The Crucial Role of Manufacturing Safety Training in Saving Lives and Increasing Efficiency
April 26, 2024
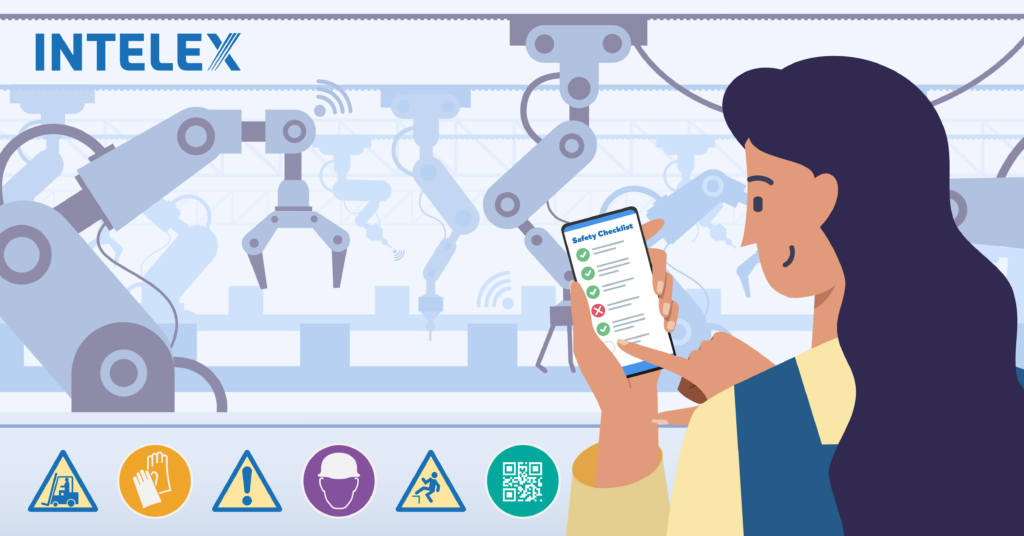
Workplace accidents, injuries and fatalities are costly events that are far too common in the manufacturing industry, where environments are fast-paced and full of potential hazards. Ensuring a safe work environment not only safeguards the well-being of employees but also enhances productivity, reduces absenteeism and preserves the reputation and financial stability of manufacturing companies. Additionally, adherence to safety regulations fosters a culture of responsibility and care, improving employee morale and retention within the organization.
One of the best ways to strengthen the safety culture at a manufacturing organization is through effective safety training. This article takes an in-depth look at the importance of manufacturing safety training in reducing accidents, injuries and fatalities while ensuring compliance with legal requirements and industry standards. It will also explore challenges that manufacturing companies face, the pros and cons of different delivery methods and how technology can help streamline workflows and drive continuous improvement.
The Importance of Manufacturing Safety Training
According to the Bureau of Labor Statistics, there were 396,800 total recordable cases of nonfatal injuries and illnesses in 2022, increasing 6.29% since 2020. Fatal work injuries totaled 404 for the manufacturing industry during 2022, compared to 341 during 2020. In addition to causing physical harm, workplace injuries and fatalities can lead to significant psychological trauma for workers and their families, exacerbating anxiety, depression and financial stress. The effects of such incidents can be devastating, disrupting family dynamics and placing immense strain on financial stability and emotional well-being. Therefore, prioritizing robust safety measures is essential not only for safeguarding individual workers but also for preserving the cohesion and security of their families.
In addition, when there are fewer injuries, there are fewer disruptions, fewer stops in production, smooth workflows and higher morale. This ripple effect streamlines efficiency and productivity, increasing your bottom line. According to the National Safety Council (NSC), over 60% of CFOs reported that each $1 invested in injury prevention returned $2 or more, and over 40% said productivity was the greatest benefit of an effective workplace safety program. Investing in a safety program at your company not only protects your workforce but also yields substantial financial returns and operational advantages in the long run.
A core component of a robust safety program is safety training, which serves as the foundation upon which a culture of safety is built. By sharing knowledge, instilling best practices and fostering a heightened awareness of potential hazards, safety training can help mitigate risks and incidents before they happen.

What Makes a Robust Manufacturing Safety Program
As manufacturing is a highly specialized industry, it’s important to tailor strategies to address its unique challenges and risks. From machine safety and hazard communication to ergonomics and personal protective equipment (PPE), these programs enable employees to navigate hazardous environments safely.
Safety training programs provide workers with the knowledge and skills needed to identify potential hazards, assess risks and take appropriate precautions to mitigate them. One example is instructing team members on how to interact with heavy equipment and use proper lifting techniques to reduce injuries. By educating employees on these types of safe work practices, emergency procedures and the proper use of safety equipment, your company can significantly reduce the likelihood of workplace accidents and injuries.
Adherence to legal compliance requirements and industry standards is also an integral part of an effective safety training program. Failure to address federal and state regulations, as well as company updates and changes, not only jeopardizes worker safety but could also expose your company to legal penalties and reputational damage.
Another factor that manufacturers should consider is that the effectiveness of initial safety training can diminish over time due to factors such as employee turnover, evolving job roles and changing safety regulations. Refresher training sessions are important as they serve as periodic reminders of safety protocols and best practices, reinforcing knowledge and behavior acquired during initial training.
Leveraging microlearning strategies, such as short, targeted Bulletins delivered on-demand via mobile devices, allows for continuous reinforcement of key safety concepts while accommodating the busy schedules and prevalent in the manufacturing industry. These quick hits also allow employers to take advantage of the short timeframes employees may have available between other duties to consume information.
By incorporating refresher training and microlearning into safety programs, organizations can ensure that their workforce remains vigilant and proficient in safety practices, ultimately reducing the risk of accidents and injuries on the factory floor.
Challenges in Manufacturing Safety Training
The introduction of new technologies and rapid mechanization has led to a large demand for a tech-savvy workforce in manufacturing. At the same time, the industry faces an acute shortage of employees with the necessary skills. This skill gap is significant and contributes to more safety incidents at work.
Research shows that companies that provide at least 20 hours of annual training are 68% more likely to have employees following safety protocols on the floor. This correlation underscores the direct link between investment in training and the cultivation of a safety-conscious workforce.
Despite its undeniable importance, manufacturing safety training is not without its challenges. They include, but are not limited to:
- Scheduling conflicts across multiple locations
- Language barriers
- Labor shortages and time constraints
- Consistency in trainings
- Downtime and loss of productivity
- Verification of its effectiveness
- Adequate refresher training
- Eliminating bad habits and shortcuts
- Lack of management enforcement
Overcoming these challenges requires a multifaceted approach that prioritizes adaptability, innovation and continuous improvement. By addressing these challenges head-on and investing in comprehensive safety training initiatives, manufacturing companies can cultivate a workforce equipped with the knowledge and skills necessary to navigate hazardous environments safely and sustainably.
Manufacturing Safety Training: Methods of Delivery
To confront these challenges, manufacturing companies can deploy a variety of training delivery methods to meet the diverse needs of their workforce. From traditional classroom training and hands-on demonstrations to online courses and workshops, each method offers unique advantages and limitations.
While classroom training provides opportunities for interactive learning, real-time feedback and hands-on experience with equipment, it can be resource-intensive and challenging to schedule, particularly across multiple locations and languages.
On the other hand, online training offers flexibility, scalability and cost-effectiveness, allowing employees to access training materials at their own pace and convenience. One downside is that if it’s not designed well, it can be less interactive and engaging. It can also be harder to gather feedback on effectiveness.
One solution is to implement Training Management software, which is designed to streamline the administration, delivery and tracking of safety training programs. It offers features such as automated course scheduling, competency assessments, progress tracking and reporting capabilities, enabling organizations to ensure compliance and monitor training effectiveness.
In addition, microlearning techniques, such as Bulletins, can be integrated into Training Management software to allow for the delivery of bite-sized training modules tailored to specific learning objectives, maximizing engagement and knowledge retention among employees.
Continuous Improvement and Evaluation
To ensure that your safety training programs are efficient, it’s important to consistently evaluate and improve them. Gathering feedback from participants and stakeholders, monitoring key performance indicators (KPIs), and leveraging metrics to measure the effectiveness of training initiatives facilitate this optimization.
Technology plays a pivotal role in enhancing the evaluation process and driving continuous improvement. For example, Training Management software can integrate with other systems within your organization, such as incident reporting and corrective action tracking, to provide a holistic view of safety performance and identify trends or patterns that may indicate areas for further training or process improvement. By leveraging data-driven insights, manufacturing companies can continuously refine their safety training programs, address emerging risks and foster a culture of continuous improvement throughout the organization.
How Intelex Can Help
Intelex has been named a valuable leader in offering resources and tools to support EHS programs. From bridging skill gaps and onboarding new hires to updating training content swiftly and ensuring compliance with regulatory mandates, Intelex provides comprehensive training management solutions tailored to the unique needs of manufacturing companies.
By leveraging technology and embracing innovative training methodologies, manufacturing companies can minimize downtime, reduce training costs and, most importantly, safeguard the well-being of their workforce. In doing so, you are not only fulfilling your legal obligations but also cultivating a culture of safety that permeates every facet of your operations, driving sustainable success in a rapidly changing industry.