Wired for Safety: Electrical Hazards in the Workplace and Best Practices to Keep Employees Safe
September 10, 2024
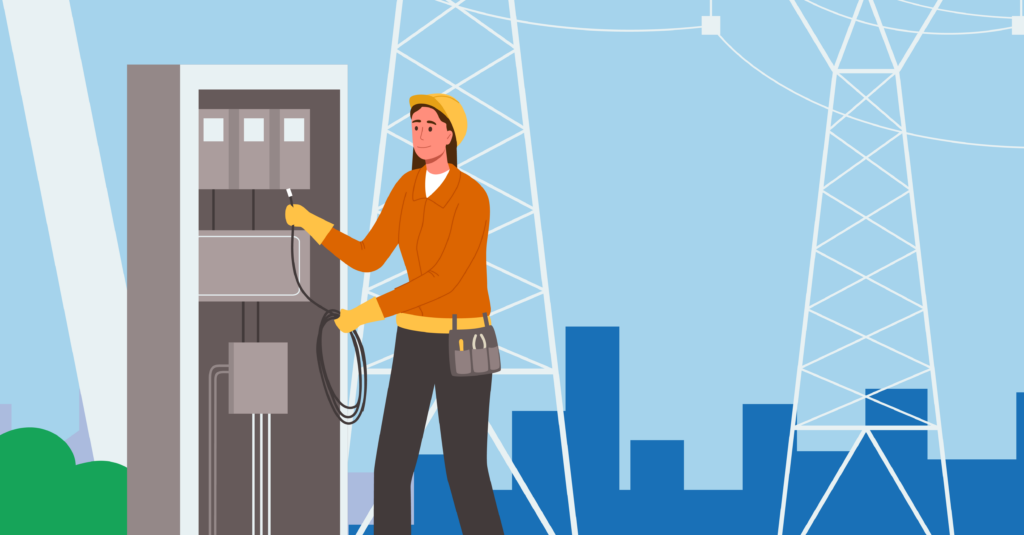
Electrical hazards are present in many industries. Healthcare providers interact daily with powered patient monitoring equipment. Retail establishments rely on powered displays and connected kiosks to help move customers through the buying experience. Any of these machines could create an electrical safety risk to workers. Employees in construction, the oil and gas sector and utilities and energy face elevated risks due to the nature of their environments, and additional protections may be needed to keep them safe.
At a regional water facility in South Carolina, a worker cut a live wire while attempting a repair on an HVAC unit. He died after being electrocuted. In an incident at a Utah restaurant, an electrician was electrocuted while working on an appliance. The severity of the electrocution prevented paramedics from immediately transporting him to the hospital, and despite lifesaving attempts, he was pronounced dead soon after.
Electrical systems and components are present in nearly every workplace, which means these hazards aren’t just concerns for those who interact with electricity services and related components as part of the job. A worker cleaning windows at a multi-unit residential building in British Columbia, Canada, was seriously injured when the cleaning pole they were using touched a high-voltage power line overhead.
Identifying and understanding electrical hazards is one step in ensuring workers are safe, no matter their role or job setting. Safer workplaces must also incorporate electrical safety best practices and leverage processes and tools that empower employees to mitigate risks and avoid accidents.
What is Electrical Safety and What are Electrical Hazards?
The most common electrical hazards include shock, arc flash and fire risks. An electrical shock occurs when someone comes in contact with electricity and the current enters their body, either by directly touching the electrical source or by touching a sufficiently conductive object that is touching the source. A single contact with an energized wire or other component can cause injury or death. An arc flash, also called a flashover, results from an arc fault explosion that can occur in many situations, including when poor connections create a hazard or when the wrong surface is touched with a test probe or other instrument. The heat generated by an arc flash can be hotter than the surface of the sun and has the potential to cause deadly skin burns and even melt metal. Fire risks often accompany electrical safety incidents and increase the danger to workers. These events may inflict injury directly or quickly ignite nearby materials and create a wider workplace emergency. Sometimes, they may also produce noxious smoke and other dangerous byproducts.
The risks to workers from electrical hazards are so pervasive, persistent and dangerous that several regulatory standards have been developed to encourage employer compliance and enhance worker safety. The Occupational Safety and Health Administration (OSHA) standards in the U.S. include 29 CFR 1910 for general industry and 29 CFR 1915, 1917 and 1918 for maritime. In addition, 29 OSHA-approved State Plans and the National Fire Protection Association (NFPA) 70E standard provide further guidance to help maintain electrical safety across various workplace environments and settings. The British Standards Institution developed BS 7671 IET Wiring Regulations, the UK standard outlining requirements for electrical installation safety. In the EU, the Low Voltage Directive (LVD) 2014/35/EU applies to commercial as well as consumer electrical equipment designed to operate within specified voltage limits. These standards offer suggestions for best practices to support safe work environments and outline potential repercussions for noncompliance.
Electrical Safety By the Numbers
The most recent data from the U.S. Bureau of Labor Statistics (BLS) shows that 145 workers died from exposure to electricity in 2022, with construction recording the highest number of fatalities for both direct and indirect exposures. In the same year, 2,950 occupational injuries were caused by exposure to electricity. Eight hundred of those cases experienced 31 or more days away from work.
The costs of electrical hazards can be high. When a worker is off the job to recuperate, the entire team may experience a drop in productivity. This can lead to expensive project delays or additional budget outlays for temporary or contract staff to fill the gaps. There are other financial impacts of electrical accidents, too. OSHA’s Safety Pays Individual Injury Estimator puts the total direct and indirect costs an employer will likely bear for a single electrical shock incident at over $330,000. Depending on the situation, there may be other considerations. Lawsuits are common, and many involve steep legal fees. Fines may also be levied against the business if the incident is found to be the result of noncompliance with applicable regulations or laws.
Electrical Challenges and Best Practices
While electrical hazards exist in nearly every sector, some industries have unique challenges.
Construction
The environments construction workers are exposed to are typically in progress or undergoing significant changes. That means there is a high likelihood of encountering exposed wiring and temporary electrical setups. On a construction jobsite, heavy machinery may be moving around, which poses a risk if large booms or other parts contact electrical services that haven’t yet been secured or walled in.
A primary challenge in construction is managing safety on dynamic and constantly changing jobsites. The state of electrical work may differ from day to day, and the workers assigned to a given site might also change frequently. Given the risks present in the construction sector, electrical safety best practices often include regular inspections to ensure that appropriate measures are in place to reduce the hazard to workers. Proper grounding and the use of ground-fault circuit interrupters (GFCIs) can also help mitigate these risks while construction work is ongoing.
Oil and Gas
In oil and gas, work locations may have explosive atmospheres that create increased electrical safety risks. High-voltage systems abound in this sector and, coupled with the extensive network of remote operations, can significantly complicate safety efforts. Access to emergency services and other supportive infrastructure is often limited, and the long response times for outside help increase the dangers of electrical incidents.
Managing safety in these harsh and hazardous environments requires planning and dedicated focus on the jobsite. What may be a simple mistake in another type of workplace can quickly become life-threatening for an oil or gas operation. The diligent use of intrinsically safe equipment is one proactive step businesses can take to help mitigate electrical risks to workers. Area classifications provide employees with essential guidance on the probability of potentially hazardous materials in specific locations. Continuous monitoring is another option that can help detect hazards early and allow workers on remote sites to take corrective action and avoid incidents.
Utilities and energy
Those working in utilities and energy are often around high-voltage transmission equipment, substation facilities and other power distribution installations, where risks are high and ever-present. Because these environments are the backbone of the electrical services that commercial and residential customers rely on, workers are often required to work under less-than-ideal conditions close to volatile electrical loads and equipment. Carrying out emergency repairs during inclement weather and upgrading equipment under tight deadlines to minimize disruption to community customers all heighten the risks.
Ensuring safety across these potentially vast and often distributed infrastructures requires unwavering attention to risk mitigation. Comprehensive training and diligent adherence to safety protocols are a must. Workers should have easy access to properly fitted protective equipment to keep themselves and their colleagues safe. Employers in the utilities and energy sector should also be vigilant about regularly upgrading any aging or deteriorating systems or infrastructure to ensure components have the latest safety technologies and mechanisms.
How Intelex Can Help
A comprehensive safety management strategy is critical to preventing electrical exposures and mitigating hazards. The right technology can ensure your team has the tools to avoid accidents and keep workers safe. Intelex provides an integrated platform to manage all aspects of electrical safety, from risk assessments to incident reporting. Our solutions offer a centralized and intuitive way to help make workplaces safer.
Employers must maintain regulatory compliance, even as work environments evolve and employees move from one jobsite or remote location to another. With Intelex, you can stay up to date with the latest regulatory requirements and ensure compliance with the standards that apply to your business, including OSHA, NFPA, BS 7671 and the Low Voltage Directive 2014/35/EU.
Ensuring workers have the proper training and awareness to operate safely around electrical equipment and related hazards is vital. You can leverage Intelex to implement and track training programs to ensure all employees are knowledgeable about electrical safety best practices.
Incident reporting and analysis are core elements in understanding and mitigating workplace risks. Intelex empowers your staff to easily report incidents and allows supervisors or health and safety teams to analyze data, identify trends, and prevent future occurrences.
With the Intelex platform, you can bring your electrical safety program into one place and ensure your preventive maintenance efforts are on target. Use the solution to schedule and manage preventive maintenance and confirm all electrical equipment is in safe working condition.
Many workplaces, particularly those in high-risk industries, have unique requirements. A customizable solution empowers your teams to streamline the processes that are most important to your operations. You can tailor Intelex’s solutions around your specific electrical safety management needs.
Maintaining a strong focus on electrical safety is critical in every industry. Construction, utilities, energy and oil and gas employees often work in uncommonly hazardous environments, and a rigorous electrical safety program is vital to keeping your teams safe. Intelex’s solutions offer highly customizable tools for improving electrical safety and ensuring compliance. We can help you understand your risk environment and tailor tools to reduce the time and effort required to gather, analyze and act on electrical safety data.