What Is a Quality Management System and Why Do You Need One?
April 27, 2020
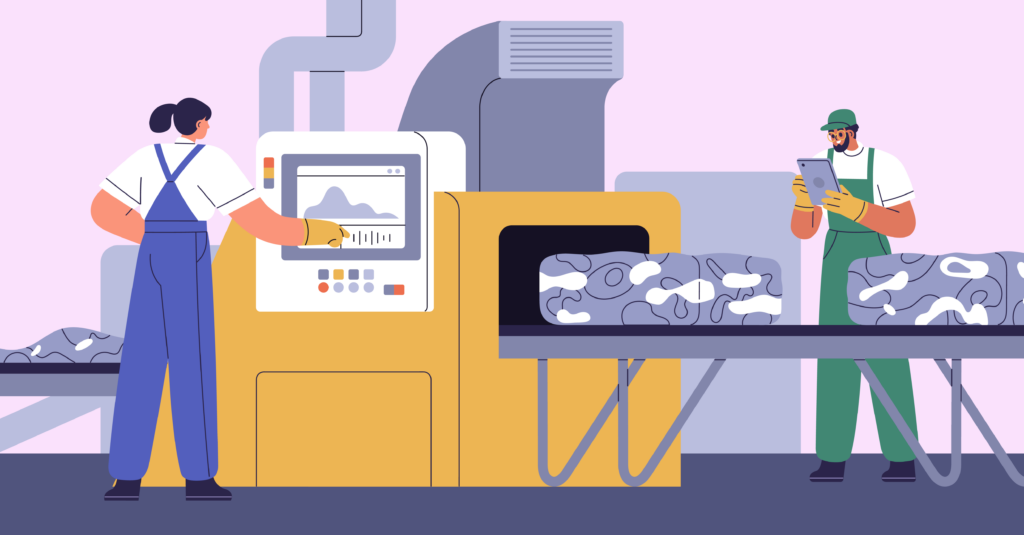
The cost of poor quality can be high for many organizations. Expensive waste, product rework or recalls, supply chains that lack accountability, and lack of insight into your customer requirements are symptoms of a quality management problem. If you’ve thought about implementing quality practices in your organization, you’ve probably heard the term “quality management system” or its acronym “QMS” and wondered what it means. Is it a software application? Is it a group of people? How can I learn about it?
This short guide will help you to understand the basics of a quality management system and where to find the best guidance to get started on the path to continual quality improvement in your organization.
What is a Quality Management System?
According to the International Organization for Standardization (ISO), a management system is “a set of interrelated or interacting elements of an organization to establish policies and objectives, and processes to achieve those objectives.” A quality management system will support ISO’s seven quality principles:
- Customer focus
- Leadership
- Engagement of People
- Process approach
- Improvement
- Evidence-based decision making
- Relationship management
A quality management system is the combination of people, processes, and tools that manages the quality resources across the organization to ensure customer satisfaction, reduce waste, and provide the groundwork for product and service innovation that meets customer expectations.
While quality management can trace its origins back to the Middle Ages, contemporary quality management dates to the early twentieth century, when W. Edwards Deming and Joseph M. Juran built on the work of statistician Walter Shewart to develop quality principles that extend beyond the manufacturing process to all organizational processes and instill the values of quality in every worker. These quality principles complemented work being done in Japan by Eiji Toyoda and Taiichi Ohno, who helped establish the influential Toyota Production System.
What Are the Benefits of a Quality Management System?
A quality management system allows an organization to link business objectives with customer expectations, provide data that supports evidence-based decision making by leadership, reduce waste and prevent rework, and ensure transparency at each stage of the supply chain. The introduction of a quality management system also helps to promote the values of quality throughout the organization to create a culture of quality in which everyone, not just a quality manager, is responsible for quality.
What Guidance Is There for Quality Management Systems?
Organizations can look to standards and frameworks for guidance on implementing a quality management system. ISO 9001:2015 is the international standard for quality management systems. It outlines a framework and vocabulary for improving quality in any organization. ISO 9001:2015 uses a high-level structure (known as Annex SL) to facilitate integration with other management system standards such as health and safety management and environmental management, the Plan-Do-Check-Act (PDCA) approach popularized by W. Edwards Deming to promote continual improvement, and risk-based thinking to help identify potential positive or negative events.
The Baldrige Performance Excellence Program (BPEP) is a framework that provides quality criteria and promotes a systems perspective of the quality management system that extends across the organization. The Baldrige core values and concepts, including customer-focused excellence, organizational learning, and visionary leadership, act as the foundation for the performance and operational elements that lead to quality excellence.
The European Foundation for Quality Management (EFQM) provides an excellence model that includes tools for diagnosing process deficiencies, a common vocabulary for communication within the organization, and a method for structuring the quality management system. The EFQM Excellence Model places external and internal customers at the center of its focus and advocates for their empowerment and recognition. It also uses a variation of PDCA that it calls RADAR (Required Results, Plan and Develop Approaches, Deploy Approaches, Asses and Refine Approaches and Deployment) to ensure continual improvement.
How Can Software Support a Quality Management System?
A quality management system is supported by many different tools for collecting and analyzing data produced by the organization. Many of these tools, such as Control Charts, Ishikawa Diagrams, and Pareto Charts, date back to the initial development of quality management and are still used today. Others, such as Failure Mode and Effects Analysis (FMEA) and Advanced Product Quality Planning (APQP) augment the traditional tools and are used in many different industries including automotive and electronics manufacturing.
A quality management system requires data collection, data analysis, and process documentation to ensure the organization can succeed with evidence-based decision making and satisfying customer requirements. The complexity of these requirements, as well as the compliance requirements for organizations that operate in multiple jurisdictions in a global environment, require cloud-based software applications to ensure continual improvement of the quality management system.
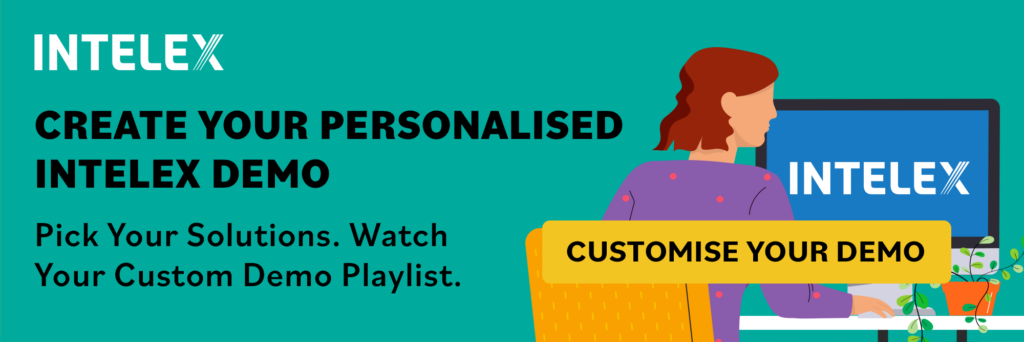