Building a Balanced Safety Strategy for Sustained Excellence
February 24, 2025
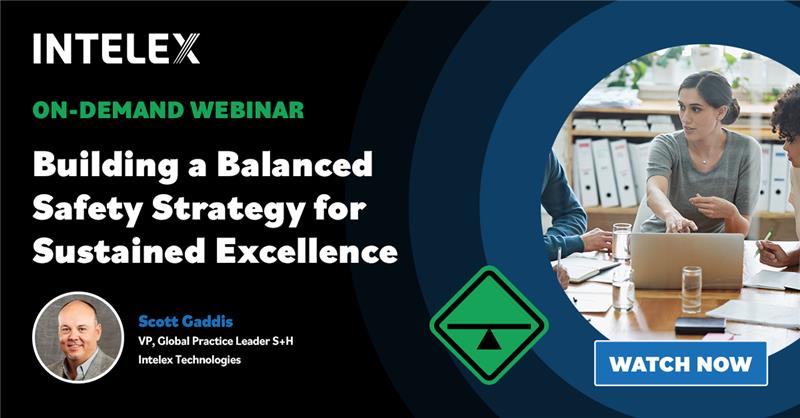
What is balanced safety?
The demands on EHS teams keep growing. With so many competing priorities, your job can feel overwhelming.
The goal of balanced safety is to ensure that no one aspect of safety dominates at the expense of others, fostering an environment where physical, psychological, organizational, and technology factors are all addressed.
In our recent webinar, Building a Balanced Safety Strategy for Sustained Excellence, we covered the foundation of balanced safety, including:
- The challenges EHS professionals often encounter when trying to achieve a better safety balance.
- Where opportunities exist to help balance your safety program and drive the culture you want.
Balanced safety combines workplace safety with related business functions—quality, operations, maintenance, security, risk, and planning—to form an effective safety management system. These interconnected functions directly impact overall workplace safety.
For example, production or operations may ask you to do more or to make more. Many times, the other parts of the integrated management system are a risk in how safety operates.
You can learn more about balanced safety here.
Table of Contents:
- Pressures and challenges affecting safety success
- 5 opportunities for better safety program balance
- Tips to improve performance and deliver the culture you want
- Assess your safety priorities
What are the pressures and challenges affecting safety success?
A well-designed safety management system is like a tower of Jenga blocks. It’s solid until its integrity is compromised. The following five pressures often represent serious threats to the integrity of your Jenga structure.
Efficiency pressure
Deadlines, initiatives to increase output, expectations to maximize productivity—these are all efficiency pressures that often take precedence over safety protocols. They can impact and sometimes even dictate procedures, policies, and the way you run the business.
- While efficiency is a positive force, it can have serious negative consequences on the safety culture.
- Gaining efficiency is good, but EHS practitioners need to recognize when efficiency pressures negatively influence safety.
Cost pressure
Whether out of necessity, desire, or habit, organizations frequently prioritize cost saving measures. This is a particularly popular strategy in times of economic uncertainty and poor market conditions.
- The result of these approaches is often cost pressures that could limit investments for new safety technologies and initiatives.
- Businesses experiencing cost pressures may also find it’s difficult to scale, to pursue new equipment, and even to maintain safety training standards due to cost.
Innovation pressure
Innovation pressure occurs when the introduction of new technologies into your environment threatens or disrupts the way you do safety and health in your business. For example, areas like the operations side of manufacturing are seeing a big implementation push for AI and similar technologies.
For EHS practitioners, it’s important to recognize the downstream effects. Machines may run faster than they once did. Decision-making may shift from humans to technology.
- New technologies, machinery, or processes can sometimes overshadow safety considerations.
Since many innovative initiatives come from the organization’s highest levels, health and safety might be left out of the conversation. EHS must play catch-up to identify areas where innovation pressures impact the safety program.
Fatigue pressure
Health and safety practitioners know that business, personal, economic, and other pressures affect the way people do their work. Fatigue pressure—where workers experience burnout, stress, frustration and other issues—reduces their focus on safety practices.
Burnout isn’t a new phenomenon, but the pandemic pushed it to new heights. Employees also face a multitude of other after-effects:
- They experience more mental health concerns.
- Drug overdoses and substance abuse are an increasing concern among workers.
- In addition, many businesses still haven’t ramped up to a full load of workers. Some simply opted to keep headcount lean, potentially leaving workers to struggle to get by without enough people.
If workers are burned out, stressed, mentally stretched or fighting against addiction, it reduces their focus on following good safety practices.
Read our article, Balanced Priorities as a Safety Manager, for tips to manage stress and avoid burnout.
Conflicting priorities pressure
Leaders may inadvertently create conflicting priority pressure when they implement initiatives that don’t align across the business or exceed the organization’s resources.
- They may want to pursue market expansion, talent acquisition, crisis management and other things that complicate running an effective safety program.
Unfortunately, there’s been a rapid increase in conflicting priorities since the pandemic and the ongoing economic uncertainty and geopolitical risks only add to the problem.
As business leaders work to keep their organizations innovating in difficult environments, EHS practitioners face a growing likelihood that conflicting priorities will negatively impact safety programs.
Where are the opportunities for better safety program balance?
There are five primary areas where EHS professionals are commonly pulled between two sides of the same seesaw.
1. Compliance and culture
Compliance and culture both vie for practitioners’ energy, and both are critically important.
Compliance is about spending time ensuring a robust baseline of regulatory compliance through clear policy, training, and audits.
- For some, there has long been a heavy bias toward compliance as a mandatory part of the role, so identifying ways to manage time to a more ideal balance can be tricky.
There’s also a culture side, which is about spending time engaging employees at every level to foster a culture of safety.
- That means emphasizing shared safety values and encouraging proactive behaviors. Cultural elements are somewhat of a soft skill in EHS, but if you want to achieve world-class performance in your organization, balancing your time to properly nurture the culture side is a necessity.
For EHS professionals whose time is heavily weighted on one side or the other, look for opportunities to change the dynamic. This conversation should happen not only with the safety team, but with the business leadership team so everyone understands where you want to go on your path toward better balance.
Watch our session, How to Engage Employee Stakeholders, for more insights.
2. Managing incidents and mitigating risks
Managing incidents and mitigating risk. Reactive and proactive. It’s an age-old push-pull for EHS professionals.
The priority for most safety professionals is to find a way to track bad things happening in their environments. It’s about:
- managing incidents after they occur,
- spending time developing efficient incident response to negative events, and
- building up protocols to address and learn from them.
But if your program is mostly reactive and your time is focused on incident management, it means there’s probably some imbalance within your management system overall.
Mitigating risk focuses ahead, where you spend time looking at hazards and risk potentials, typically through proactive risk assessments and control measures.
- It includes hazard identifications, audits, issue elimination, and engineering controls. Here, you seek to mitigate the possibility of risk in the environment.
Finding a better balance requires greater emphasis toward being very proactive when mitigating risk rather than reacting to things that happen in the workplace. The system management must be thoughtfully constructed to enable your team to successfully make that transition.
Watch our on-demand session, Transformative Strategies for Proactive Safety, for more advice.
3. Office administration and field work
Most EHS practitioners would probably agree that they spend plenty of time behind a desk. It’s a common imbalance—office administration takes time away from doing field work, where you can engage frontline workers in an authentic and effective way.
Office administration encompasses numerous vital activities.
- The first hours of every day may be spent in the office signing permits, getting people to work, confirming the training plan is correct, and generally checking that things are working as they should. It’s necessary work but it can consume you.
Field work is spending time at the frontline, understanding what the worker is doing and what his or her challenges are.
- It’s about seeing issues firsthand and being able to attend to them immediately, monitoring progress and measuring the safety climate.
How can you pry yourself out of the office role and spend more quality time where safety issues are front and center? Being a visible leader helps to develop balance between the two and create the right split.
Watch our on-demand session, 10 Incremental Ideas to Take Your Safety Culture to the Next Level, for more ideas.
4. Collecting data and using data
Collecting data used to be a big challenge. Now it’s using all that data to drive the desired outcomes. Health and safety teams have spent a tremendous amount of time collecting data and increasing data inputs from various sources to identify risks in the work environment.
Most companies have more data than they can handle.
- The result is often overwhelm and inaction—there’s so much to see that it’s impossible to gain any real insights.
When organizations transition to using data, they can focus on quality over quantity. They transform data into actionable intelligence and use analytics to identify patterns.
- People are the biggest variability EHS has and trying to predict what they’re going to do is very difficult. However, we can certainly predict risk in the work environment, we can isolate some of those hazards, and we can improve our decision making.
Strategic use of technology, including advanced solutions such as AI and machine learning, empowers safety teams to bring balance to the system. You can not only collect data but also use that data effectively and proactively. You get the intelligence you need and enjoy an ideal split of time between capturing data and acting on it.
Watch our session, 5 Elements of a Data-Driven Safety Culture, for more advice.
5. Immediate actions and long-term planning
Health and safety practitioners spend a ton of time responding to urgent safety concerns and taking immediate actions to protect workers and maintain their trust. But managing those open action plans isn’t a complete answer.
- If there are hundreds of open items and you aren’t fixing all the things you see, how well are you really maintaining trust within the environment? Working the list reactively may not be enough.
On the other side is long-term planning, where you spend time developing strategic plans that go after the underlying safety challenges so you can make genuine progress over time.
- It isn’t easy, since you still have some level of need to respond immediately to emergent issues. But by investing more time in long-term planning, you can wield far more control where it matters.
Finding the ideal split reduces the need for immediate responses because the work is more balanced.
Watch our application spotlight, How Safety Analytics Raise the Bar in Operational Excellence, to drive meaningful improvement.
How can you begin to improve performance and deliver the culture you want?
Technology can play a big role in getting you on the path to improving the safety balance in your organization.
- Automation allows you to connect workflows, accelerate activities, and reduce manual tasks.
- Data analytics give you insights that combine culture, incident management, compliance, and risk mitigations to promote a more actionable work plan and a more proactive safety process.blog
- Customized dashboards with tailored views help stakeholders from business leaders all the way to the frontline understand and respond to the things that are important based on individual roles.
- Mobile accessibility extends safety out into the work environment, putting a safety management system in the hands of everyone in the organization to save time. It’s more efficient and more effective.
Assess your safety priorities
If you aren’t sure just how well you’re doing on balancing your time in the different areas, we developed a safety assessment scale that can help you identify where you are.
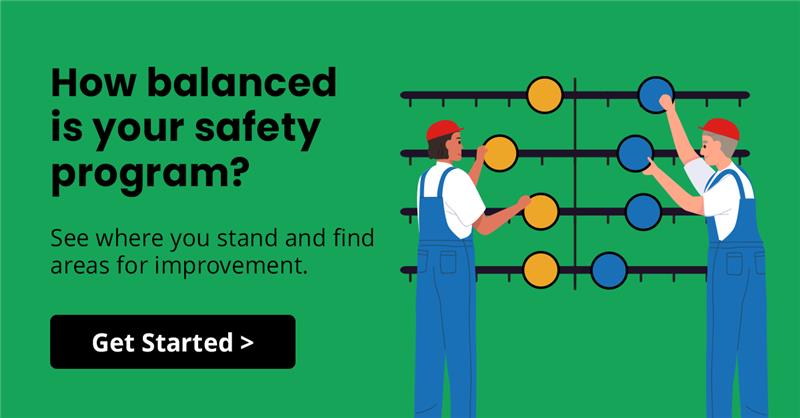
You can use the results to:
- Evaluate your management systems.
- Reflect on the business pressures affecting your environment.
- Consider where you’re spending your energy.
- Develop a plan to put more time into the areas that will help you achieve more safety balance.
How balanced is your safety program? Use our Safety Assessment Scale to find out how close your organization is to reaching its full potential and uncover opportunities across your culture, data, and strategy.