What Incident Management Tools Can Save You
November 18, 2024
5 minute read
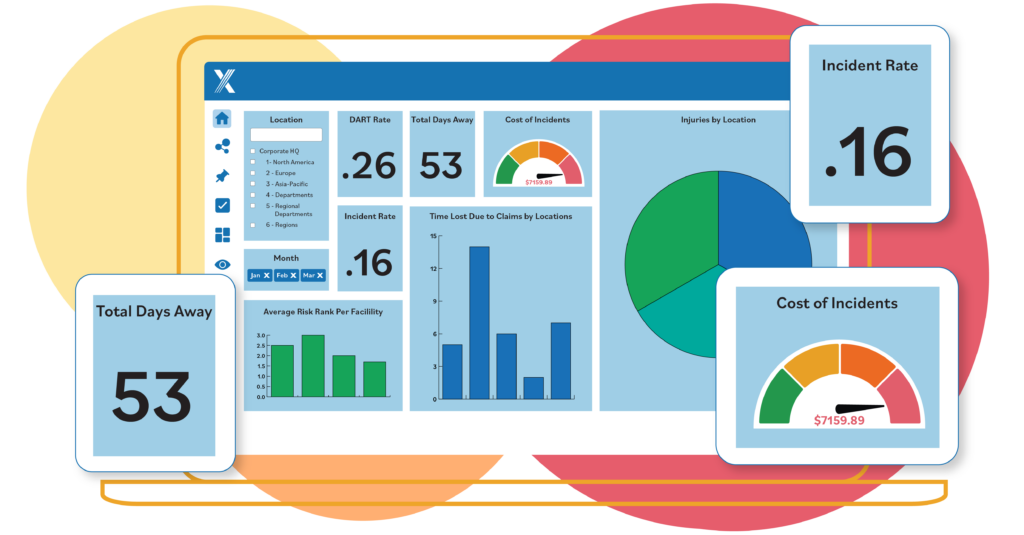
Every incident report is a chance to prevent the next injury. But if your team is still managing those reports with spreadsheets, emails, or multi-system processes, you’re reacting—not leading safety forward.
Manual methods slow everything down:
- Teams can’t act fast when data is delayed. Hazards go unaddressed in the moment, which makes it more likely for the same problems to happen again.
- Without clear insights into why incidents happen, teams end up using quick fixes instead of solving the real problem—so issues keep coming back.
- When it’s hard to track corrective actions, tasks get missed, accountability slips, and safety improvements fall through the cracks—putting compliance at risk.
And the longer these issues linger, the greater the risk of repeat incidents, regulatory fines, and reputational damage. That’s where modern incident management tools make all the difference.
The real cost of not having incident management tools
Across high-risk industries like oil and gas, manufacturing, and construction, safety teams need fast, accurate, and complete incident data. But outdated systems make that nearly impossible.
Here’s what we hear from companies before they switch to digital incident management tools:
- “We couldn’t access the data we needed until it was too late.”
- “Corrective actions were inconsistent—no one knew who was responsible.”
- “Our audit trail was a mess when regulators came knocking.”
Sound familiar?
3 ways incident management tools outperform manual methods
Manual reporting methods are often fragmented. We’ve seen customers excel in three key areas when they switch from manual methods to data-driven options.
- Root Cause Analysis: Identifying underlying causes is challenging without unified data, leading to inadequate preventive measures.
- Corrective Actions: Ensuring that corrective actions address identified issues is difficult without a structured workflow.
- Documentation: Regulatory compliance requires thorough documentation, but paper-based methods often result in incomplete or lost records.
Digital solutions like the Intelex platform help tackle these challenges, streamlining processes, enhancing accuracy and improving overall efficiency.
1. Root cause analysis that gets to the actual cause
Root cause analysis (RCA) helps companies find the real reasons behind workplace incidents so they can stop them from happening again. Intelex has built-in tools to make this easier, like Pareto Analysis, 5-Why’s, and Fishbone Diagrams.
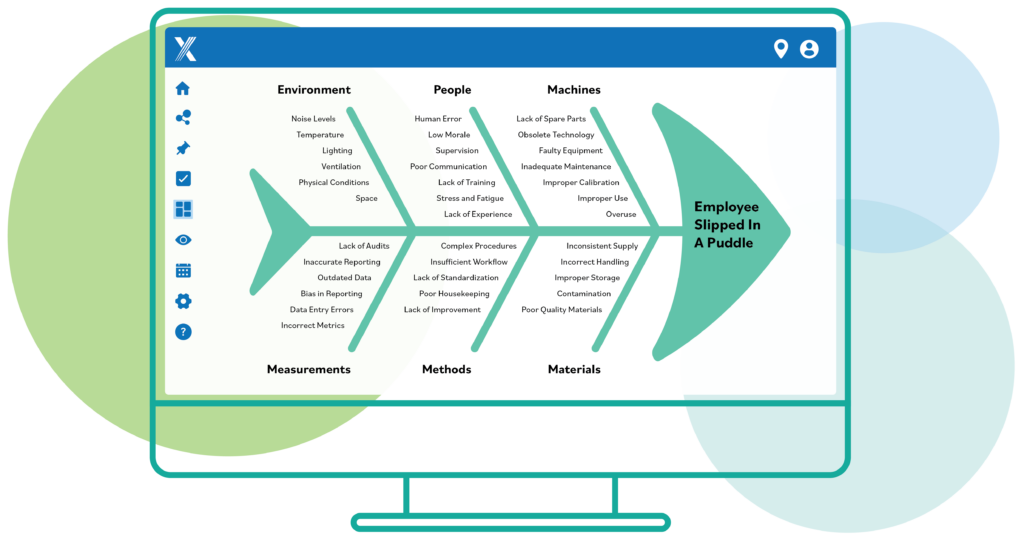
With Intelex, users can also use historical data to spot patterns and common risks. This helps safety teams take the right actions to fix problems and prevent them in the future.
The root cause analysis tool also help different teams work together by improving communication and making sure everyone is on the same page.
Success story: George’s Inc. relied heavily on lagging indicators to assess safety performance. This limited their ability to proactively prevent incidents. Since implementing Intelex, George’s Inc. has reduced their DART (Days Away, Restricted, or Transferred) rate by 54%.
2. Corrective actions that don’t slip through the cracks
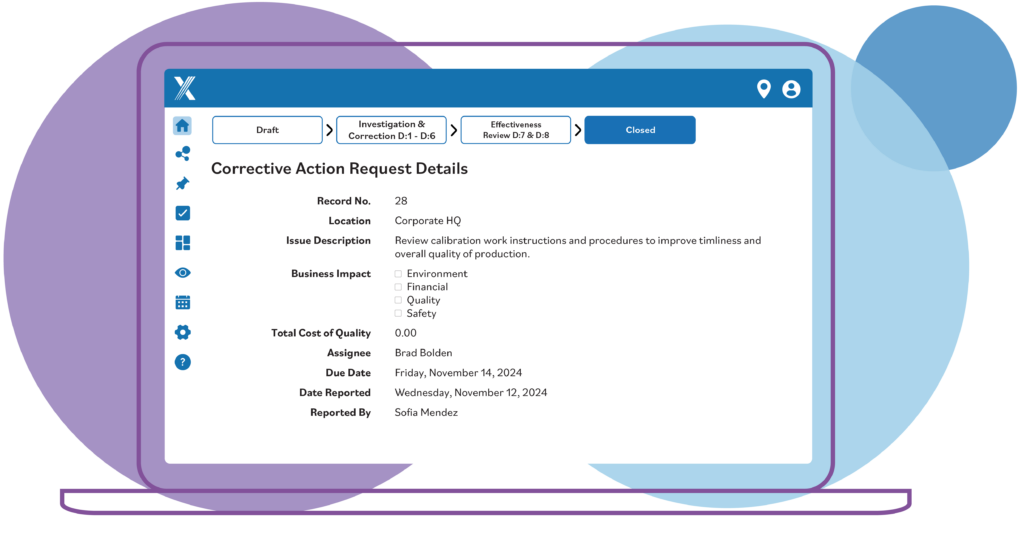
Corrective action means finding and fixing the main cause of a problem so it doesn’t happen again. Intelex helps by automating this process, making it faster and easier to stay on track and follow safety rules.
With Intelex, each step—from spotting the problem to solving it—is clear and organized. Teams can set deadlines, assign tasks, and avoid missing steps, so nothing falls through the cracks.
Real-time dashboards let safety managers see what’s going on across all teams. They can track progress, make sure people are doing their part, and quickly spot any delays or problems.
Success story: Manufacturing company, Coats, experiencing time-consuming, error-prone safety reporting used Intelex as part of their Journey to Zero strategy, to improve reporting efficiency and boost corrective actions closed within 30 days by 89%, up from 39%.
3. Improved documentation and compliance
Intelex makes safety incident reporting easier by giving real-time updates and keeping all incident data in one place. This helps safety managers and teams respond quickly with the most up-to-date information and stay on top of safety rules.
Because everyone can see what’s happening right away, it’s easier to make fast decisions and keep track of investigations as they happen.
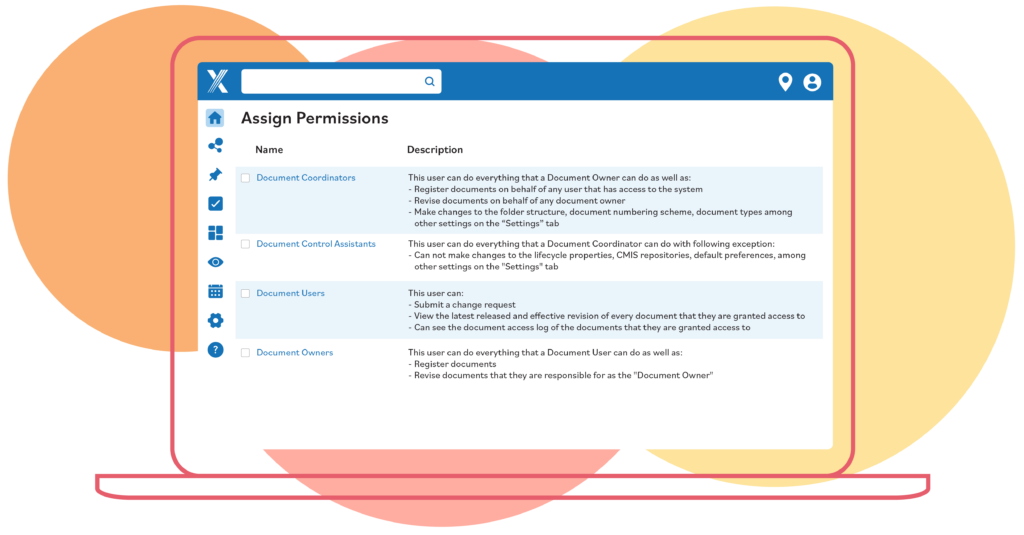
All safety reports and documents are stored in one secure system, so teams don’t have to search through emails or different departments to find what they need. With custom access settings, only the right people can see private or sensitive information.
This safe and organized system also keeps a full record of who did what, helping teams stay compliant and ready for audits. Overall, Intelex gives everyone the tools they need to build a safer workplace.
Success Story: Johnson Matthey, a global leader in sustainable technologies, used to rely on paper-based systems that caused delays and repeated work. After switching to Intelex, they cut down paperwork by 98% and improved efficiency, making it easier to get certified and connect multiple locations smoothly.
Ready for proactive incident management tools?
Manual incident reporting is costing your team time, clarity, and safety. Digital incident management tools like Intelex give you:
- Faster investigations
- Better accountability
- Clearer insights
- Stronger outcomes
Want to see what Intelex can do? Create your personal product demo tour.
Choose from pre-made demos for health and safety, risk management, environment and sustainability, and quality and supplier. Or create your own with the applications that matter most to you.