Optimize ISO 9001:2015 Compliance with Document Control Software
October 28, 2022
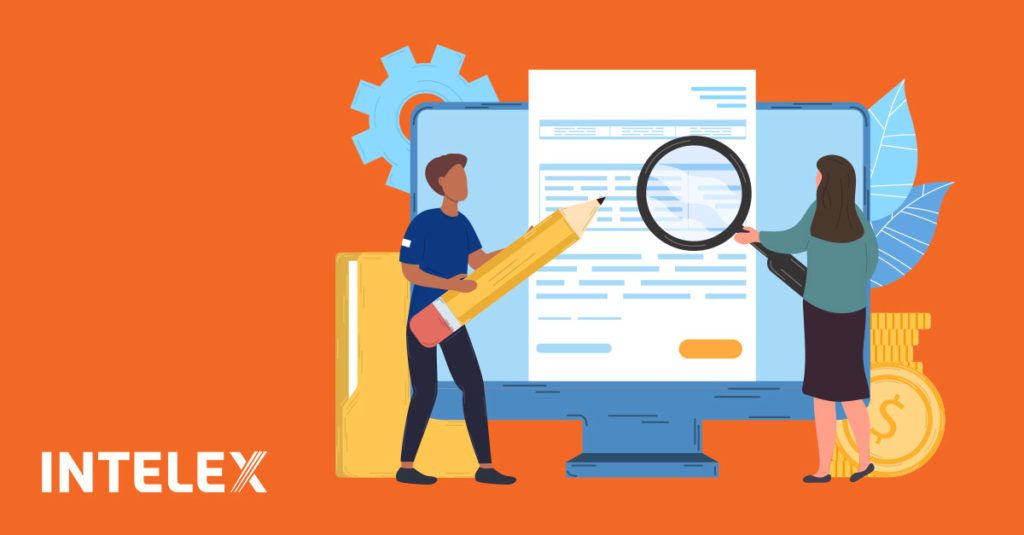
Unlike previous iterations of ISO 9001, ISO 9001:2015 does not prescribe specific approaches to document governance. Instead, it is up to each organization to determine its approach to the maintenance, retention, and disposition of documentation.
ISO 9001:2015 eliminates the distinction between records, processes and manuals by using the category “documented information” to describe all of them. The phrase maintain documented information describes working documentation that requires regular updates, such as procedures and work instructions. The phrase retain documented information refers to document types such as records that provide evidence of past conformity with requirements.
ISO 9001:2015 has requirements for documented information throughout the standard. The table below collects all the references to required documented information.
Clause | Description |
4.3 Scope of the QMS | Describe products and services covered and justify anything the organization decides is out of scope for ISO 9001:2015. |
4.4.2 Operation of QMS processes | Maintain documents that support the operation of the QMS and retain documents that provide confidence and evidence that processes are being carried out correctly. |
5.2.2 Communicating quality policy | Distribute and facilitate interaction with the quality policy. |
6.2.1 Quality objectives | Maintain documentation of the quality objectives and their relevance to the QMS. |
7.1.5.1 Resources | Maintain documentation that provides evidence of the suitability of monitoring and measuring resources for the QMS. |
7.1.5.2 Measurement traceability | Maintain the basis for calibration or verification as documented information when no standards for these activities exist. |
7.2 Competence | Retain documentation as evidence of the competence of all human resources supporting the QMS. |
7.5.1 Documented information | Maintain documentation required by ISO 9001:2015 for the effectives of the QMS. |
7.5.2 Creating and updating | Ensure that all documentation has appropriate identification, description, format, and review policies. |
7.5.3 Control of documented information | Ensure documentation is available for use and adequately protected by effective information governance policies. |
Clause | Description |
8.1 Operational planning and control | Provide governance of documentation to demonstrate that processes, products, and services have met all requirements and expectations. |
8.2.3.2 Requirements for products and services | Retain documentation to demonstrate reviews of the requirements for products and services and of any new or additional requirements. |
8.2.4 Changes to requirements for products and services | Amend documentation to reflect changes to the requirements for products and services. |
8.3.3 Design and development inputs | Retain documentation relating to design and development inputs. |
8.3.4 Design and development controls | Retain documentation of the controls relating to the design and development process. |
8.3.5 Design and development outputs | Retain documentation relating to the design and development of outputs. |
8.3.6 Design and development changes | Retain documentation relating to any changes to the design and development controls. |
8.4.1 Control of external processes, products and services | Retain documentation relating to externally provided processes, products, and services. |
8.5.1 Control of production and service provision | Ensure the availability of documentation that defines the characteristics of the product, services, and activities, as well as the results of each. |
8.5.2 Identification and traceability | Maintain documentation to ensure traceability of outputs and conformity of products and services. |
8.5.3 Property belonging to customers or external providers | Retain documentation relating to any incident involving customer or external provider property while in the care of the organization. |
8.5.6 Control of changes | Retain documentation describing the results of the review of changes. |
8.6 Release of products and services | Retain documentation of the conformity of product and service release and the traceability of release authorization. |
8.7.2 Control of nonconforming outputs | Retain documentation relating to nonconforming outputs. |
9.1.1 Monitoring, measurement, analysis and evaluation | Retain documentation relating to the monitoring, measurement, analysis, and evaluation of the QMS. |
9.2.2 Internal audit | Retain documentation relating to audits of the QMS. |
9.3.3 Management review outputs | Retain documentation of results of management reviews of required changes and improvements. |
10.2.2 Nonconformity and corrective action | Retain documentation on nonconformities and corrective actions taken. |
Intelex can be used not only to support ISO 9001:2015, but also the Baldrige Excellence Framework. ISO 9001:2015 and Baldrige share several common elements, including a focus on achieving quality excellence for products and services that meet regulatory requirements.
Baldrige complements ISO 9001:2015 by moving beyond compliance and helping organizations achieve operational excellence and continuous improvement. Intelex can play an important role in achieving this strategic goal. The table below shows some of the common features between ISO 9001:2015 and Baldrige, as well as the Intelex applications that can support them.
The Baldrige Excellence Framework contains several elements that are not considered in ISO 9001:2015. These elements are critical to the complementary relationship between ISO 9001:2015 and Baldrige that will allow organizations to achieve operational excellence. Below is a description of these unique elements and how Intelex can help you meet the requirements found in ISO 9001:2015 and Baldrige.
How Intelex Supports ISO 9001:2015 and Baldrige Excellence Framework
ISO 9001:2015 | Baldrige Excellence Framework | Intelex App | ||
Clause | Description | Clause | Description | |
4. Context of the organization | Understand the internal and external issues that impact strategic direction. | Organizational profile | Consider requirements and expectations of stakeholders. Understand organizational mission, vision, values and core competencies for strategic planning and innovation. | Bulletins Document Control Training Management Nonconformance (NCR) Customer Complaints Audits/Supplier Audits (with Checklists) Management Review (MR) Meetings Management Action Plans Risk Assessments Monitoring and Measurement |
6. Operations | Design, manage and improve key products and work processes. Create processes for managing innovation. | |||
4. Measurement, analysis and knowledge management | Consider measures to improve operational performance. Collect data from multiple sources and share best practices throughout the organization. | |||
5. Leadership | Understand the role of leadership in supporting the QMS and engaging the people in the organization. Demonstrate commitment to customer satisfaction. | 1. Leadership | Consider the role of leadership in creating an environment for success and communicating with the workforce. Create opportunities for intelligent risk and innovation. Communicate with and engage key customers and stakeholders in and beyond the organization. | Bulletins Document Control |
3. Customers | Listen to and engage with customers to develop a long-term relationship that exceeds customer expectations. Determine methods of listening to and engaging with customers to achieve customer satisfaction. | |||
6. Planning | Address risks, opportunities and objectives. | 2. Strategy | Understand the development and implementation of strategy. Understand strategy development process and key strategic objectives. | Action Plans Document Control Management of Change (MoC) |
7. Resources | Consider work environment, monitoring, organizational knowledge and workforce competence. | 5. Workforce | Build and engage an effective and capable workforce. | Document Control Monitoring & Measurement Training Management Risk Management Bulletins EHS applications Nonconformance (NCR) Customer Complaints Audits/Supplier Audits (with Checklists) Management Review (MR) (Meetings Management, Action Plans) Risk Assessments Dashboards Supplier Relationship Management Product Management Shipping, Receiving & Inspections Management of Change (MoC) |
4. Measurement, analysis and knowledge management | Consider measures to improve operational performance. Collect data from multiple sources and share best practices throughout the organization. | |||
6. Operations | Design, manage and improve key products and work processes. Create processes for managing innovation. | |||
8. Operations | Monitor operations and internal and external information. | |||
3. Customers | Listen to and engage with customers to develop a long-term relationship that exceeds customer expectations. Determine methods of listening to and engaging with customers to achieve customer satisfaction. | |||
9. Performance evaluation | Manage and evaluate the QMS for operational performance and customer satisfaction. | 4. Measurement, analysis and knowledge management | Consider measures to improve operational performance. Collect data from multiple sources and share best practices throughout the organization. | Document Control Monitoring & Measurement Training Management Risk Management Bulletins EHS applications Nonconformance (NCR) Customer Complaints Audits/Supplier Audits (with Checklists) Management Review (MR) (Meetings Management, Action Plans) Risk Assessments Dashboards Supplier Relationship Management Product Management Shipping, Receiving & Inspections Management of Change (MoC) |
3. Customers | Listen to and engage with customers to develop a long-term relationship that exceeds customer expectations. Determine methods of listening to and engaging with customers to achieve customer satisfaction. | |||
1. Leadership | Consider the role of leadership in creating an environment for success and communicating with the workforce. Create opportunities for intelligent risk and innovation. Communicate with and engage key customers and stakeholders in and beyond the organization. | |||
7. Results | Analyze results for product performance, customer-focused performance, workforce performance and leadership performance. | |||
10. Improvement | Address nonconformity, corrective action and continuous improvement. | 6. Operations | Design, manage and improve key products and work processes. Create processes for managing innovation. | SRI (Shipping, Receiving, and Inspections) Nonconformance (NCR) Corrective Action Reporting Root Cause Analysis Action Plans |
4. Measurement, analysis and knowledge management | Consider measures to improve operational performance. Collect data from multiple sources and share best practices throughout the organization. | |||
Baldrige Scoring System | Apply Baldrige rubric for assessment of organizational performance maturity. |
In conclusion, ISO 9001:2015 provides flexibility in documentation management, allowing organizations to tailor their approaches to maintaining and retaining essential information. This adaptability, combined with Intelex’s software solutions, enables companies to achieve both compliance and operational excellence.
For further insights into optimizing your documentation and aligning with standards like ISO 9001:2015 and the Baldrige Excellence Framework, watch the Intelex Document Control Software product demo today. Discover how this solution can elevate your quality management approach and drive continuous improvement.