How Moss Construction Cut Workplace Injuries by 25% with Intelex EHS Software
March 9, 2022
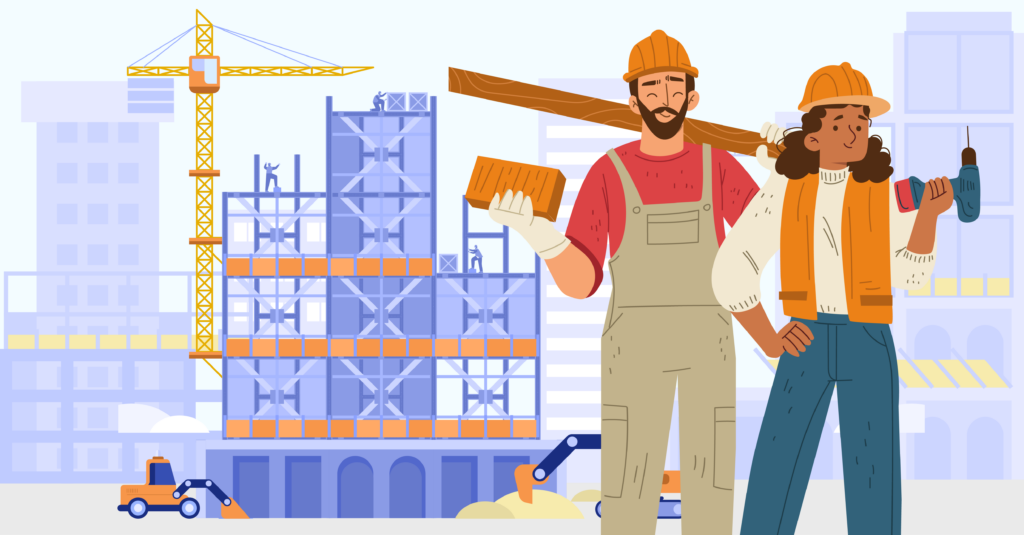
Fast growing companies often find themselves needing a high-performance approach to environmental health and safety (EHS).
Take the case of Fort Lauderdale, Florida-based construction company Moss & Associates, whose vice president of environmental health and safety, Scott Gerard, recently told the story of his company’s business growth. During a presentation at the 2021 EHS Today Safety Leadership Conference, Gerard said Moss started out as a company of 300 people some 17 years ago and has today become an organization of more than 3,000 employees with expectations to reach 6,000 this year.
But high growth often moves too quickly past other corporate capabilities. In this case, Moss had outgrown its traditional EHS data collection approach that utilized Microsoft Word and Excel flat files that required safety professionals to make assumptions about safety performance without the benefit of validation from data and analytics.
“To facilitate that growth, we had to rethink our strategy on collecting data and what we do with it,” Gerard said. “Turns out we were pretty good at collecting data, but not really good at acting on it or making it available to the operations teams.”
Before the company embraced data collection through a safety management system platform, Gerard believed he had a great handle on when accidents were most often happening.
“I would have told you about seven or eight years ago that most of our accidents happened on Tuesday in the morning because that’s when we bring all our leadership in on construction projects to have what’s called a subcontractor meeting…and I thought that’s when the field runs amok,” he said.
During that during that time, workers would not have had proper supervision and might have been inclined to take shortcuts they otherwise wouldn’t take had they been directly supervised, he said, adding, “I really would have bet the farm that this was when (most) incidents were happening.”
Turns out that the assumptions they made without validating data and analytics were simply not correct. Gerard now says that incidents are “pretty evenly distributed” throughout the week.
Searching for a New Health and Safety Management Platform
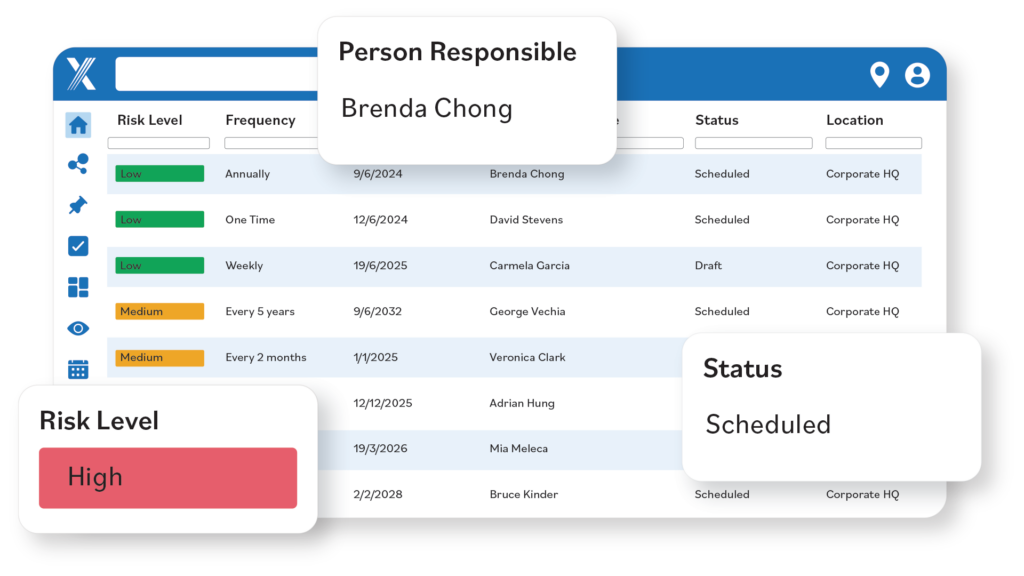
Moss ultimately went searching for a safety management system and settled on the Intelex Health and Safety Management platform to bring all its data from various processes into a centralized database, including incident reporting, inspections, behavioral-based observations, recorded near misses, good catches and even safety suggestions. Gerard described it as a hub-and-spoke system with 15 sources of data flowing in and out of the “single source of truth” Intelex platform.
Moss’s centralized safety management system integrates data from other systems that include employee resource planning, scheduling, weather alerts, an IoT system that records working hours and includes an alert system that monitors entry into unauthorized or dangerous areas, a reverse 911 system for broadcasting alerts and an insurance claims system.
“That hub-and-spoke system is key when you’re making decisions about transforming into a digital environment or looking at your evolution for your next platform,” Gerard said. “Making sure that it will talk to other systems, in my mind, is a must-have. It’s one of the Top 5 must-haves.”
Improvements were also needed for data gathering and, to that end, Moss introduced schedule-driven inspections – a condensed form with pieces and chapters for various phases of construction that listed the hazards typically related to them. It replaced an earlier approach where safety inspectors were given a “soup to nuts” checklist that would often come back only half filled out, with many fields simply “not applicable” to certain situations and activities.
“The inspections are now focused, they’re relevant and they give us back the most important commodity that as EHS professionals we have – time,” Gerard said. “It allowed us to really focus in on hazards that created opportunities for people to get hurt and to ultimately eliminate those hazards.”
System Upgrades Go Beyond Workplace Safety
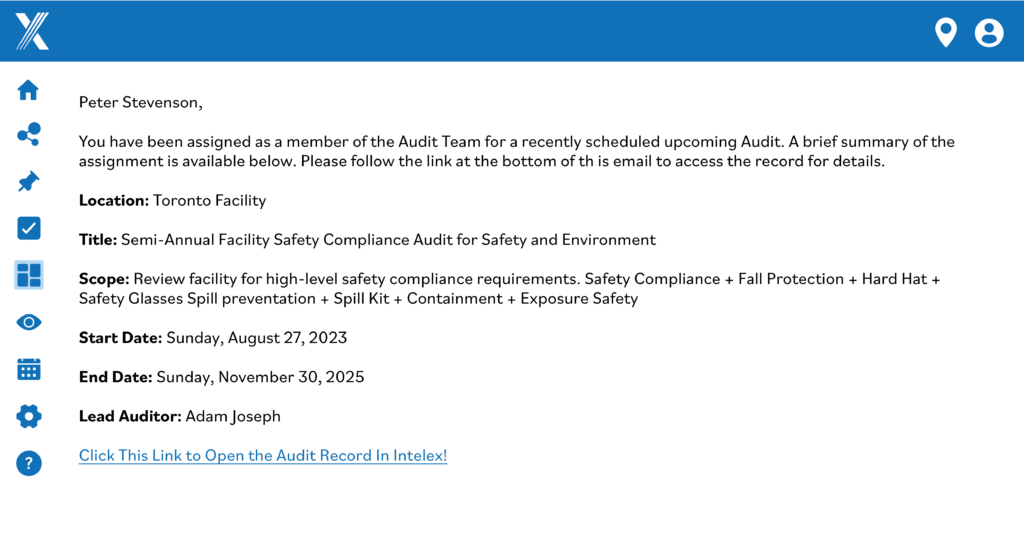
Moss has also introduced a reverse-911 alert system for its employees. Now when an incident or hazard happens on a job site, notifications are automatically sent out through the alert system so that workers are immediately aware of any emergency or ongoing hazardous situation, and they are given instructions on how to prepare, respond and act.
“We are a Florida-based company and about half of our work is in Florida. So, we get to experience hurricanes for about half of the year,” Gerard said. “We use this system to give out data to our supervisors and hourly work force on what to expect.”
He cited a unique situation that once happened in Hawaii where 100 company workers had been deployed on a project. A rare hurricane was about to hit the area and employees there were alerted and instructed to take immediate shelter.
“We had four people that responded back in those last hours (before the storm) saying, ‘I think I made a mistake, and I don’t feel like I protected my family properly. Can you help me?’
“We were able to get that message back to leadership on the island and they were able to place these families in “hardened structured” hotels,” Gerard said. “Using technology is not always just for work-related events. It’s taking care of our families or teams.”
Applications Should ‘Talk’ To Each Other
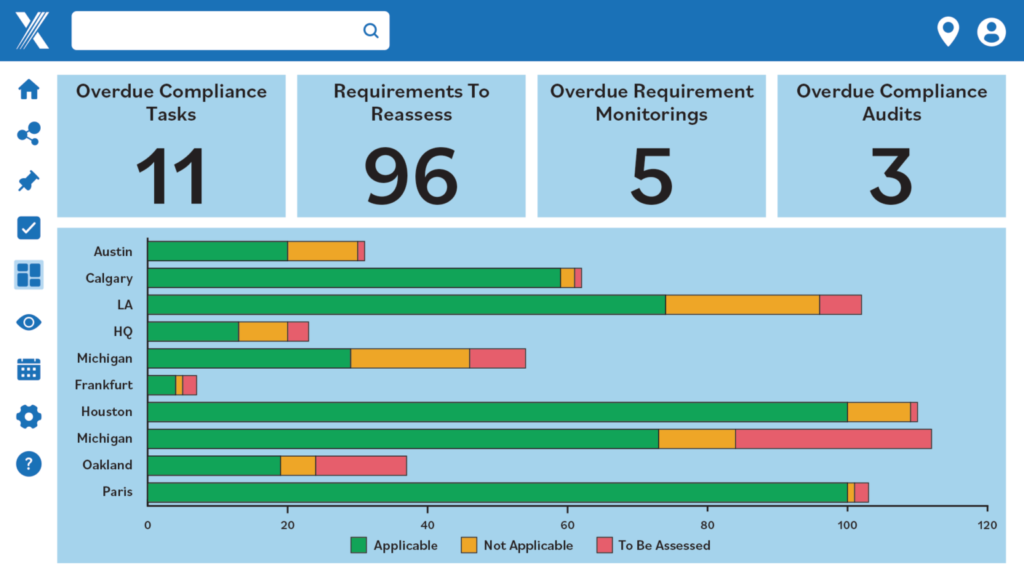
In advising others who might be considering a move to technology-powered EHS, Gerard said he believes it’s important to have a system where applications “talk” to each other and use relevant and meaningful data.
“You can collect thousands and thousands of data points, but you have to be careful with that as you move to a digital platform,” he said. “Make sure that you’re not collecting data points that you won’t be able to leverage…that are not going to be actionable.”
There’s a danger in too much data – collecting what isn’t actionable, he added.
“Even when we were analog, collecting data on flat files, we didn’t have the ability to make it actionable,” Gerard said. “When we started this (digital) process we over-collected data, but it wasn’t actionable. Over-collection of data is a burden on the people you’re asking to collect that for you. Make sure that it makes sense.”
Tips for Adopting New Safety Technology
Changes in technology also require strategy and cultural change. Gerard advised the following:
- Become familiar with emerging technologies for safety as well as other purposes that support safety.
- New products enter the market at a rapid pace. Safety professionals will find they either need more time to learn about them and/or the support and help of IT professionals and dedicated safety technicians.
- Begin now to budget for technology and think from one to 10 years ahead in order to budget appropriately.
- A process roadmap will enable the expansion or redevelopment of an overall safety strategy. Develop one if you don’t already have one.
Conclusion
Moss & Associates’ adoption of EHS software showcases how data-driven safety management can deliver real results. By centralizing safety data and focusing on actionable insights, Moss reduced injury frequency by 25% between 2017 and 2021. This transformation not only improved workplace safety but also enhanced efficiency, freeing up valuable time for EHS professionals to focus on proactive hazard prevention.
Ready to transform your safety processes? Discover how our Construction Safety Software can help you reduce incidents and streamline operations.