Identifying and Tracking Workplace Hazards Using JSA Software
November 1, 2022
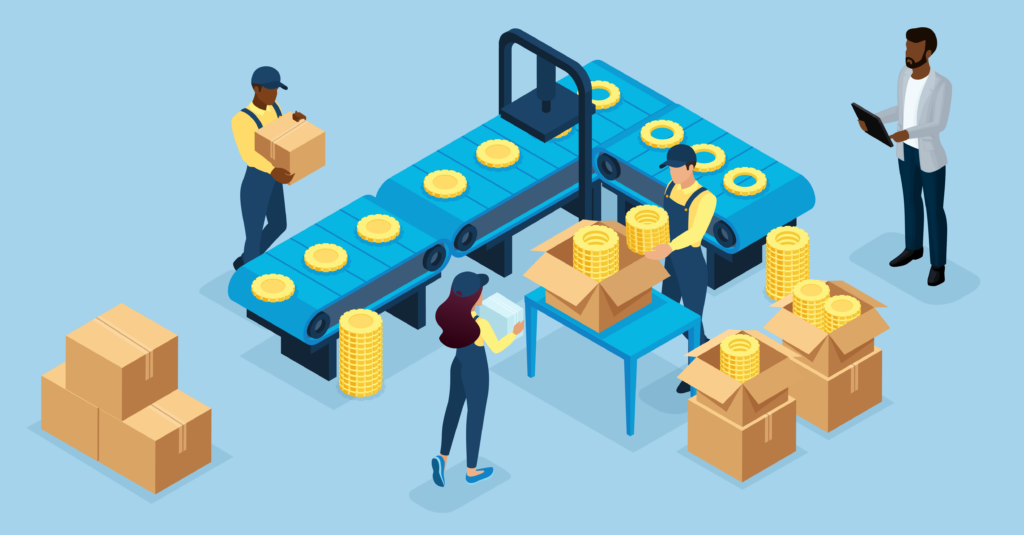
Every seven seconds, a worker is injured on the job in the United States. Many of those injuries could be prevented through readily available tools, such as job safety analysis techniques and software.
Job safety analysis (JSA) is used to define and control hazards associated with certain processes, jobs or procedures. It is a systematic examination and documentation of every task within each job and is used to identify health and safety hazards and the steps required to control each task.
Experts know that one of the most effective ways to identify, track and (hopefully) eliminate work-related injuries is by using job safety analysis, also known as job hazard analysis, to identify hazards.
What’s the Definition of a Hazard?
A hazard is something that holds the potential for harm. In practical terms, a hazard often is associated with a condition or activity that, if left uncontrolled, can result in an injury or illness. Some common hazards include chemical releases or improper storage of chemicals, housekeeping issues that create an unsafe work environment, the potential for electrical shock, uneven or slippery walking surfaces, working at heights, mechanical breakdowns, flying objects, temperature extremes, visibility issues and more. Identifying hazards and eliminating or controlling them as early as possible will help prevent injuries and illnesses.
What is Job Safety Analysis?
Job safety analysis is a tool – likely a template either on paper or on a digital device – that focuses on job tasks as a way to identify hazards before they occur. The process dissects the relationship between the worker, the task, the tools and the work environment. Ideally, after uncontrolled hazards have been identified, safety professionals or production managers take steps to eliminate or reduce them to an acceptable risk level.
Why is Job Safety Analysis Important?
More than a dozen workers are killed at the workplace every day in the United States, according to OSHA and the Bureau of Labor Statistics. You can help prevent workplace injuries and illnesses by looking at your workplace operations, establishing proper job procedures and ensuring that all employees are trained properly. Recent research from Intelex Technologies found that 90 percent of respondents have experienced at least one EHS incident (environmental release, worker injury or illness, property damage, vehicle incident, fire and/or near miss) in the past year. Tracking down and managing the causes of those incidents can drastically reduce workplace-related injuries and illnesses.
What is the Value of a Job Safety Analysis?
Safety professionals can use the findings of a job hazard analysis to eliminate and prevent hazards in their workplaces. This is likely to result in fewer worker injuries and illnesses; safer, more effective work methods; reduced workers’ compensation costs; and increased worker productivity. Job safety analysis also can be a valuable tool for training new employees in the steps required to perform their jobs safely.
Related Content:
- The More You Know (Part 1): The Essentials of Job Safety Analysis – Research shows 275 American workers in 2019 died each day from hazardous working conditions. Completely eliminating harmful incidents on the job is the ideal for every business. Job safety and hazard analysis are essential tools of the trade to getting there.
- The More You Know (Part 2): How Safety Analytics Raise the Bar in Operational Excellence – OSHA estimates a recordable incident has a direct cost of $7,000 and a workplace fatality is $910,000, in addition to indirect costs at three times those amounts. The good news is that many workplace injuries and incidents can be predicted before they happen.
According to our research, 86 percent of EHS professionals surveyed indicated that unless they improve their health and safety culture – and training and communication play a huge role in that undertaking – they will lose skilled workers and top prospects to better-performing competitors.
In addition, one of the best ways to determine and establish efficient and safe work procedures is to conduct a job or work hazard analysis, which is one component of a larger commitment to a safety and health management system and a path to a higher level of maturity in EHS management. Reducing exposure to hazards and eliminating injuries and illnesses is good for business: Our research found that 87 percent of health and safety professionals agree that a high level of maturity in health and safety management can be a key competitive differentiator.
Where Should You Concentrate Your JSA Efforts?
A job safety analysis can be conducted on many jobs in your workplace. Priority should go to the following types of jobs:
- Jobs with the highest injury or illness rates
- Jobs with the potential to cause severe or disabling injuries or illness, even if there is no history of previous incidents
- Jobs in which human error could lead to a severe accident or injury
- Jobs that are new to your operation or have undergone changes in processes and procedures, or jobs that are so complex that written instructions are required.
How can Software Help With JSA?
Job Safety Analysis Software makes it easier to identify and mitigate job hazards in the workplace to effectively reduce worker injuries and asset losses and to increase uptime. Your software should:
- Provide hazard identification and risk assessment: Should use a standard risk methodology – the likelihood of an incident occurring by severity – to identify and resolve hazards associated with individual job tasks, and then communicate the operational risks as acceptable, acceptable with mitigation or unacceptable. You might already have your own risk assessment methodology. If so, seek out a system like Intelex, which allows you to create or upload your own risk assessment methodologies directly into the safety management system.
- Optimize your controls: Should perform parallel residual risk analysis for different control types to identify the most sensible control for the job or task. Should automatically maintain a log of controls that can be used to boost visibility into the need and types of controls and promote audit-readiness.
- Be tailored to your operations: Intelex’s Job Safety Analysis application, like the rest of Intelex, is highly configurable. Add the jobs, hazards and controls that are relevant to your operations and workforce to ensure maximum value and adoption.
What Features Should Your Job Safety Analysis Software Include?
Intelex Job Safety Analysis software allows users to identify, analyze, communicate and reduce the risks associated with any job or task. You should be able to filter and sort jobs by location, business unit, employee(s) involved, job steps, hazards, potential trigger events, potential consequences, consequence severity and much, much more.
- Keep assessments organized and centralized: You should have the ability to log every job safety assessment into the system, which gives company-wide visibility into job history, past risk levels, past steps, past controls and even past owners. This helps ensure your risk levels are always trending in the right direction.
- Leverage JSA information across your safety management software platform: A job safety analysis or job hazard analysis contains a plethora of useful information in and of itself, but it provides the most value when it is considered in other contexts, such as incident management, compliance auditing, training development or enterprise risk assessments. Intelex allows for users to take JSA data out of its silo to maximize its use across the organization.
Ready to see how job safety analysis software can transform your workplace safety? Watch our product demo to explore the features and benefits in action!