How Machine Guarding Prevents Injuries and Boosts Compliance
July 17, 2024
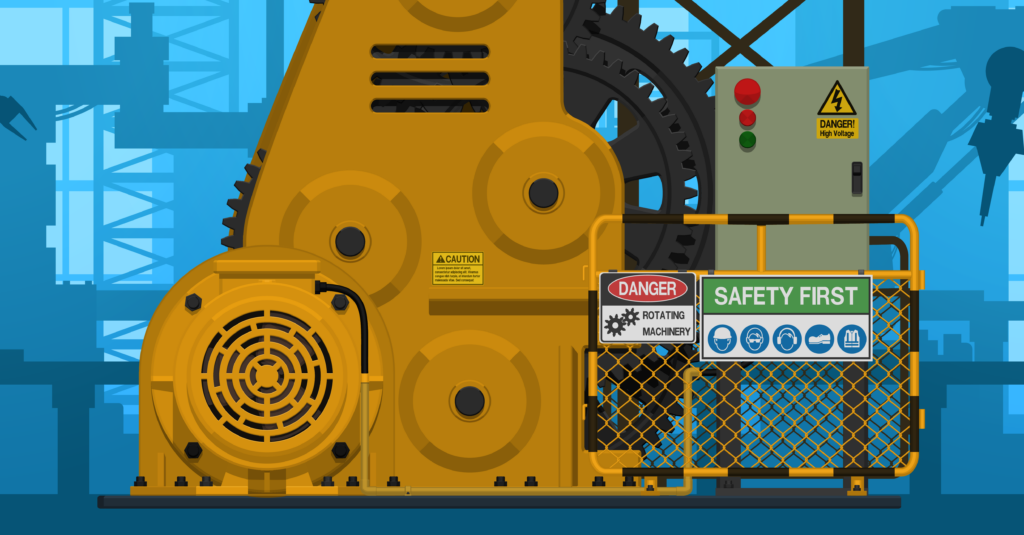
Unguarded machines present serious safety hazards in numerous industrial environments. Whether on the assembly lines of the automotive industry or in the confines of metalworking shops, workers face daily risks interacting with hazardous machinery. The U.S. Occupational Safety and Health Administration (OSHA) reports approximately 18,000 severe injuries—including burns, crushed hands or fingers, lacerations, amputations and blindness—due to inadequate machine guarding every year. These mostly preventable incidents also result in over 800 fatalities annually.
Machine guarding consistently appears on OSHA’s Top 10 Most Frequently Cited Standards list, with 1,635 violations recorded in 2023 alone. This blog explores the critical role of machine guarding, the hazards it mitigates, different methods for implementation and Intelex’s role in enhancing safeguarding practices.
Machine Guarding: What Is It and How Is It Regulated?
Machine guarding involves the use of safety barriers and protective devices to shield workers from hazardous parts and functions of machinery during operation and maintenance activities. These include methods such as fixed guards, interlocking guards and two-hand operating devices, designed to reduce the risk of severe injuries and fatalities.
Compliance with regulatory requirements is essential for ensuring proper worker protection. In the U.S., specific machinery standards are outlined under OSHA’s 29 CFR 1910 Subpart O. In Canada, provincial laws and guidelines, including those from the Canadian Centre for Occupational Health and Safety (CCOHS), govern machine guarding. In Europe, the European Union’s Machinery Directive 2006/42/EC specifies health and safety standards for machinery, while in the UK, post-Brexit, the Health and Safety Executive (HSE) ensures compliance with both national and relevant EU regulations. On a global scale, the International Organization for Standardization (ISO) and the International Electrotechnical Commission (IEC) provide standards that promote consistency in machine safety practices worldwide.
Not adhering to regulations can result in severe penalties and significant operational risks. A notable example is the case of an Ohio aluminum parts manufacturer fined $1.7 million by OSHA after a fatal incident involving a machine’s barrier door. Clearly, beyond the financial impact, such violations can also seriously compromise the sustainability and reputation of non-compliant organizations.
Common Machine Guarding Hazards
Each piece of machinery, from table saws and mechanical power presses to conveyor belts and robotic arms, poses unique mechanical and non-mechanical hazards. To address these risks, machine guarding serves as a critical line of defense for workers in a wide range of industries such as construction, energy, mining and metals, agriculture, manufacturing and food and beverage. Common hazards include:
- Hazardous Mechanical Motions:
- Rotating Parts: Rotating parts such as gears and rollers can catch hair and clothing, pulling hands and arms into hazardous positions and causing severe injuries.
- In-running Nip Points: These occur where two parts move together, for example between a belt and roller, risking entrapment of body parts.
- Reciprocating Motions: Found in presses and shapers, these back-and-forth movements can trap and injure body parts.
- Transverse Motions: These involve continuous movement of materials that can pull in nearby objects, including body parts.
- Hazardous Actions at Points of Operation:
- Cutting: Machines such as saws and cutting discs perform sharp cuts that can pose severe risks.
- Punching: Punch presses create holes in materials through a downstroke motion that can be hazardous to operators.
- Shearing: Shearing machines apply force to cut materials like metal, which require rigorous safeguards to prevent amputation risks.
- Bending: Machines that bend metal or other materials can create pinch points and other hazardous interactions.
- Non-Mechanical Hazards:
- Flying Chips and Sparks: Operations such as grinding or welding can eject particles or sparks, posing risks to eyes and skin, which require protective guards and barriers.
- Thermal Hazards: Machinery operating at high temperatures can cause burns or scalds. Heat shields and other barriers are crucial to protect workers from heat-related injuries.
- Electrical Hazards: Electrical machines can cause shocks, arc flashes or burns, with effective guarding involving insulation and grounding.
- Noise Hazards: High noise levels from machinery can lead to hearing loss that can be mitigated by noise-reducing enclosures or barriers.
- Chemical Exposures: Hazardous emissions from industrial processes necessitate the use of specialized guards designed to shield workers from harmful exposure.
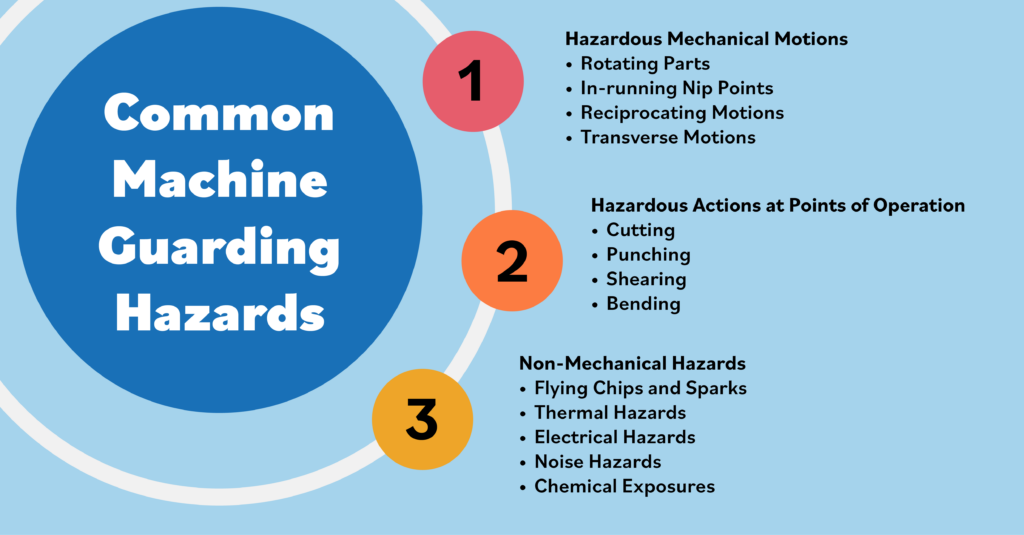
Key Methods of Machine Guarding
Effective machine guards must meet several critical requirements. They should prevent contact with hazardous parts, remain securely in place and must not create additional hazards or interfere with machine operations. The five key safeguarding methods include:
- Guards: Physical barriers preventing contact, including fixed guards that permanently enclose hazards, interlocked guards that halt operation if altered, adjustable guards for varying material sizes and self-adjusting guards that adapt automatically.
- Devices: Tools that restrict access to hazardous areas, featuring sensors like photoelectric and radiofrequency that detect intrusions, electromechanical devices that stop machines when triggered and safety features such as pullback devices and trip controls.
- Automated Feeding and Ejection Mechanisms: Systems that automatically handle materials and reduce direct exposure to hazards.
- Machine Location or Distance: Placing machinery at a safe distance from operators to reduce risks of contact.
- Miscellaneous Aids: These include shields to contain debris, holding tools for safer material handling and awareness barriers that highlight hazardous areas.
Additionally, effective lockout/tagout (LOTO) procedures remain a critical safety measure in many industries. These procedures ensure that machines are properly shut off and unable to energize or start up during maintenance or servicing. By incorporating machine guards along with safety measures like LOTO, organizations can significantly improve workplace safety and protect employees from serious injuries or fatalities.
Advantages of Machine Guarding
Machine guarding is an essential safety measure in high-risk industries, effectively preventing accidental contact with hazardous machine parts. It not only reduces the risk of severe injuries but also demonstrates an organization’s commitment to prioritizing employee well-being.
In industries that depend heavily on machinery, safety—especially through machine guarding— directly correlates with productivity by minimizing accidents and ensuring continuous operations. For example, in the aerospace sector, machine guarding protects workers during the precise assembly and testing of components. In the food and beverage industry, it helps maintain smooth production lines, adhering to strict health standards and preventing safety breaches.
The financial impact of machine guarding is significant. According to the National Safety Council, workplace injuries cost the U.S. economy $167 billion in 2022, including medical expenses, lost wages and productivity losses. Demonstrating the effectiveness of preventive measures, a randomized study involving 40 small metal-fabrication businesses showed that machine-guarding measures improved safety scores by 13% to 23%. This improvement not only enhances safety but also translates into financial savings by reducing the costs associated with workplace injuries and operational disruptions.
Challenges in Implementing Machine Guarding
Although the advantages of machine guarding are clear, implementation faces challenges such as insufficient understanding of standards, lack of safeguarding processes and limited resources. Many organizations fail to fully comply with OSHA’s requirements, leading to inadequate protection. Effective safety protocols need input from operators, maintenance personnel, supervisors, engineers and safety professionals. Without robust processes, such as design reviews and risk assessments, identifying and mitigating risks are difficult. Additionally, safeguarding can be costly, averaging $2,500 per machine and another $2,500 per day for assessment labor. Improper design, installation and non-compliance of older machines with modern safety regulations further complicate the implementation process. Regular inspections and maintenance, along with retrofitting guards, are crucial to bring older machines up to current safety standards.
Organizational culture also impacts the effectiveness of machine guarding initiatives. Without the support and engagement of workers, these initiatives can never truly succeed. Engaging employees requires management to lead cultural changes, offer thorough training and establish direct processes for incident investigation and prevention to cultivate a safety-first mindset across the entire organization.
How Can Intelex Help with Machine Guarding?
Intelex offers a comprehensive suite of Environment, Health and Safety (EHS) management solutions that help organizations effectively implement and manage machine guarding. Key features include:
- Identifying and Assessing Machine Guarding Needs: Intelex’s Job Safety Analysis application conducts thorough risk assessments to identify areas requiring machine guarding. Integrated with the Incident Reporting application, it ensures all potential hazards are promptly addressed.
- Tracking and Managing Machine Guards: The Audit Management application schedules regular inspections and maintenance of machine guards, proactively preventing accidents.
- Ensuring Compliance with Relevant Standards: Automated updates and alerts keep organizations compliant with the latest machine guarding standards and regulations.
- Documentation and Reporting Capabilities: Intelex’s Incident Reporting and Document Control offer robust documentation and reporting capabilities, supporting audits and inspections and maintaining clear records of machine guarding practices and compliance efforts.
- Training and Awareness: Intelex’s Training Management application provides extensive training solutions, covering standards review, understanding machine guards, reporting procedures for damaged or missing guards and the organization’s lockout/tagout program, helping employees stay informed and proactive in workplace safety.
Integrating these advanced tools allows organizations to take a holistic approach to managing machine guarding and overall safety, helping to safeguard workers and enhance operational efficiency.
Conclusion
Machine guarding is a crucial aspect of workplace safety, protecting workers from incidents and ensuring regulatory compliance. Effective measures can drastically reduce typical machinery-related injuries, such as crushed hands, severed limbs, lacerations, abrasions and amputations. Injuries as severe as these can lead to permanent disability, profoundly affecting workers’ lives and livelihoods.
Achieving zero accidents and injuries should be a top priority in any workplace. Advanced EHS software solutions support this goal by enhancing the management of machine guarding protocols through risk assessment, real-time monitoring and compliance tracking. By prioritizing effective safeguarding and utilizing modern EHS applications, organizations can create safer work environments and advance toward the ultimate goal of zero harm.