How to Build Your Job Safety Analysis Plan
December 21, 2021
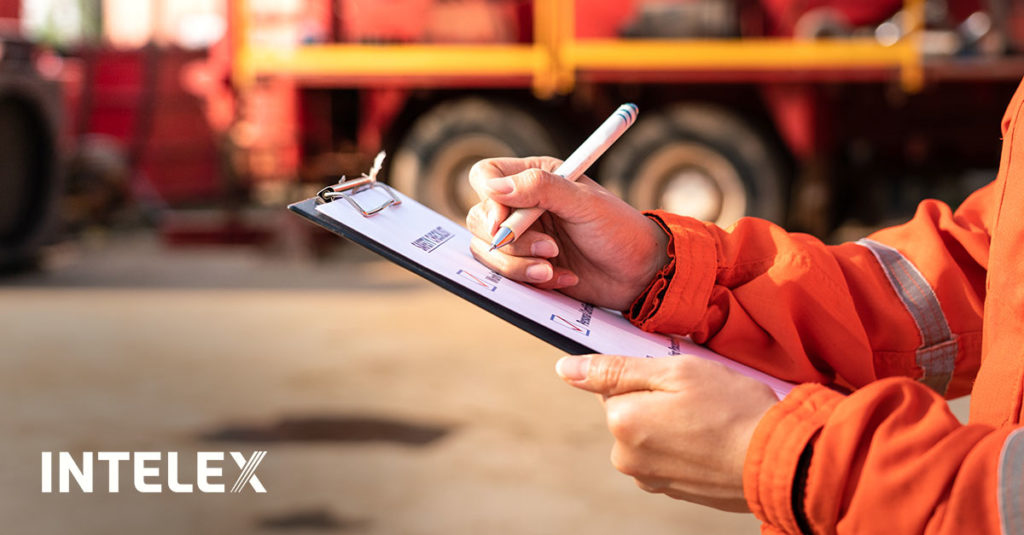
Too many workers are injured and killed each day at the workplace and employers need to do all they can to be aware of and reduce the risks to prevent workplace injuries. The International Labor Organization (ILO) estimates 2.3 million people around the world die from work-related accidents or diseases every year – a total that exceeds 6000 deaths each day. In addition, there are 340 million occupational accidents and 160 million victims of work-related illnesses annually.
Job hazard analysis (JHA) or job safety analysis (JSA) help to identify risks and create safer workplaces. JSA and JHA are generally interchangeable terms used to describe plans that define and outline how to control hazards associated with certain processes, jobs or procedures. It is a systematic examination and documentation of every task within a particular job to identify existing health and safety hazards, and the steps required to control risk.
JSAs are also an important training tool for new employees, showing them the steps required to perform their jobs safely. But as is the case for every employee health and safety practice, a JSA requires commitment from works and especially leadership to be effective.
JSAs incorporate health and safety principles and practices into a task or job. Deloitte, in its report Workplace Safety Analytics, defines the terms “job” and “task” to mean a specific work assignment, such as “operating a grinder, using a pressurized water extinguisher or changing a flat tire.” It’s important not to define a job too broadly or narrowly. In a JSA, each basic step of a job is determined, potential hazards are identified in each step, and recommendations are made for the safest way to perform it.
Recognizing hazards is a matter of watching a worker do a job. That might involve a group of experienced workers and supervisors who observe that job being performed then offering insights and analysis through later discussions. These assessments might include other participants with a wider base of experience. Analysis would seek to identify undetected hazards and increase the job knowledge of those participating. The goal is to heighten safety and health awareness, improve communication between workers and promote greater acceptance of safe work procedures.
JSAs create regular contact between supervisors and workers. They also provide initial job training education and help create briefing guides for infrequent jobs. JSAs might also become the standard for health and safety inspections or observations and support comprehensive accident investigations.
How to Perform a JSA
The Canadian Centre for Occupational Health and Safety (CCOHS) outlines four basic steps for conducting a JSA:
1. Select the job to be analyzed:
Ideally, a JSA should be conducted for all jobs and revised whenever equipment, raw materials, processes or the environment changes. It’s suggested to take a first-things-first approach and start by creating JSAs for the most critical jobs determined through a prioritization analysis, which CCOHS says should consider:
- Accident frequency and severity: Jobs where accidents occur frequently or where they occur infrequently but result in serious injuries.
- Potential for severe injuries or illnesses: Jobs where the consequences of an accident, hazardous condition or exposure to harmful products are potentially severe.
- Newly established jobs: Due to lack of experience in these jobs, hazards may not be evident or anticipated.
- Modified jobs: There may be new hazards associated with changes in job procedures.
- Infrequently performed jobs: Workers may be at greater risk when undertaking non-routine jobs, and a JSA provides a means of reviewing and identifying hazards in those tasks.
2. Break the job down into a sequence of steps:
A step is defined as “a segment of the job operation necessary to advance the work.” It’s important not to define the steps too broadly as missing important ones may result in associated hazards not being identified. On the flipside, too much detail creates too many steps.
CCOHS’s rule of thumb suggests most jobs can be described in 10 steps or less. If more are required, then it is suggested to divide the job operation into two segments, each with a separate JSA.
- Combine steps where appropriate to streamline the process.
- Ensure each step is in the correct sequence to avoid missing hazards.
- Focus on defining what is done rather than how it is done.
- Fill out job steps in a template through observation.
- Observers should be experienced and capable in all aspects of the task.
- Conduct observations during normal times and situations.
- Discuss the breakdown and correct order of steps upon completion.
3. Identify potential hazards:
The next stage is to identify potential hazards at each step. Based on observations, knowledge of accident and injury causes and personal experience, it’s a matter of listing things that could go wrong. Rather than seeking to solve detected hazards and problems, the effort here should simply identify them. CCOHS suggests assessment through a series of targeted questions that might include:
- Can a body part get caught in or between objects?
- Do tools, machines or equipment present any hazards?
- Can a worker make harmful contact with moving objects?
- Can a worker slip, trip or fall?
- Can a worker suffer strain from lifting, pushing or pulling?
- Is a worker exposed to extreme heat or cold?
- Is excessive noise or vibration a problem?
- Is there a danger from falling objects?
- Is lighting a problem?
- Can weather conditions affect safety?
- Is there possible exposure to harmful radiation?
- Can contact be made with hot, toxic or caustic products?
- Are there dusts, fumes, mists or vapors in the air?
4. Determine preventive measures:
Eliminating or controlling identified hazards is the focus here. Generally accepted methods are listed below in order of preference:
A. Eliminating the hazard – The most effective measure and techniques to do it might include:
- Choosing a different process
- Modifying an existing process
- Substituting with a less hazardous product
- Improving the environment (such as adding ventilation)
- Modifying or changing the equipment or tools
B. Containing the hazard – Assumes the hazard can’t be eliminated. Contact could be prevented by using enclosures, machine guards, worker booths or similar devices.
C. Revising work procedures – Modify steps for managing the hazardous situation, changing the sequence or adding additional steps.
D. Reducing the exposure – This option is considered the least effective and should only be used if other solutions are not possible. One way to minimize exposure is to reduce the number of times a hazard is encountered. An example of reducing hazard exposure would be to modify machinery so that less maintenance is needed. The use of appropriate personal protective equipment may be required. To reduce the severity of an incident, emergency facilities such as eyewash stations may need to be provided.
In listing and explaining preventive measures, CCOHS recommends avoiding general statements such as “be careful” or “use caution” and instead be specific and describe both what actions should be taken and how a job step should be performed.
An additional and essential follow-through step in JSA is ongoing monitoring and control or management. The effort here is to understand and validate whether a JSA works as desired. Monitoring helps ensure job safety and hazard concerns were abated or mitigated to a desired level and that the JSA is correctly implemented. This happens through follow up job-task inspection and interviews with workers that are using a specific JSA.
Further investigation and corrective action may be required to identify and address additional root causes discovered through monitoring activity and provide further correction. Gaddis says that a safety professional should never believe a “first” implemented procedure is completed until they have done their due diligence with additional monitoring.
For a more complete discussion of JSAs and the importance of analytics in creating safer workplaces, download: The More You Know (Part 1): The Essentials of Job Safety Analysis.