Top EHS Leadership Tips to Inspire a Strong Safety Culture
December 2, 2022
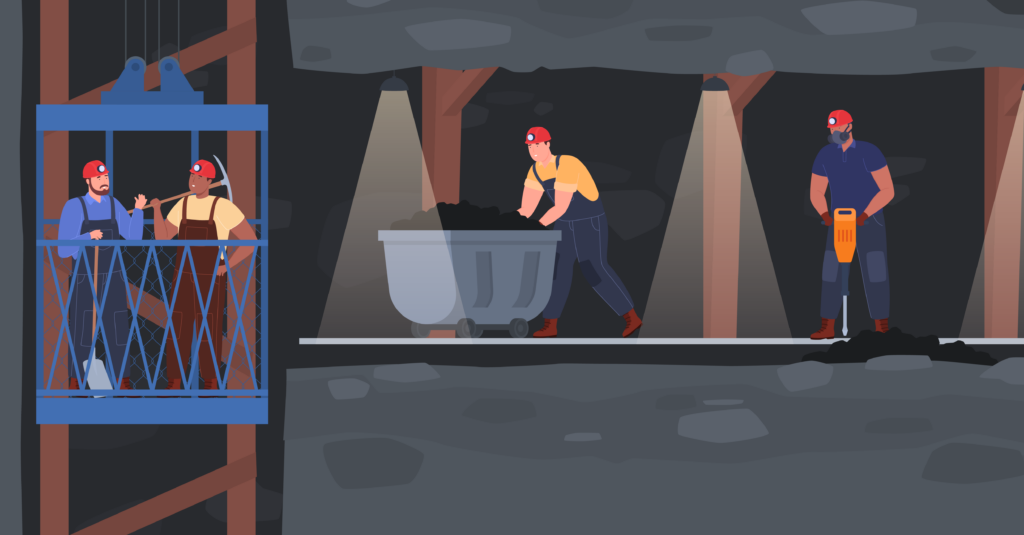
Seasoned safety pros and newly-appointed novices can benefit from these great tips for becoming a better EHS leader.
William Gibson, a safety specialist for Ohio-based Del-Co Water Company Inc., admits he’s far from being the most seasoned environment, health and safety (EHS) professional. But he is passionate about people and a keen observer who has taken the best ideas from safety veterans he’s encountered and applied those learnings to his own professional journey.
Gibson says he stepped out of his comfort zone to become a safety manager in 2017 when his company called out for someone to manage safety for the growing organization. During a recent presentation at the EHS Today Safety Leadership Conference, he shared many of the great lessons learned during his relatively short five-year career as an EHS professional and outlined what he believes are the building blocks of a great safety program and the key elements of a sound safety culture. What follows below is a summary of his insights.
- It starts with a proactive vision where you’ve assessed your workplaces risks, tried to anticipate the greatest hazards and what could go wrong and established what need to be closely tracked measurable goals to help you avoid incidents.
“This is simple stuff to do when you’re starting a program,” he says. “On a yearly basis, we set our safety goals. You want to set goals that are attainable and measurable. If you can’t do everything in a year – that’s fine. You at least want to have set goals and work through them.” - Plan for worst-case scenarios because, as Gibson says, you can never be too safe. And use safety technology to help manage the most hazardous risks within your working environment.
“Make sure that you budget for the most opportune potential incidents,” Gibson says. “Go back to your [OSHA]300 records…to anything where you can see what’s actually happening in your company and establish a [technology investment] budget. Those will be the things that usually happen more often so, why not spend the money on technology that costs a fraction of what it would cost if someone was injured?” - Safety professionals need to be present, accessible and approachable. “It’s a huge deal for people to see you in the workplace, asking them questions. You don’t always need to be the safety enforcer,” Gibson says. Commit to a people-first approach that lets employees know you care about them. It may spark a willingness to report safety incidents and issues or even suggest better training ideas.
“You want people to come to you so, the more you can get through to them…where they want to talk to you…it’s the best thing you can ask for,” Gibson says.
- Make it personal. To illustrate how a safety professional might take a more personal approach to individual people, Gibson offered an idea he discovered five years ago:
A safety colleague at a conference he attended explained how she put the names of each employee at her company into a glass jar. Once or twice a week, she would dip into that jar and pull out a random name then make a special effort to focus on that individual for that day.
“It’s a pretty cool idea,” Gibson says, explaining he now uses the same practice at his company. “Focusing on one person or two makes them feel good, it makes them feel empowered and lets them know you truly do care.” - Safety professionals need to walk the talk and “get their hands dirty” by participating in the jobs that workers do. It’s likely you’ll perform the job incorrectly, but it will show everyone how difficult certain jobs can be and help to humanize how others perceive you, Gibson says, adding, “They’ll respect you for it.”
- Encourage staff to teach you how to do their jobs because learning jobs from the folks who do the work helps you to understand the “why” behind what they do. Safety professionals should routinely walk the warehouse, office and factory floors. “Observations are priceless,” Gibson says. Take pictures and observe people – not just doing unsafe things but also performing their everyday jobs. Take candid photos of people engaged in their work and perhaps share these in future safety correspondences you send to employees. “Hang out” with employees. Interactions with them don’t always need to be safety related. Consider doing things with them outside of work, such as participating in local volunteer programs, Gibson suggests.
- Be honest, fair and consistent when communicating with employees. Speak the same way to your general manager as you would a trainee. “If you are not treating everyone the same when it comes to [safety] discipline or rules, no one’s going to buy into what you do,” Gibson says.
- Communicate often. Gibson says he regularly shares safety news and information, talking about each department and the safety work done for every area of the business. Gibson also produces an annual safety report and shares it with every employee. In the report he discusses current safety activities, accomplishments in the previous year and details of recorded incidents.
- In safety education, it’s important to offer job-relevant training and to make a list of the types of future trainings you want to provide to workers. Sometimes just seeing it on paper helps you plan a little bit better, Gibson says. Also recognize that one way to train doesn’t necessarily work for everyone.
“A lot of people don’t learn the same way – depending on their age or where they come from,” Gibson says. Online training may work for some, but hands-on instruction may work better for others. And, Gibson counsels, be patient.
“You want to talk to people like human beings and if they don’t understand, take the time to explain,” he says. - Look for opportunities to be a people motivator. Continually recognize individuals and teams and let them know the ways in which they are special. The easiest and littlest things often make the biggest difference, Gibson says. Showcase people by profiling them in the jobs they do.
“Try to pump up your employees to others…the people that don’t do these jobs will be encouraged to respect both the company and those individuals a little more,” Gibson says, adding, “The folks being talked about will feel appreciated.” - Learning never stops for safety professionals. It’s important to continually focus on personal development and education to improve your skills and abilities to help others, he says. Keep up to date with EHS trends, regulations and changes. You don’t want to be in a position where you’re moving reactively – adapting safety practices and processes after hazards leads to incidents.
“We’ve been a company for 50 years…and we just put in a lockout/tagout program three years ago,” Gibson says, explaining how his company had tended to be reactive to hazards. “It took an injury for [these things] to happen, but we’ve learned from it and we’re trying to be proactive for future incidents.” - Use safety industry resources to help you improve. Many EHS associations offer grants or subsidies for certain types of safety assets and equipment, and it’s worth checking them out, he says. Reach out to fire departments and local highway patrols for help in identifying hazards and risks related to the work a company does. Gibson suggests exploring OSHA’s On-Site Consultation Program, which offers no-cost and confidential occupational safety and health services to small- and medium-sized businesses in all 50 states, the District of Columbia, and several U.S. territories, with priority given to high-hazard worksites.
- Try to make safety fun – or at least make the attempt. Gibson recommends the following:
- Use animation and fun illustrations or videos in safety presentations
- Gamification, including:
- What’s Wrong with This Picture? where people identify hazards in a photograph.
- Pin the personal protective equipment (PPE) on the worker – a variation of the old children’s game of pin the tail on the donkey – in this case perhaps using a life-sized outline of a person where you might ask folks while blindfolded to attach PPE cutouts.
- Safety quizzes on a variety of safety topics – these can be found online.
- Memes and GIFs. Gibson calls these “just the best thing in the world” and says, “If you can use them in training and make people laugh, you’re a step ahead.”
- Safety Jeopardy – a fun way to review the last year of safety training you did. Many templates are available online to create a Jeopardy game, Gibson says.
Last but not least, Gibson suggests recognizing and communicating the great safety things you do so that employees clearly see how your program and culture continue to improve. Regularly review your safety policies, the EHS goals you set and track the progress you make. Consider what might drive even greater improvement.
Discover practical steps to strengthen your safety culture with insights from Scott Gaddis. Watch our on-demand webinar for actionable ideas to enhance safety accountability and success.