Manufacturing Safety in the Post-Pandemic World
February 16, 2024
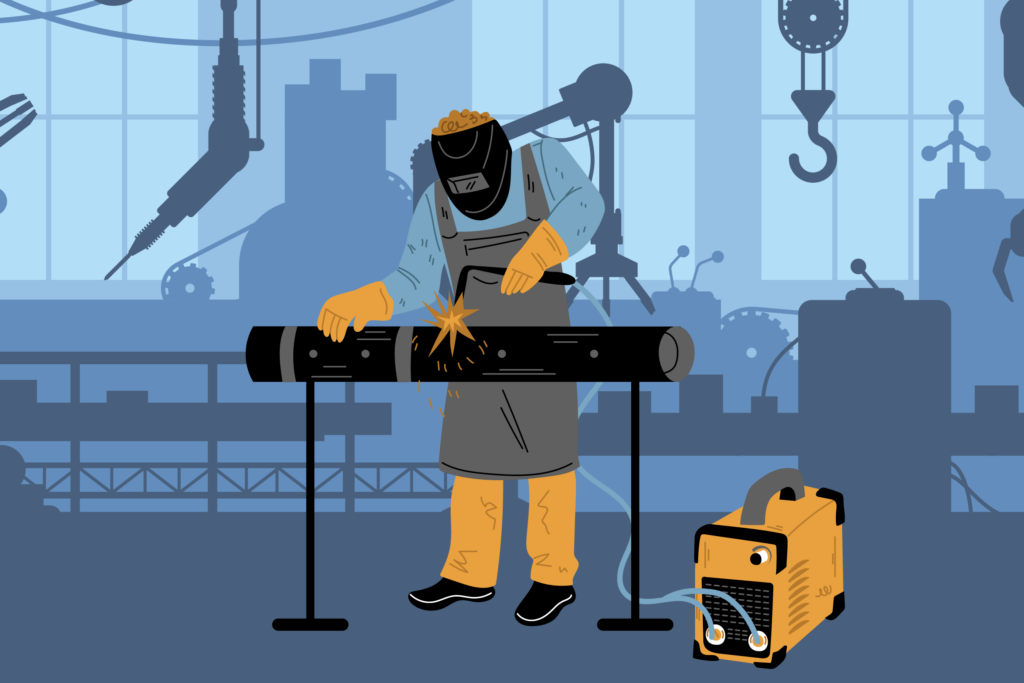
The COVID-19 pandemic profoundly impacted the manufacturing industry worldwide. With lockdowns changing the way we work and disrupting purchasing habits, many manufacturers shifted their attention to making personal protective equipment (PPE) for frontline workers. This pivot was a critical step in ensuring the resilience of the manufacturing industry. Despite the potential for the pandemic to devastate manufacturing, the U.S. economic recovery was much quicker than expected. According to the Center on Budget and Policy Priorities, while the pandemic might have provoked the deepest economic recession since World War II, it was also the shortest, with contracted economic activity restricted only to March and April 2020. Since then, the recovery has been much stronger than many analysts anticipated.
However, while the economic data is trending in the right direction, injuries and fatalities are not. According to the U.S. Bureau of Labor Statistics, there were 5,486 workplace fatalities in the United States in 2022 (the most recent year for which data is available). This reflects a 5.7 percent increase from 2021, when there were 5,190 injuries.
This article looks at how the labor shortage is one of the biggest challenges in post-pandemic manufacturing safety, as well as the ways in which digital transformation can help.
The Labor Shortage is a Big Challenge for Manufacturing Safety
By far, the biggest challenge for manufacturing safety today is the ongoing shortage of skilled labor. According to the Manufacturing Institute, the manufacturing industry needs to fill 4 million jobs by 2030. The COVID pandemic eliminated approximately 1.4 million manufacturing jobs, but that only added to an existing labor crisis. As it stands, there is a potential gap of 2.1 million unfilled manufacturing jobs by 2030, which could cost the U.S. economy $1 trillion.
The reasons behind this shortage are complex, with no single reason acting as a root cause. According to the U.S. Chamber of Commerce, early retirements and an aging workforce are critical contributors to the shortage. By October 2021, more than 3 million adults had taken early retirement due to the pandemic. This factor alone constitutes almost half the total number of workers missing from the U.S. workforce. This trend is likely to continue as the U.S. age demographic shifts higher and younger generations have fewer children.
The demographic of women in the workforce has also changed during the pandemic. Chronic daycare shortages, exacerbated by pandemic shutdowns, meant many women left the workforce to focus on home childcare. Women are now participating in the U.S. workforce at their lowest rate since the 1970s, with 3.5 million working mothers leaving the workforce in spring 2020. This drove the participation rate for women in the workforce from 70 percent to 55 percent. Since 2020, that participation rate has recovered somewhat, but remains well below the pre-pandemic rate. The research from the Chamber of Commerce suggests 27 percent of workers who lost their job during the pandemic cannot return to the workforce because they must care for children or other family members.
Meanwhile, entrepreneurial and digital commerce success has been a surprising contributor to the labor shortage. In 2022, entrepreneurs formed more than 5 million new businesses, with another 5.5 million in 2023. In 2020, more than 2 million people made more than $100,000 on social media. This has obvious economic benefits, but it has also taken millions of potential workers out of the manufacturing workforce, and the industry is struggling to attract workers who see more lucrative career options in the digital world.
Other factors continue to apply stress to the manufacturing industry. In 2021 and 2022, the U.S. Federal Government introduced several pieces of legislation designed to build resiliency into the U.S. economy, including the Infrastructure Investment and Jobs Act (IIJA), the Creating Helpful Incentives to Produce Semiconductors and Science Act (CHIPS) and the Inflation Reduction Act (IRA). This combination of funding and tax incentives will support manufacturing efforts for things like semiconductors, batteries and electric vehicles. However, workforce shortages and continued supply chain challenges for raw materials, exacerbated by conflict in Ukraine and the Middle East, represent considerable risk for these initiatives.
What does this mean for manufacturing safety? Potentially, it increases the risk of injuries and fatalities. When the workforce is smaller, workers are under pressure to do more. They bypass safety procedures and take shortcuts to get things done, which makes them more likely to make careless mistakes. As older workers retire, younger workers need to learn skills quickly so they can maintain production quotas, which means they might miss critical safety training. Retirement also means the organization loses institutional safety knowledge and peer relationships, which can have a critical impact on the safety culture. In other words, younger workers are under more pressure to perform, but have less knowledge and fewer skills to stay safe in a fast-paced manufacturing environment.
Future Trends for Manufacturing Safety: Technology-Focused Solutions
Digital transformation and disruption through the use of advanced technology such as sensors, cloud computing, machine learning, robotics, smart manufacturing, digital twinning, 3D printing and green manufacturing is key to manufacturing’s continuing ability to drive innovation and, ultimately, improve workplace safety. These technologies create increased connectedness between humans and machines and drive EHSQ 4.0 and Industry 4.0.
Sensors
From personnel sensors that can track employee location, vital signs, temperature and movement, to perimeter sensors that detect hazardous releases, to proximity sensors that warn when people and equipment are dangerously close to each other, sensor technology collects vast amounts of data that require analysis and action. The new world of data and analytics is having a profound impact on the way we work, and sensors are a frontline tool to collect that data.
Mobile Solutions
Creating a strong safety culture in a manufacturing environment needs more than spreadsheets and paper-based forms. Workers on the manufacturing frontline need a mobile app to record observations quickly and easily. These observations go to the management system to help leaders understand potential threats, which they can then use to send real-time updates to workers using bulletins to mobile devices. This creates a cycle of continuous safety feedback that enhances workplace situational awareness and makes frontline workers partners in manufacturing safety culture.
Machine Learning or AI-Enhanced Solutions
Machine learning (ML) and artificial intelligence (AI) are changing the way we think about safety data in the workplace. Instead of adding up numbers or struggling with spreadsheet formulas, data-based solutions for AI and ML can analyze massive amounts of data in real time to create leading indicators, which helps identify growing hazards before they turn into incidents. Protex AI uses closed-circuit television (CCTV) and AI to continuously monitor the work environment, identify hazards and provide that data to the management system for analysis and communication to the front line.
Robotics
Robotic automation can be found in various areas in manufacturing. Tasks that robots can perform include assembly, welding and shipping as well as product packing. Robots often are used to perform tasks that are physically impossible or potentially dangerous for human employees. Many organizations have introduced “cobots” (collaborative robots) in factories following the pandemic, which has helped them adhere to social distancing requirements.
Smart Manufacturing
We often hear about the factory of the future, but many of these solutions are available today. More importantly, they point to where manufacturing is heading as we go into the future. Intelligent (or smart) manufacturing is a closed-loop manufacturing process that is enabled by a digital thread. The whole focus is to ensure consistent, seamless alignment of the production system, achieving higher quality at lower cost. Organizations can accelerate product ramp-ups, exceed quality targets and deliver products faster. There is a direct correlation between cost of poor quality (COPQ)—resulting from inefficient production methods and rework that puts workers under stress—and worker safety. By improving the efficiency of the production system and reducing COPQ, human workers are under less pressure and have less rework, which reduces fatigue and keeps them safer.
Digital Twins and Virtual Reality
Virtual environments and digital twins are becoming important tools for training workers in complex tasks. Human error resulting from poor training continues to be a critical factor in many workplace accidents, and the pressure of a labor shortage means many organizations reduce onboarding time for new workers by neglecting training. Virtual environments can provide effective training at regular intervals to help ensure workers have the knowledge they need to perform their tasks and stay safe.
Conclusion
As a worsening labor shortage and a volatile global environment put the manufacturing industry under increasing pressure, new threats will continue to put worker safety at risk. To meet these evolving challenges, the manufacturing industry needs to look at digital transformation tools like AI, mobile solutions, virtual environments and sensors to adapt to new realities and keep workers safe on the job.