Permit to Work Boosts Safety by Design Strategies
August 31, 2021
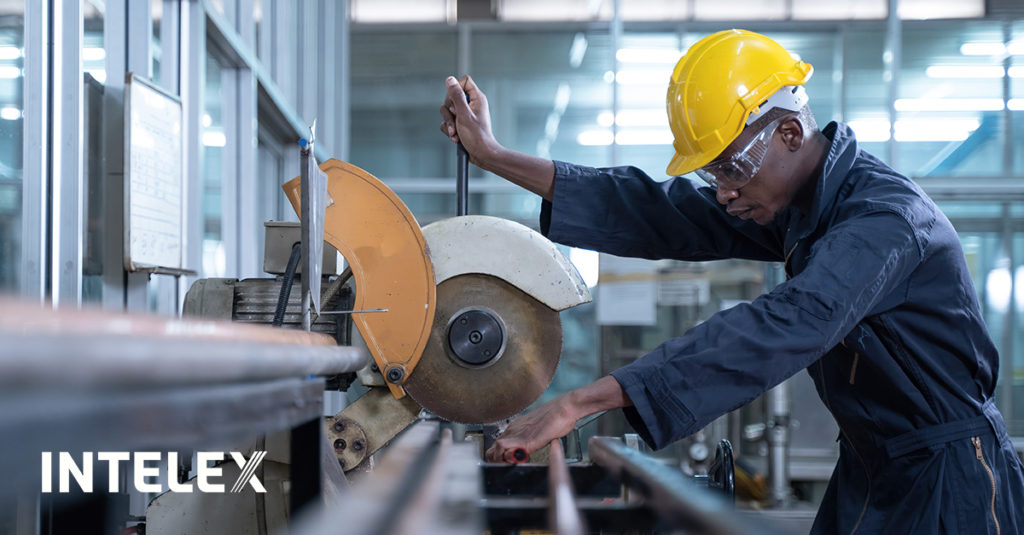
As companies pursue more proactive and preventive safety strategies such as Safety by Design, they are looking for new processes and methods such as Permit to Work software, to help make it happen.
Keeping workers healthy, happy and safe should be a strong governance focus within every company’s ESG strategy. In 2019, over 27% of the 5,333 worker fatalities in the U.S. were due to workplace hazards such as getting struck or caught in objects or equipment (14%), exposure to harmful substances or environments (12%) or injury from fire and explosion (2%). And for every hazard-related worker fatality, there were 20 to 60 times as many non-fatal incidents that created costly and disruptive downtime and absences from work. So, despite an increased emphasis on improving worker health and safety, there are still considerable challenges to making it happen.
Eliminating workplace hazards is the idea behind Safety by Design, a proactive and preventative approach to workplace safety. Its objective is to systematically identify, mitigate and eliminate as many workplace hazards as possible.
Compliance Is a Challenge
The weakest link in any corporate safety program is often its people. As an organization you spend time, effort and money to train, educate and equip workers with everything they need to do their work safely, but you cannot guarantee their compliance.
An NYU study showed that hard hats were only worn by 16% of workers who sustained head injuries, only 23% of the workers with foot injuries wore safety shoes/boots and only around 40% of the workers with eye injuries wore protective eyeware. Incident rates for contractors, who often perform non-routine work without training or knowing safety procedures, are two to three times higher than for full-time employees. So how do you provide workers a thorough understanding of the hazards and risks associated with a task and help them mitigate that risk and perform the work safely? A common solution is safe work permits, which are a key element of a permit to work (PTW) process.
Permit to Work Protects Employees and Employers
Permit to work is a formal process that identifies, communicates and mitigates risk for workers completing non-routine tasks in potentially hazardous work areas. Its purpose is to protect contractors and employees by ensuring they are aware of and understand the risk of all potential hazards, and that appropriate controls are implemented so that they can perform their job safely. Key details that PTW must include are:
- Identification of the permit authorizer and work supervisor.
- A detailed description of the scope of work to be performed and permit timeframe.
- Designation of the person or persons required to do the work.
- Description of all training, instruction and education workers need to be authorized to perform the work.
- Formal risk assessments, such as job safety analysis, to identify hazards associated with the work tasks.
- Identification of simultaneous operations which may result in conflicts
- Identification and application of controls, such as required PPE and exposure monitoring
- Lockdown of required energy isolations, such as lock out/tag out (LOTO)
- Agreement for the corporation and tradespeople to adhere to the PTW process in the form of document signatures
The effectiveness of PTW is only as good as the identification of hazards and risks up-front, the control procedures required to mitigate those risks and the compliance of workers following those control procedures. Obviously, a deficiency in any one area reduces the overall effectiveness of the PTW process.
Technology Simplifies and Improves Permit to Work
There are many ways that technology can improve workplace safety, and more specifically, the PTW process. Remote and wearable sensors capture important environment data such as sound levels, air pressure or temperature to identify work area risk more accurately and in real-time. For example, wearable gas detectors protect mobile workers through continuous atmospheric testing while always-on connected data streams are useful for alerts and analysis. Improvements in personal protective equipment (PPE) make it easier for workers in hostile environments to protect themselves, and digitized PTW workflows increase communication and information sharing between EHS and operations teams
Permit to Work software reduces administration effort and makes it easier for EHS managers to recognize workplace hazards and implement the controls required to minimize their risk. It centralizes and simplifies the management of requesting, reviewing, authorizing and reporting of work in hazardous environments across your entire organization. Equally as important, Permit to Work software will often integrate with other key EHS software tools such as Job Safety Analysis, Training Management, Document Control, Operational Risk Management and more to improve PTW information quality and deliver an integrated approach to Safety by Design.
Permit to Work Keeps Employees Healthy, Happy and Safe
Workplace safety makes good business sense. OSHA has found that for every $1 invested in a workplace health and safety program, a business can benefit by saving $4 to $6 by lowering costs, increasing productivity and improving employee engagement. These benefits increase when you focus on more proactive and preventive safety solutions such as Safety by Design. PTW makes Safety by Design easier by formalizing risk identification and communication, control adherence and energy isolations during tasks where employees and contractors are most at risk.
Learn how Intelex Permit to Work software can improve your organizations Safety by Design strategy.