Improving Workplace Safety: How to Engage Employees as Stakeholders
April 19, 2022
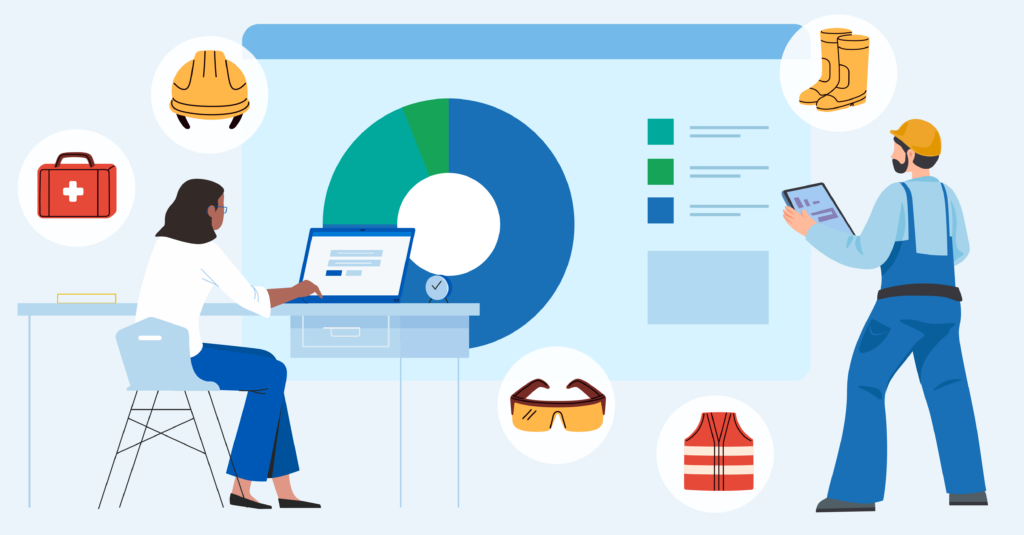
Engaging employees as legitimate stakeholders in workplace health and safety is crucial for building a robust safety culture. This approach involves listening, collaboration and treating employees as equal partners in developing and implementing safety programs. When the entire workplace is involved, organizations can significantly enhance their safety outcomes, limit losses and drive performance. As true stakeholders in safety, they become more invested in the well-being of themselves and their colleagues, leading to a safer and more productive work environment.
This article explores various strategies and best practices for engaging employees in workplace safety, drawing on real-world examples and expert insights. From encouraging safety leadership roles among employees to building strong labor/management relationships, the following sections will provide practical guidance on how to create a collaborative and effective safety culture within your organization.
Relationship Building is Key to Workplace Safety
As a health and safety “staff of one,” Scott Gaddis recognized that his effectiveness at Kimberly-Clark would depend on his ability to build strong relationships across the organization. To develop a culture of safety, Gaddis actively engaged with various working crews, identifying individuals eager to enhance their safety skills and job qualifications.
As part of their condition of employment, workers at Kimberley-Clark’s production facility needed to embrace two champion areas as a prerequisite to advancing their careers. One champion area focused on job specialization and the other required deeper learning about health and safety, quality, maintenance, etc.
“If you were a champion of paper manufacturing, that was your first priority,” Gaddis says. “Your second champion area might have been to work with me on safety and health. Every employee already had strong safety knowledge through training and skills development. Then I had a crew of 35 workers that I worked with to have an even deeper capability in safety.
“I would meet with those people, train them and build their knowledge. I would teach them things like lockout/tagout, confined space, how to drive a fork truck, how to inspect the fork truck – everything I knew. I was transferring that knowledge to them and trying to build mini versions of myself.”
Someone might be designated as the machine-guarding expert or champion on a work crew and would refine and develop their health and safety skills to perform inspections on that equipment. Eventually, most employees in a facility of more than 500 people were clamoring to become champions in various aspects of operations.
“I was trying to just keep skin in the game and wanted them to be a part of this,” Gaddis says, explaining it was challenging to instruct so many people on safety skills. But the effort was vital in creating a strong safety culture and encouraging employees as stakeholders in health and safety.
“Everybody was able to take accountability. That facility was the best one at Kimberly Clark… and it’s just been perking along for the last 30 years now.”
Overcoming Labor/Management Barriers
The success of safety programs and willingness of employees to become stakeholders might also depend on labor/management relations and how comfortable workers feel about raising health and safety risks, says Jordan Barab, a former director of health and safety for the American Federation of State, County and Municipal Employees (AFSCME) and former deputy assistant secretary for the U.S. Occupational Safety and Health Administration (OSHA).
“If you have a situation where (employees) are not listened to or, even worse, managers are disciplining or retaliating against them for raising issues, then obviously you’ve got a problem bigger than any health and safety expert is going to be able to address,” he says. “So, it’s necessary for health and safety professionals to understand the power relationships in the workplace and to listen to workers.”
In workplaces where a collective bargaining agreement exists, contract language sets the parameters and rules each side must follow regarding workplace safety, but management must also earn the trust of employees, Barab says, adding, “Good employers are sincerely interested in working with their employees as partners and listening to them.”

Still, power relationships can sometimes inhibit or put a roadblock in the way of an employee’s ability to step up as a stakeholder in health and safety.
“If a worker is not listened to regarding a health and safety concern, then that’s obviously going to have kind of a chilling effect on the labor/management relationship when it comes to health and safety,” Barab says. “You need to deal with the labor/management issues and the power relationships in the workplace before you can actually fix health and safety problems.”
Barab admits getting the attention of company leadership sometimes requires filing workplace safety complaints with OSHA.
“We didn’t have many strikes over health and safety issues, but by using some kind of labor action – by going to the press or whatever – we could put pressure on them,” he says.
Encouraging employees to be legitimate stakeholders in workplace safety is really a matter of listening, being open to and dealing with employees as equal partners in developing and implementing programs.
Setting the Tone for a Safety Culture Through Leadership Commitment
While employees are important stakeholders in their safety, leadership should also demonstrate a commitment to safety as a core value. When leaders at all levels prioritize safety as a core value, it sends a clear expectation to the employees that they need to be involved in their safety program. This top-down approach ensures that safety is integrated into every aspect of the organization, from strategic planning to daily operations.
This means that senior executives and managers need to visibly and consistently demonstrate their commitment to safety. Actions speak louder than words; thus, leaders should actively participate in safety training, regularly communicate the importance of safety and ensure that adequate resources and tools are allocated to safety programs.
By making safety a central element of the organization’s mission and values, leaders create an environment where employees feel supported and motivated to prioritize their own safety and that of their colleagues. This commitment from the top helps to foster a culture where safety is seen not just as a compliance requirement but as a fundamental aspect of the company’s operations and ethos.
Employee Engagement and Technology Integration
Leveraging EHS software, such as Intelex, can significantly improve safety management processes. These tools provide solutions for tracking, reporting and analyzing safety data, crucial for compliance and continuous improvement.
Real-Time Monitoring
Real-time monitoring tools offer immediate insights into safety conditions and incidents, allowing swift responses to risks. These tools enhance the accuracy of incident reporting and help organizations gain a precise understanding of root causes.
Incident Management and Behavior-Based Safety
Intelex software includes modules for Near Miss Reporting, Inspections, Incident Reporting, Behavior-Based Safety, Observations and Mobile accessibility. These modules streamline reporting, facilitate root cause analysis and promote safer practices. Mobile access ensures data can be collected and accessed from anywhere, enhancing system responsiveness.
Employee Interaction with EHS Software
EHS software empowers employees to report observations, near misses and incidents in real-time via mobile devices. This approach optimizes data collection and generates high-level insights. Employees can submit detailed reports, including photos and videos, ensuring quick and accurate documentation of safety concerns.
This interaction creates a culture of transparency and continuous improvement. The collected data helps identify trends and develop targeted interventions, providing leadership with insights for informed decision-making.
Continuous Improvement
EHS software supports continuous improvement through regular audits, inspections and feedback loops. Organizations can use this data to identify areas for improvement, set safety goals and track progress. Continuous learning from past incidents helps address potential risks proactively.
The Path Forward to a Robust Safety Culture
Engaging employees as legitimate stakeholders in workplace health and safety is more than a compliance obligation—it’s a strategic approach for creating a strong safety culture. By listening to employees, collaborating with them and treating them as equal partners in safety initiatives, organizations can significantly enhance their safety outcomes, minimize losses and boost overall performance.
When employees feel valued and listened to, they are more likely to take ownership of safety and contribute positively to their work environment. Equally important, when leaders at all levels prioritize safety and actively participate in safety programs, it sends a strong message that safety is a core value of the organization.
Ultimately, creating a collaborative and effective safety culture requires a genuine commitment to continuous learning and improvement. Through technology, open communication and strong relationships between management and employees, organizations can create a safer, more productive work environment where everyone is invested in the well-being of themselves and their colleagues.