to decreased focus and higher risks of incidents.
- Conflicting leadership priorities: Including market expansion, talent acquisition, operational priorities, and crisis management, may divert attention and resources away from safety programs.
Much like a tower of Jenga blocks, a well-designed safety management system remains stable until integrity is compromised.
When business pressures force companies to remove critical safety elements, collapse becomes inevitable. The challenge for safety leaders is finding the right balance between these competing pressures while maintaining a strong safety culture.
Implementing a balanced safety strategy is not without its challenges. It requires:
- A shift in mindset
- Significant investment in resources
- A commitment to continuous improvement
However, the benefits, in terms of improved safety performance and business success, far outweigh these challenges.
Five key areas of safety imbalance
An organization’s most significant challenge is ensuring that its safety programs maintain equilibrium across multiple competing priorities. Many struggle to balance:
- Compliance versus culture
- Incident management versus risk mitigation
- Office administration versus field engagement
- Data collection versus data insight
- Short-term safety actions versus long-term planning
Below, let’s explore these five common areas of imbalance and real-world case studies demonstrating how organizations have successfully
1. Compliance vs. Culture: The Case of Alcoa & Heraeus
Many organizations focus heavily on compliance, ensuring adherence to regulations, policies, and audits. While compliance is necessary, it does not drive engagement or proactive safety behaviors.
Alcoa, under the leadership of Paul O’Neill in the late 1980s, demonstrated how prioritizing safety culture could lead to broader business success. O’Neill implemented a policy allowing workers to stop production if they noticed a safety risk. Safety became the first discussion point in all executive meetings, and Alcoa invested heavily in risk mitigation.
As a result, the company’s injury rates dropped by more than 75%, productivity improved, and Alcoa’s market value grew from $3 billion to $27 billion during his leadership period. Paul O’Neill led Alcoa with the value of safety, the marker for which he would assess success.
Similarly, Heraeus, a global technology company, recognized the need to transform its safety culture. In 2019, the company adopted Intelex’s safety management system, which increased process transparency and supported day-to-day operations. As a result, Heraeus reduced Lost-Time Incidents (LTIs) by 10% in Germany and 40% in the United States between 2020 and 2021.
These case studies highlight that organizations must move beyond compliance-driven models and embrace a culture of safety ownership, where workers feel responsible for their safety and that of their peers. Focusing on safety partnerships deep in an organization leverages better compliance, and both go hand in hand with success.
Read our newest report How to Make Compliance Work for Your Safety Culture (Not Against It!) for more ideas.
2. Managing Incidents vs. Mitigating Risks: The SUEZ Model
Many organizations invest significant resources in investigating incidents but fail to allocate equal attention to preventing them.
SUEZ North America, a water services company, sought to improve safety by implementing an automated system to capture, report, analyze risks, and correct hazards across its facilities. By adopting Intelex’s EHSQ digital solution, SUEZ:
- Increased reporting by ten times, resulting in earlier risk identification and prevention.
- Achieved a 24% decrease in its Days Away, Restricted, or Transferred (DART) rate.
- 41% reduction in its Workers’ Compensation Experience Modification Rate (EMR).
These results underscore the critical importance of proactive risk management.
Instead of waiting for incidents to occur and then reacting, companies must invest in hazard recognition, frontline safety engagement, and leading programming. This proactive approach to safety not only mitigates risks but also promotes a culture of safety and a healthier workplace. It’s a call to action for safety professionals, organizational leaders, and HR managers to be proactive and vigilant in their safety strategies.
3. Office Administration vs. Field Work: The Role of Leadership Presence at George’s Inc.
Safety leaders often become consumed with safety-related paperwork, compliance reports, staff meetings, and other activities, which can lead to a disconnect from the realities of frontline work.
George’s Inc., a major poultry producer, realized that its manual safety processes hindered its ability to identify risks proactively. By implementing Intelex’s EHSQ Platform, George’s Inc.:
- Strengthened its safety culture.
- Improved worker engagement.
- Greatly enhanced connection to the frontline where better communication was warranted.
These changes led to a 54% reduction in the company’s DART rate.
This case study underscores the importance of leadership presence in safety programs. Safety professionals, supervisors, and even senior leaders must spend time in the field, engaging directly with employees to understand their challenges and address hazards in real-time.
4. Collecting Data vs. Using Data: Thales’ Data-Driven Safety Insights
Collecting vast amounts of safety data is meaningless unless translated into actionable insights.
Thales, a global technology leader, needed a digital solution to handle large-scale data collection and analysis. By adopting Intelex’s system, the company processed more than 215,000 safety indicators across its sites, allowing for more precise predictive analytics and better decision-making.
Organizations must ensure that their safety data is not just collected but actively used to drive improvements. Predictive analytics, AI-driven risk detection, and intelligent dashboards can help leaders identify patterns, intervene early, and prevent incidents before they occur.
Thales has been able to use its data differently, allowing it to prescribe better safety process features and make its sites safer.
5. Immediate Actions vs. Long-Term Planning: The Need for Strategic Foresight at Moss
Balancing short-term incident response with long-term strategic planning is crucial for sustaining safety excellence.
Moss, a leader in the construction industry, integrated safety, risk, and claims management into a single platform using Intelex’s software. This approach allowed the company to improve safety reporting, enhance risk assessment, and develop a long-term workforce safety strategy.
Sustainable safety programs require organizations to address immediate hazards while continuously improving their systems and aligning safety goals with broader business objectives.
How technology like Intelex helps create sustainable safety balance
Technology has become a crucial enabler of safety balance in modern organizations, ensuring that safety management is effective, efficient, proactive, and deeply embedded in the organizational culture.
Digital safety management solutions, such as those provided by Intelex, help organizations achieve sustainability in their safety programs by addressing the key imbalances discussed earlier.
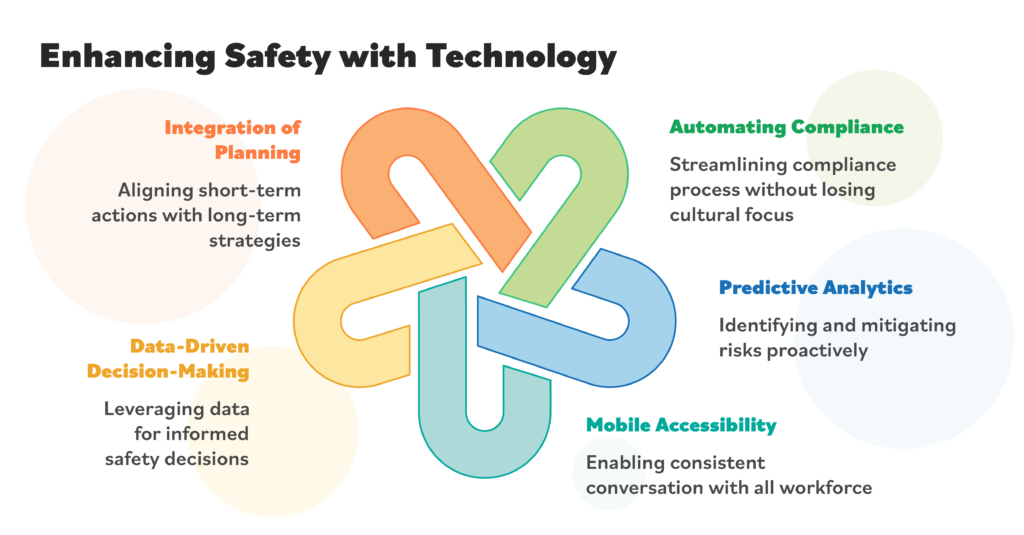
1. Automating compliance without losing culture
Compliance should not be a paperwork burden—it should enhance safety culture.
Intelex’s software helps organizations automate compliance tracking, regulatory reporting, and proactive activities like safety inspections, audits, and hazard identification to better engage the workforce.
Through customizable dashboards and automated workflows, companies can focus on engagement and safety leadership rather than administrative burdens.
2. Predictive analytics for risk mitigation
Instead of reacting to incidents, Intelex’s AI-driven analytics and predictive risk assessment tools help organizations identify and mitigate risks before they lead to injuries.
By integrating leading indicators such as near-miss reporting, unsafe conditions, and ergonomic assessments, organizations can shift from incident response to actual prevention strategies.
3. Mobile accessibility for field engagement
Field workers often feel disconnected from safety management systems because traditional reporting happens behind a desk.
Intelex’s mobile safety apps allow workers to report hazards, document incidents, and conduct safety inspections directly from their smartphones or tablets, ensuring real-time engagement and immediate corrective actions.
Bi-directional engagement via mobile devices allows for consistent conversation with all workforce members.
4. Data-driven decision-making
Many organizations collect vast amounts of safety data but fail to leverage it effectively.
Intelex enables organizations to centralize, analyze, and visualize data trends, helping leaders make informed decisions about where to invest resources, how to improve safety culture, and which risks to prioritize.
5. Integration of short-term and long-term safety planning
A significant challenge in safety management is balancing immediate hazard control with a long-term strategy.
Intelex allows organizations to track real-time incident data while aligning safety initiatives with business objectives.
With customizable safety performance tracking and automated reporting, leadership teams can monitor progress over time and refine long-term safety strategies based on real-world data.
The future of balanced safety: Data-driven, technology-enabled, and worker-centric
Companies that excel in safety—such as Alcoa, Heraeus, SUEZ, George’s Inc., Thales, and Moss—prioritize a balanced approach.
As workplace safety continues to evolve, integrating technology, cultural engagement, and predictive analytics will define the most successful organizations.
Solutions like Intelex help companies bridge the gap between:
- Compliance and culture
- Reactiveness and prevention
- Administration and frontline work
- Data collection and actionable insights
- Short-term fixes and long-term planning
By leveraging technology to enable balance, organizations can move toward a sustainable, high-performance safety culture where safety is not just a mandated requirement but a strategic advantage that protects people, enhances productivity, and drives business success.
The accurate measure of safety return on investment (ROI) is returning workers home safe and healthy every single day.
With the right leadership commitment, workforce engagement, and strategic application of technology, organizations can achieve a thriving workplace working towards zero harm.
Is your safety program unbalanced?
We developed a quick assessment tool to help you identify gaps between your current and ideal safety program and give you suggestions to bridge the gap.