The Five Things You Need To Know About Incident Management and Reporting
September 27, 2022
8 minute read
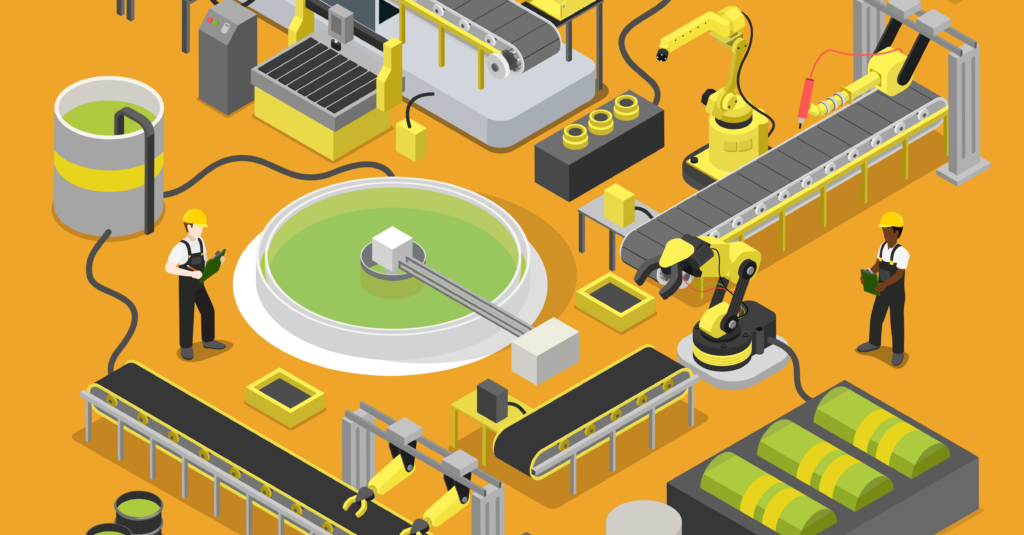
Every day, SUEZ North America’s 2,900 employees manage 1 billion gallons of water and wastewater—and the safety risks that come with it. That’s why effective incident management and reporting is critical to keeping operations safe and compliant.
From towering tanks to aging infrastructure, they oversee more than 4,000 facilities, many requiring work 100 feet in the air or in high-hazard environments.
But despite the scale and complexity of their operations, SUEZ was still managing incident data and safety reporting through spreadsheets and paper forms.
“We couldn’t keep track of the paperwork. We had five different versions of everything,” said Kanwer Khan, Vice President, Environmental Compliance, Health, Security and Safety for SUEZ North America.
It wasn’t just inefficient — it was risky. And as operations grew, so did the urgency to fix it.
SUEZ needed a system that could keep up with the pace of their work, support their people, and give leaders visibility into what was really happening on the ground.
The path to improving incident management and reporting often starts with a mindset shift—one grounded in these five essential principles.
Table of Contents
Disasters are rarely caused by a single event
Safety and environmental disasters almost never happen because of one failure. They’re often the result of a cascade of events — organizational failures, poor planning, unclear procedures, and missed warning signs. This underscores the importance of having a strong incident management and reporting process in place to identify root causes early.
“Rarely does a single event cause a tragedy. It’s a cascade of events … there were problems lying in wait,” said Gordon Graham, risk expert and former California Highway Patrol officer.
Consider the Deepwater Horizon disaster. A technical failure triggered the explosion, but investigations revealed much deeper issues:
- Emphasis on speed and cost over safety.
- Poor communication between internal and third-party contractors.
- Disorganized safety manuals and inconsistent procedures.
- Under-reporting of unsafe conditions due to fear of reprisal.
The takeaway: Incident management must uncover and address systemic weaknesses — not just symptoms.
Any incident with a potential for a serious loss points out the same deficiencies in the SMS: the causal factors that make the incident occur. The severity of the actual loss in each event often is a matter of chance.
You must define what counts as an “incident”
It’s not just about reportable injuries.
An “incident” can include:
- Property damage
- Environmental release (either contained onsite or spreading externally)
- Security breaches
- Near misses
- “No harm” events that could have been worse
- Harm to third parties (e.g., a hospital patient injured due to malfunctioning equipment)
- Product damage
The severity of an incident’s outcome is often just a matter of chance.
Even when nothing goes wrong, the presence of a hazard signals deeper issues. That’s why organizations should investigate every incident and near miss, especially those with high loss potential using these three steps:
- Investigate every incident and near miss to evaluate loss potential.
- Conduct in-depth reviews of high-potential events, even if no harm occurred.
- Define what types of loss and potential loss are most significant to your organization’s people, resources, and reputation.
Incident reports are more than a compliance exercise
Timely, accurate incident reports are one of the most powerful tools in an EHS professional’s toolkit.
They serve as the foundation for:
- Root cause analysis
- Corrective and preventative actions
- Regulatory reporting
- Pattern and trend identification
- Leadership awareness and accountability
A good report should:
- Be fact-based and objective (not opinionated)
- Include clear timelines, locations, witness statements, and diagrams
- Be as complete and visual as possible—with photos, sketches, and documentation
- Include sign-off from those involved, including victims, witnesses, and managers
These reports help uncover hidden risks and ensure that action is taken—not just noted.
Want to see how Intelex makes incident reporting easy?
Watch our Incident Reporting Software demo to see how
you can simplify reporting, improve investigations, and reduce safety risks.
Regulatory requirements are the floor, not the ceiling
Employers with more than 10 employees are required by OSHA to record serious work-related injuries and illnesses, including:
- Fatalities
- Injuries resulting in days away from work
- Medical treatment beyond first aid
- Diagnosed cases of cancer, chronic illness, or broken bones.
But just meeting compliance isn’t enough.
To truly strengthen your safety program, you should also capture:
- Near misses
- Unsafe conditions
- “No harm” events
- Adverse outcomes related to equipment or medication (in healthcare settings for example)
Doing so helps build a culture of safety—not just compliance.
How software changes incident management and reporting
The creation of incident reports, which are a vital component of any incident management system, does not have to be difficult or confusing.
Safety Incident Management software empowers you to capture, track, investigate, analyze and report on all incidents and near-misses, including injuries and illnesses, spills, property damage and vehicle incidents.
The biggest challenges in incident management and reporting aren’t conceptual — they’re tactical, according to Trevor Bronson, Director of Portfolio Strategy at Intelex and a former EHS practitioner at Tesla and PPL.
“Without a proper tool, resources will be wasted gathering data, entering it in multiple locations, hunting down data for reports, and following up on CAPAs,” said Bronson.
Here’s an example of what Trevor is talking about.
Incident management example: Manual vs. software
Process Step | Manual Approach | Modern Software Approach |
---|---|---|
Recording the incident | Manual forms, redundant data entry | Configurable, mobile-responsive forms tied to incident type; auto-alerts notify stakeholders |
Investigating the incident | Disorganized process, hard-to-track timelines, poor document control | Dedicated workflows, centralized document control, media attachments for on-site accuracy |
Follow-up and auditing | Low visibility into status of actions; hard to identify trends or confirm effectiveness | Real-time tracking of action items, trend dashboards, integrated audit tools |
Corrective and preventative actions | Manual task lists, missed deadlines, no escalation process | Tasks assigned within workflows, automated reminders/escalations, completion tracking |
Internal/External Reporting | Time-consuming data collection, inconsistent formats, no scheduling | One-click reporting, scheduled internal reports, customizable report templates |
Analyzing root causes | Siloed data, poor data quality, difficult RCA and BI integration | Embedded analytics, custom dashboards, integrated RCA tools and BI platforms |
Role-based visibility | Everyone sees the same incomplete data or relies on email updates | Executives see KPIs, supervisors see site performance, frontline workers report from the field |
SUEZ reduced DART by 24%—here’s what changed
Since implementing Intelex’s Safety Incident Management Software in 2015, SUEZ North America has made significant strides in improving how it captures, tracks, and acts on safety data. The shift from paper-based processes to a centralized, digital system has contributed to stronger engagement, better data quality, and meaningful safety outcomes.
The results speak for themselves:
- 10x increase in employees reporting incidents thanks to increased employee engagement.
- 24% reduction in Days Away Restricted or Transferred (DART) rate — from 2.14 in 2014 to 1.63 in 2018.
- 41% reduction in Workers’ Compensation Experience Modification Rate (EMR) — from 1.05 in 2009 to 0.62.
Operating hundreds of facilities across North America, SUEZ must manage aging infrastructure, varied safety cultures, and frontline employees who often work in high-risk environments. Accurate incident reporting and accessible data are critical for keeping workers safe and operations running smoothly.
Today, every employee has access to the Intelex platform, and most of the workforce can report hazards directly from smart devices. This accessibility, combined with structured workflows and centralized reporting, has helped embed safety more deeply into daily operations.
Now, SUEZ utilizes Intelex’s EHS Incident Reporting Software for capturing, reporting, analyzing and correcting hazards. Every employee has access to the software and most of the workforce has smart devices through which they can report hazards.
“Intelex has been a life saver for us,” said Khan. “I don’t know what we’d do without it.”
Incident management and reporting demo
Ready to see how Intelex can help you improve incident reporting in your organization? Watch our incident reporting software demo.
You’ll learn how to:
- Capture and investigate incidents efficiently
- Assign and track corrective actions
- Analyze trends to prevent future harm
- Make safety data accessible to everyone—from frontline workers to executives
Watch the demo and discover what smarter incident reporting could do for your team.