Building a Safer Tomorrow: Challenges and Solutions in Construction Site Safety
February 14, 2024
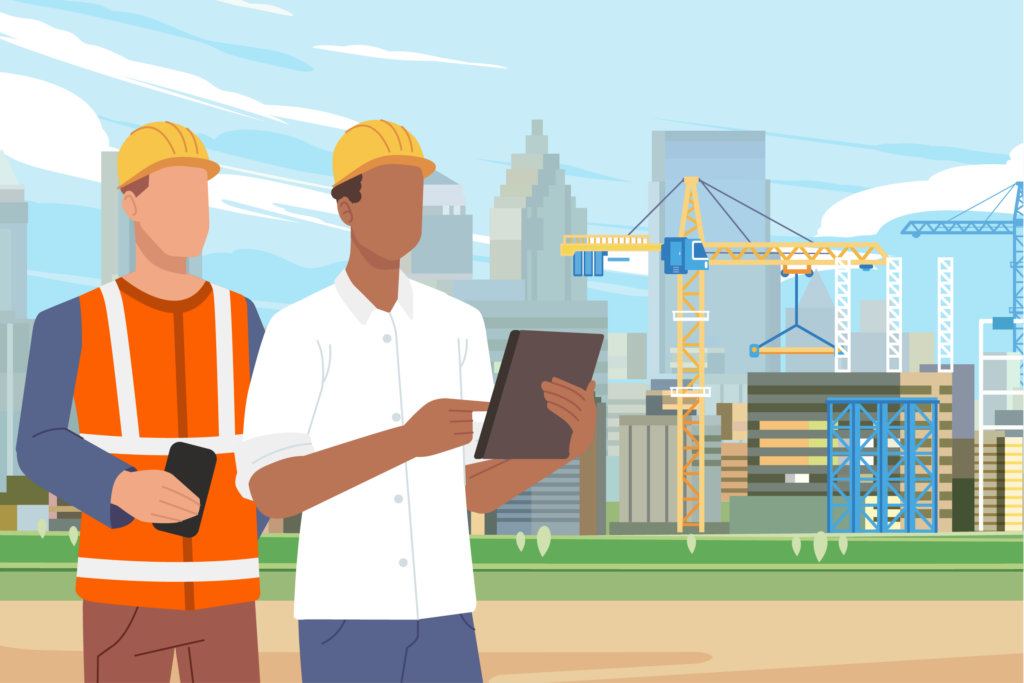
On the afternoon of August 24, 2020, a construction worker employed by an electrical contractor was preparing to install a new power line between two utility poles at a Tennessee construction site. The worker threw the guide twine, pulled the cable toward the next pole, but it arched higher than intended and contacted the distribution power lines. Flowing through those lines were 2,700 volts of electric current, which traveled down the guide twine to the worker, who was electrocuted.
Just a few weeks earlier a UK construction worker was crushed underneath concrete after a partial wall and roof collapsed during demolition work on a site. He was pronounced dead on the scene.
Sadly, this kind of day is often the rule rather than the exception in the construction industry, both in the U.S. and around the world, with workers routinely suffering fatal and life-altering injuries while working to build the vital infrastructure on which we all depend.
This blog will examine what companies are doing to improve construction site safety in the face of such stark circumstances. It will examine how they are handling compliance regulations, how innovative technologies such as wearables are helping, the latest training strategies and what the future of construction safety might look like.
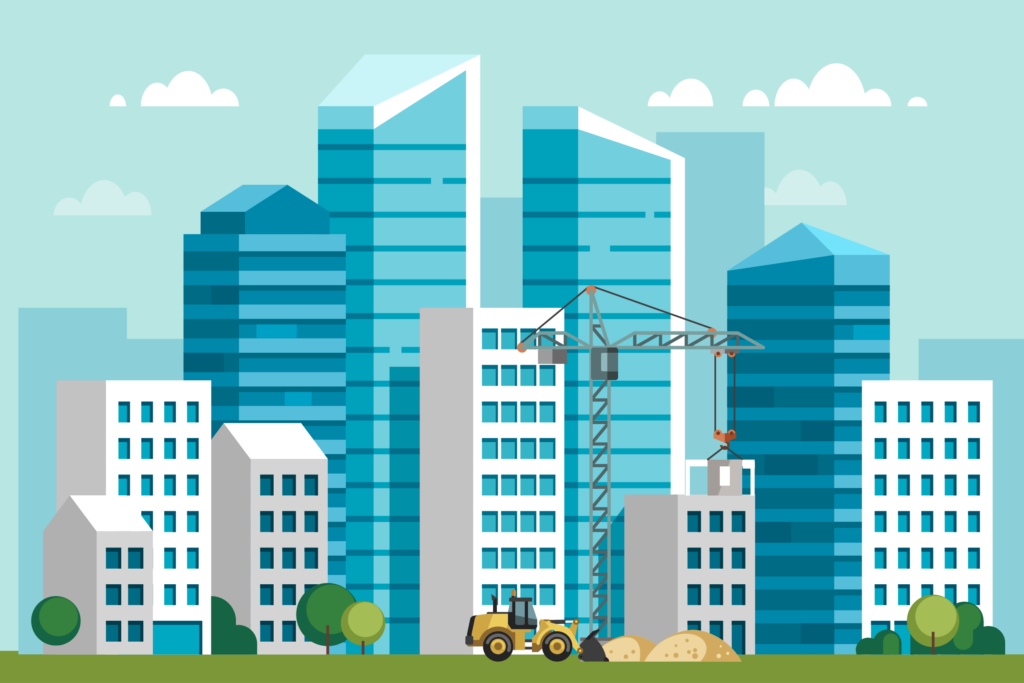
Construction Compliance
OSHA’s Top 10 list of most frequently cited standards for 2022 includes five that specifically mention the word “construction” in their title: Fall Protection (Number 1), Ladders (Number 3), Scaffolding (Number 5), Fall Protection Training (Number 8) and Eye and Face Protection (Number 9). Additionally, the Bureau of Labor Statistics found that there was an 11 percent increase in construction fatalities in 2022 from the previous year. In the UK, the most work-related deaths were in the construction industry, up more than 50 percent from 2021.
What these and other statistics reveal is a very simple and well-known fact: construction is often an extremely dangerous occupation. While standards set by OSHA, HSE and other similar regulatory bodies around the world have had a tremendously beneficial effect on worker safety, Greg Sizemore, vice president of health, safety, environment and workforce development at Associated Builders and Contractors (ABC), reminds us that these standards are “not to be considered as the highball in safety performance, but the bare minimum.”
A construction company that puts up industry-leading safety performance numbers is one that has a safety-focused culture in place, and that culture starts right at the top with the CEO, Sizemore adds.
“[Workers] will see and recognize whether that leader is walking the walk and talking the talk. So, as a CEO, when you go out to a construction site, are you wearing the same PPE that you’re requiring your employees to wear? Or are you still in your loafers and your khakis and your Ray-Bans, as opposed to steel-toed boots, a hard hat and safety glasses?”
If it’s in place at those corporate office heights, a culture of safety will conceivably cascade through lower management ranks and onto the actual construction sites.
While the commonly cited OSHA standards are not likely to be reduced in frequency any time soon, Sizemore does expect to see a growing emphasis on substance abuse policies.
“As an industry, we cannot allow substances to take over. If your son or daughter is rigging the load below a tower crane, and that operator happens to be under the influence of an illegal substance as they’re pulling the levers and lifting that load, you’d want to know that that operator is in 100-percent tip-top capacity to do their job.”
In the United Kingdom, many observers expect the tragic Grenfell Tower fire of 2017 to continue to influence future regulation directions set by the Health and Safety Executive (HSE), the U.K. government agency that oversees workplace health and safety.
“This will include improvements in building standards, governance, fire safety provisions and maintenance and more. The impacts of this will be very far-reaching,” says Paul Humphreys, head of health and safety at Forterra, a U.K.-based manufacturer of clay and concrete-based building materials.
Construction Safety Training Is Key
Prioritizing safety is a smart business decision. A well-executed safety and health program yields a return on investment, saving $4 to $6 for every $1 spent according to OSHA. Beyond financial benefits, implementing safety measures correctly results in reduced costs, heightened productivity and improved employee morale – making it not just a necessary practice but also a strategic advantage.
Effective training is key to keeping construction workers safe on the job. When workers are given comprehensive training on performing their jobs securely, there is a notable reduction in accidents and incidents on construction sites.
For global construction companies, training is complicated – high turnover and market volatility pose challenges, along with managing a diverse workforce with individuals from various cultures, backgrounds and languages. Navigating the rules, regulations and requirements associated with each location adds an extra layer of complexity.
During the pandemic, many construction companies had to cut back on staff training and upskilling to facilitate new, rigorous health and safety procedures, allowing workers to carry out their jobs safely.
Since then, short training courses have proven to be effective and continue to be popular. Many companies have adopted the use of software to provide workers with interactive courses. These software tools often double up with mobile apps, enabling employees to learn and report hazards on-the-go, fostering communication among the workforce.
At Intelex, bulletins are a form of communication akin to targeted, bite-sized public service announcements (PSA) meant to deliver relevant information and training to workers in the moments when the information has maximum value. Once a bulletin has been delivered, the sender can monitor engagement, checking to understand who has seen the information and how they have responded.
Whether the training is virtual or in person, Sizemore stressed the importance of verification of skills learned once the exercise is completed.
“The thought of someone simply being chained to a desk or staring at a monitor for 30 minutes on a particular topic, and that information being something that they will immediately take onto the job, is fairy dust.”
Therefore, there must be a way to justify that individual’s competence in the task they are training for. This can take the form of a simple Q and A from the supervisor.
“It doesn’t have to be an inquisition. It’s saying, ‘Since you now know how to inspect a grinder before you use it, or since you learned what personal protective equipment you need to have on to use this tool, show me before you start to do it.’”
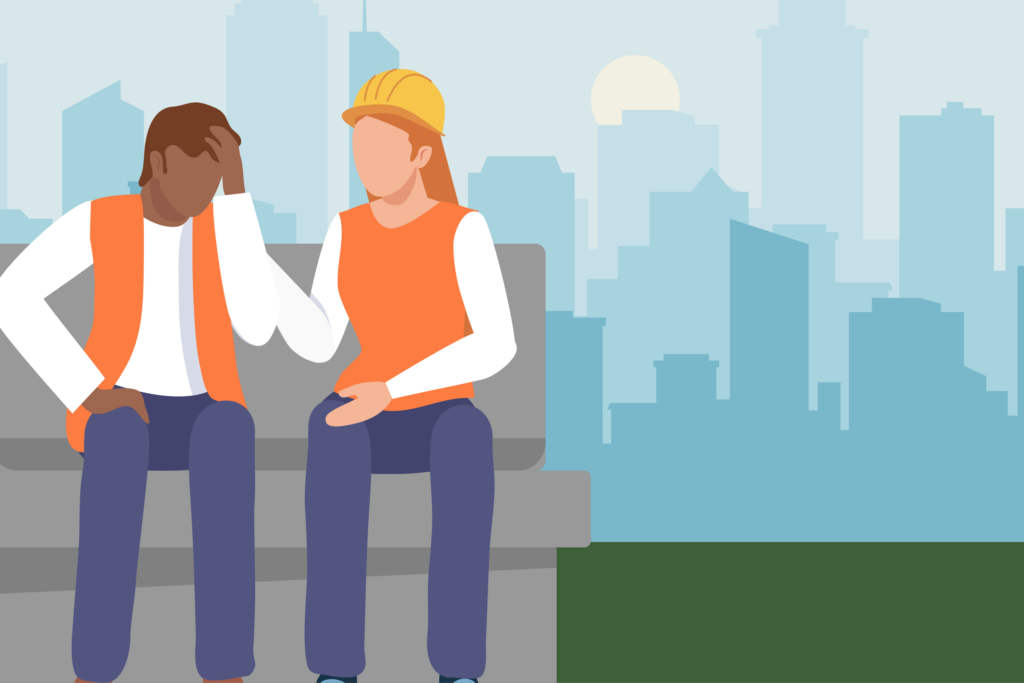
Mental Health and Wellbeing in Construction
The impact of the pandemic has underscored the urgency of addressing mental health concerns in the construction sector, known as Total Human Health. This concept considers the entire well-being of an employee, encompassing physical safety and mental health, addressing issues such as anxiety, depression and suicide.
“The isolation of social distancing had a significant impact on people, and we need to take this as an opportunity to improve our industry and expand our safety dedication,” Sizemore said.
Disturbingly, the construction industry has the second-highest number of suicides across all sectors, with rates well above the national average. According to the CDC, the average suicide rate is 17.8 per 100,000, while in construction, it is significantly higher at 56.0 for males and 10.4 for females.
This challenging period serves as an opportunity for the industry to reevaluate and enhance its commitment to safety, expanding it to encompass not only physical aspects but also the mental health of its workforce.
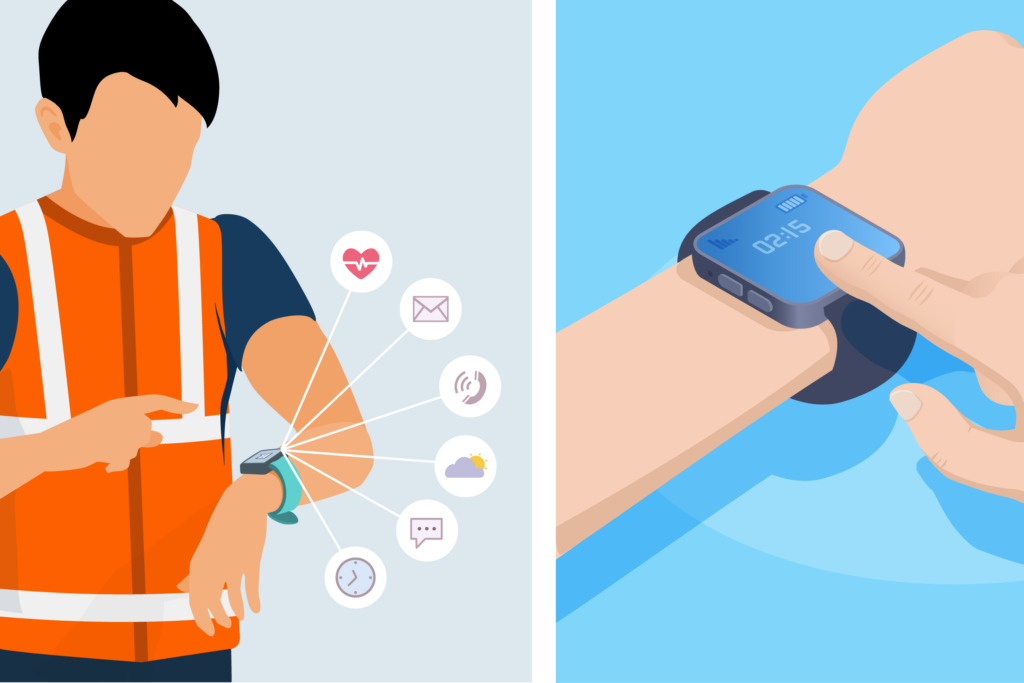
How Construction Wearable Technology is Helping
Fortunately, many new technologies have become available to help increase construction site safety. One popular item being adopted is wearables—garments or other objects containing electronic sensors that can be worn just like any other typical work garb, such as safety vests, gloves or protective eyewear.
Research provides compelling evidence that wearables can make a difference. A 2019 study looking into their effectiveness evaluated 251 NIOSH Fatality Assessment and Control Evaluation (FACE) reports and concluded that the active hazard in 73 of them (29 percent) could have been prevented with a wearable device. The report also looked at 29 cases from 2018 in the OSHA archives and revealed that wearables could have played a role in preventing one-third of them.
Forterra has invested in hand-arm vibration monitoring equipment from Reactec. Hand-Arm Vibration Syndrome (HAVS) can result in loss of sensation in the fingers, loss of grip strength and bone cysts in the fingers and wrists, among other injuries.
The Reactec system includes a wristwatch-like device that informs the wearer of their exposure by calculating and displaying in real-time their HAVS risk assessment exposure points. Sound and vibration alerts let them know if they are going over their exposure thresholds.
“We are also always looking to upgrade our forklift truck and mobile plant technology to improve vehicle and pedestrian safety,” adds Humphreys.
Forterra regularly reviews systems such as that from ZoneSafe to determine if they could be a good fit for the company’s work environment. ZoneSafe’s Vehicle to Person Alert system works by identifying tags worn by pedestrian workers, who are warned of approaching vehicles through tag vibration. Vehicle drivers are alerted to the presence of pedestrians via an in-cab control unit. The detection zone’s range can be adjusted from three to 10 meters. It can also detect through walls and racking.
How Construction Safety Software Helps Reduce Risks
While other technologies may bring efficiency gains to specific aspects of construction operations, health and safety software stands out as an indispensable investment for ensuring the well-being of the workforce, reducing accidents and safeguarding the overall success and reputation of the company.
With health and safety software, there are a variety of tools, such as Safety Observations, Incident Management and Job Safety Analysis (Task-Based Risk Assessment) that empower construction companies to actively monitor and address safety concerns in real-time, fostering a culture of proactive risk management.
Safety Observations, for example, enable workers to promptly report safety issues, contributing to a swift and agile response mechanism. Incident Management streamlines the handling of accidents and near misses, ensuring a quick and effective resolution to minimize potential risks. Job Safety Analysis, or Task-Based Risk Assessment as it is known in the UK, provides a structured approach to identify and mitigate potential hazards associated with specific tasks, ensuring that safety protocols are tailored to the unique challenges posed by each phase of the construction process.
As the world evolves, construction companies must navigate a myriad of changes and challenges. Their ability to do so will be pivotal in advancing their safety initiatives and overall success. Together, these tools help elevate safety standards, reduce accidents and fortify the overall well-being of the workforce as a company grows and changes over the years.