10 Tips for Effective FMEAs
January 17, 2019
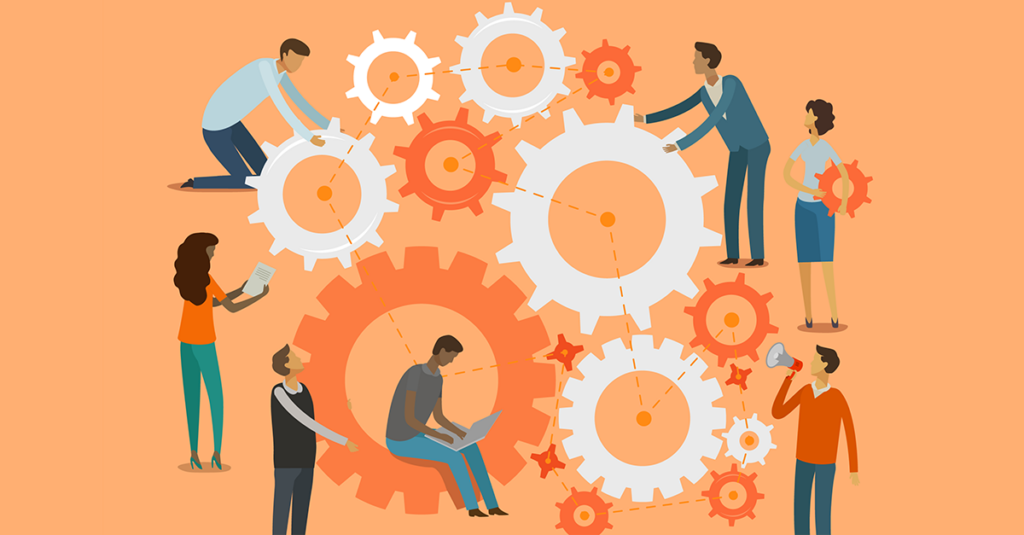
The Failure Mode and Effects Analysis (FMEA) can reduce or eliminate failure costs and protect against errors by illuminating issues before they arise. The technique can be used to design products or services, the production processes that deliver them, or to improve prototypes or existing processes.
What practices should you adopt to promote a robust FMEA process? Here are some to start with:
- Decide on a scope for the FMEA exercise before you begin. Will it pertain to one process, subprocess, part or product? Will it be unique to one site or facility, or can it be applied to many? Defining a scope can make the deliberation process easier.
- Start the FMEA process as early as possible. Don’t wait to explore risks and risk management approaches until designs are fixed, and the assets to support a production process and procured and installed. It’s easier to make error-preventing changes at the idea stage than it is after all critical decisions have been made.
- Build a cross-functional FMEA team. Include product or process owners, stakeholders and even customers if you can. Incorporate salespeople, trainers or marketing staff who will pay attention to different aspects of performance.
- Make the FMEA a living document. Re-assess risks after design changes, process improvements, or changes in the environment to respond in agile ways. Link control plans and action plans to FMEAs.
- Keep catalogs of common failure modes, causes and effects. Rather than coming up with all the ideas from scratch, draw from your organization’s knowledge base. Digitized systems can help with this task.
- When identifying the cause for a failure mode, get to the root. It’s easy to record the first cause the FMEA team thinks of, but it’s only by addressing the root cause that you reap the greatest benefits. Link 8D or other root cause analysis into your FMEA for effective recordkeeping.
- Consider costs and actual recorded events. Although most FMEA grids don’t have a spot to keeping track of the projected cost or actual occurrence of each failure mode, knowing this information can transform how you interpret overall risks.
- Include the interfaces to your supply chain (receiving). Changes in the inputs – or how the inputs arrive at your location – can have impacts on risks across the system. Include them in your FMEA worksheets.
- Supplement the FMEA with other risk assessment techniques appropriate to your industry, such as Process Hazard Analysis (PHA), Hazard and Operability Study (HAZOP), Systematic Human Error Reduction and Prediction Approach (SHERPA), what-if analysis or Fault Tree Analysis (FTA). FMEA is useful and effective, but should not be considered a panacea.
- Promote strong involvement by both business and technical staff. In many organizations, FMEA is a task conducted entirely by technical or engineering teams. Get your people on the business side involved in recording failure modes and effects or engaging in root cause analysis exercises to support the FMEA, to strengthen the results and make sure they are consistently applied across the organization.
Most significantly, the FMEA approach supports organizational learning. By capturing knowledge about products and processes in a form that is easily recognized by many, information is preserved and communicated. An FMEA process with broad involvement can thus advance organizational learning while protecting you from the impacts of potential issues or errors.
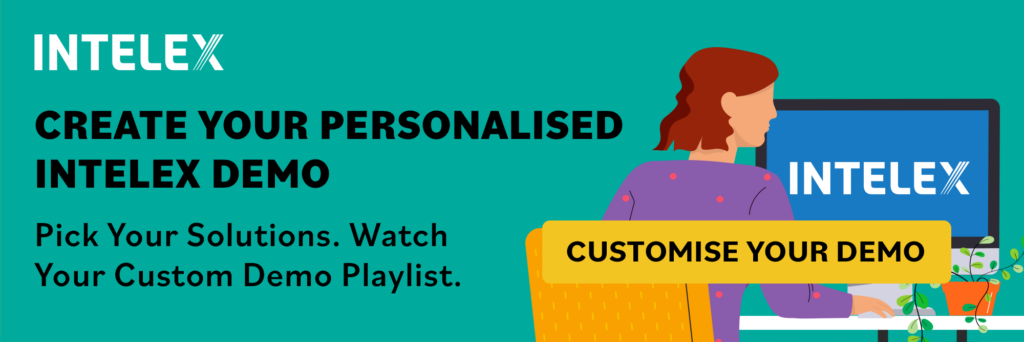