Digging In to Improve Mining Safety: Challenges and Software Solutions
June 1, 2021
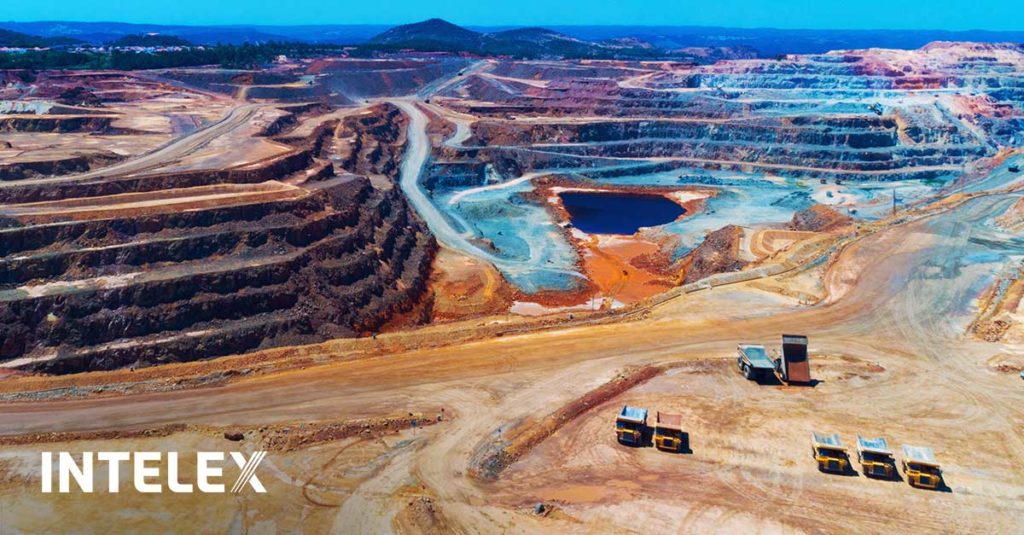
Mining safety is on an upswing in recent years. According to the Mine Safety and Health Administration (MSHA), approximately 230,000 miners work across 11,500 metal/nonmetal mines in the U.S., while 64,000 work in the nation’s 1,000 coal mines. The mining sector employs 3.7 million+ workers worldwide and is structured according to the substance being mined, the type of excavation taking place (either surface mining or underground mining) and by the mine’s lifecycle/development phase. Environmental and safety concerns/priorities change based on the substance being mined, the type of excavation and the phase of the lifecycle.
In 2020, there were 29 mining fatalities, making it the sixth consecutive year that mining fatalities were below 30. Among those fatalities, five occurred in coal mines, a historic low.
After a two-year increase in 2017 and 2018 when about half of all deaths resulted from powered haulage accidents, such as vehicle-on-vehicle collisions, failure to use a functioning seat belt and conveyor belt accidents, MSHA responded with a multifaceted education campaign and initiated rule-making. By 2020, powered haulage deaths dropped to 21 percent. The Year 2020 also marked the first year in MSHA’s history with no seatbelt-related deaths, and conveyor-related deaths dropped from four in 2017 to one in 2020.
As required, MSHA inspected all underground mines at least four times per year and surface mines at least twice per year in 2020, in a year when 15 percent of inspectors self-identified as high-risk for the coronavirus under CDC guidelines. Between March 1, 2020, and Dec. 31, 2020, MSHA issued 195 citations for sanitary conditions that could have contributed to coronavirus.
The mining industry achieved its highest compliance with MSHA’s health standards, which protect the long-term health of miners. The year 2020 saw all-time-low average concentrations of respirable dust and respirable quartz in underground coal mines, as well as exposure to dust and quartz for miners at highest risk of overexposure to respirable dust.
Mining Safety Solutions
Challenge: Managing permits—Requirements for permitting mines can be extensive and complicated, particularly for large mines. In some cases, it can be a multi-year process, involving dozens of individual permits.
Solution: Permits Management Software
Challenge: Waste removal/water management—Although covered under permits, it is useful to understand that mine waste can pose serious environmental risk. Major breaches of tailings ponds have made headlines. Water at mine sites is frequently monitored, and in extreme cases, water treatment sludge may be classified as hazardous waste and require special handling and disposal.
Solutions: Water Quality Management Software, Waste Management Software
Challenge: Reputational damage—While modern practices have improved safety and decreased fatalities and have diminished environmental impact, the industry still suffers from the reputation of being a dirty and unsafe industry. Failures in waste management continue to draw criticism from local communities and contributes to the negative public perception.
Solution: Environmental, Social and Governance (ESG) Software
Challenge Stakeholder management—The environmental impact of mining often puts mining companies in the position of needing to address and manage the concerns of Indigenous and environmental groups in a formalized way.
Solutions: Communication Management Software, Environmental, Social and Governance (ESG) Software
Challenge: Contract worker safety—The mining industry relies on contract workers, and these contractors typically are overrepresented in fatal mining accidents. Ensuring that contractors receive appropriate training is a challenge for mine operators.
Solutions: Training Management Software, Bulletins
Challenge: Aging workforce—Like many other industries, a significant portion of the mining workforce is reaching retirement age. Training needs will increase for new, inexperienced workers.
Solutions: Training Management Software, Bulletins, Behavior-Based Safety Software
Conclusion
Mining safety has come a long way, with fatalities dropping and compliance improving, but challenges remain. By adopting modern software solutions for permits, waste management, ESG, training and contractor safety, mine operators can address pain points and continue to enhance safety standards. As the industry evolves, focusing on proactive safety measures and leveraging technology will be key to ensuring a safer and more sustainable future for miners worldwide.
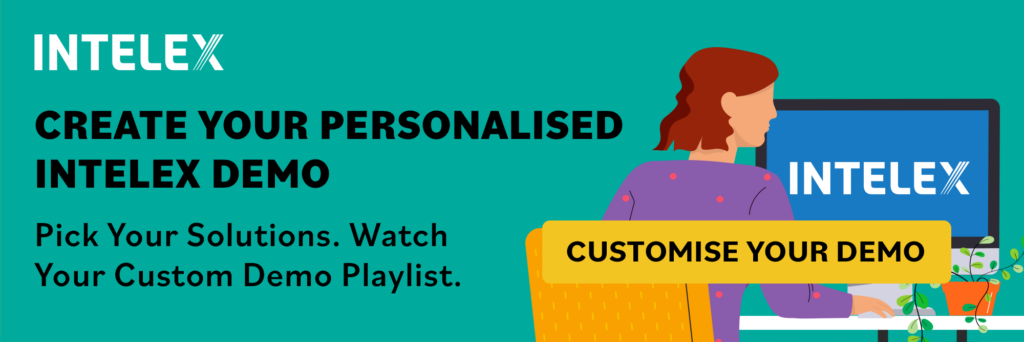