Bridging the Gap in Worker Safety with Mobile Technology
August 13, 2019
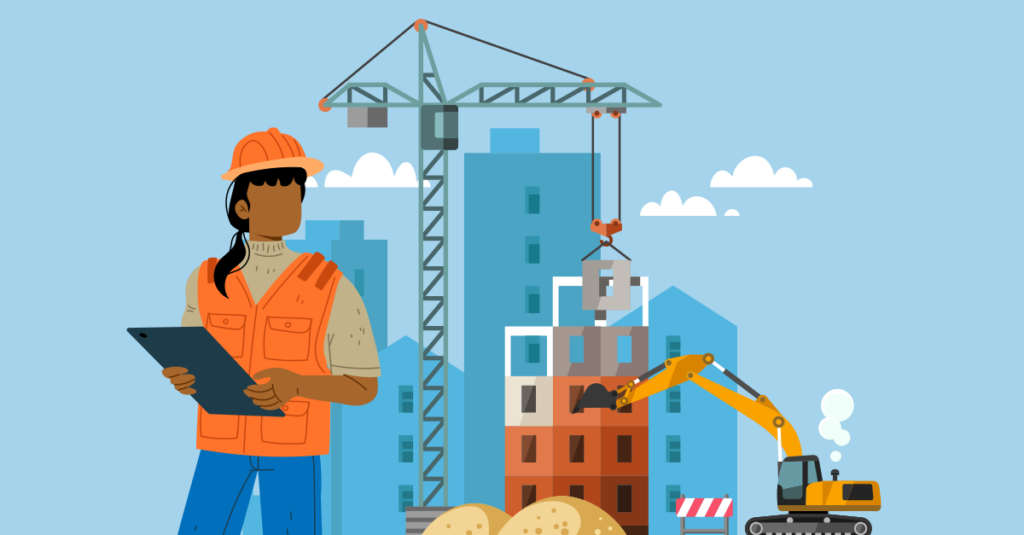
Successful EHS management systems identify, manage and eliminate workplace hazards before they cause injuries and illnesses for employees, damage assets and create environmental issues.
Mobile apps and software systems are providing workers with immediate access to safety resources, enhancing the effectiveness of Environmental Health and Safety (EHS) management systems.
These systems are crucial for identifying and mitigating workplace hazards to prevent employee injuries, illnesses, and environmental issues.
Want to see how top EHS leaders around the world are improving safety culture with mobile tech? Read the 10 findings in our latest report.
14 U.S. Workers Killed Each Day
According to the U.S. Bureau of Labor Statistics, the rate of worker deaths and reported injuries in the United States has decreased by more than 60 percent in the past four decades since the Occupational Safety and Health (OSH) Act was passed. However, every year, more than 5,000 workers are killed on the job (a rate of 14 per day), and more than 3.6 million suffer a serious job-related injury or illness.
Serious job-related injuries or illnesses don’t just hurt workers and their families. Research from Liberty Mutual places a dollar amount on the cost of serious, nonfatal workplace injuries to American businesses of $1 billion per week in direct U.S. workers’ compensation costs. Implementing an EHS management system, however, can improve small- and medium-sized businesses’ safety and health performance, save money and improve competitiveness.
Safety and health programs help businesses:
- Prevent workplace injuries and illnesses
- Improve compliance with laws and regulations
- Reduce costs, including significant reductions in workers’ compensation premiums
- Engage workers
- Enhance social responsibility goals
- Increase productivity and enhance overall business operations
Scott Gaddis, Vice President, Safety and Health at Intelex Technologies, has created the checklist “10 Steps to Take Your EHS Management System from Good To Great,” to help you evolve your EHS Management System.
Recommended EHS Practices
OSHA has recently updated the Guidelines for Safety and Health Programs it first released 30 years ago to reflect changes in the economy, workplaces and evolving safety and health issues. The new Recommended Practices have been well received by a wide variety of stakeholders and are designed to be used in a wide variety of small- and medium-sized business settings. The Recommended Practices present a step-by-step approach to implementing a safety and health program, built around seven core elements that make up a successful program.
These practices include:
- Management Leadership
- Worker Participation
- Hazard Identification and Assessment
- Hazard Prevention and Control
- Education and Training
- Program Evaluation and Improvement
- Communication and Coordination for Host Employers, Contractors and Staffing Agencies
Here are some examples of these practices in action and some resources to help you achieve EHS management success:
1. Management Leadership
The simple model, “People, Public Trust and Profit” can be used to explain to senior management that EHS not only responds to the human case for health and safety but also the business case. Once they understand this, they are more likely to engage in the EHS process. The key to this concept is the importance of expressing typical EHS outputs as critical business outputs such as cost, quality and production and creating the understanding that EHS can create a competitive advantage.
In the webinar, “People, Public Trust and Profit: Driving EHS Excellence and Competitive Advantage,” Dr. Richard D. Fulwiler, ScD, CIH, FAIHA, president, Transformational Leadership Associates, presents actual examples for expressing critical EHS metrics as critical business KPIs. The webinar also demonstrates how an effective EHS software platform can augment these efforts by providing a means for EHS teams to collect, analyze, translate, and communicate key metrics and KPIs both internally and externally.
2. Worker Participation
Suez operates water utilities and provides water and wastewater services to municipalities across the United States. Every day, the Paramus, N.J.-based company provides close to 1 billion gallons of drinking water and treats 1.2 billion gallons of wastewater. Suez also provides long-term maintenance services to over 5,000 elevated and ground water storage tanks. It’s often dangerous work. Employees, for instance, spend 1.2 million work hours a year maintaining water storage tanks at elevations of 100 feet or more. One small error at such heights can be fatal. Worker safety, therefore, is a paramount concern.
When Suez takes over the operation of a client’s sewer and wastewater plant, it often inherits a poor safety culture where old, and usually sub-optimal, processes are ingrained in the way workers operate. To change such thinking, the company will do things such as improving the lighting, applying a fresh coat of white paint everywhere, trimming hedges and providing all workers with a bag of safety-related “goodies,” like new safety shoes, gloves and goggles. Suez views modern technology as being a key element in this effort to promote workplace safety.
Suez chose Intelex’s EHS Incident Reporting and Management software as the platform to make that happen. As more employees have come to realize how much easier it is to enter incidents and other health and safety information with the platform, usage has grown steadily from “only a handful” of sites when it was first deployed, says Kanwer Khan, Vice-President, Environmental Compliance, Health, Security and Safety for Suez, to over 120 today. In the first year, 400 incidents were recorded, a figure that rose to 1,800 in the second year. By the fourth year of using Intelex, 4,000 incidents were reported, a figure that has now stabilized.
3. Hazard Identification and Assessment
Gold mining company Agnico Eagle Mines has been recovering precious metals since the days of sock-hops and Elvis Presley – 1957, to be exact. Headquartered in Ontario, Canada, the firm today operates eight mines across Canada, Finland and Mexico. It also carries out mining exploration and development activities in these countries, along with the United States and Sweden.
With 2016 annual revenues of $2.1 billion (CDN), Agnico Eagle is one of the largest goldminers in the world, employing approximately 8,400 fulltime and contract workers. In 2010, the company recognized a need to improve environmental health and safety (EHS). It was using paper-based spreadsheets to track incidents, inspections and other critical activities and had no real-time capabilities to act on data. EHS staff at Agnico also needed to quickly get data in the hands of executives to speed up EHS project approvals. And, with locations throughout the world, a tool that could accommodate multiple languages – particularly Finnish – was a must.
Good data helps Agnico health and safety leaders identify and assess hazards and gain executive approval for safety initiatives. These can include buying new and safer equipment, changing a procedure or stopping a hazardous activity. “If you are presenting a proposal to executives, it’s much easier if you have data to back it up,” says Louise Grondin, SVP Environment, Sustainable Development and People at Agnico Eagle. “Looking at the number of incidents through the Intelex dashboards helps us make our case (to management) for new equipment, or a change in procedure, or to stop an activity that is too risky.”
Discover how Agnico Eagle has cut its accident rate by 75 percent.
4. Hazard Prevention and Control
Coeur Mining uses Industrial Internet of Things (IIOT) devices integrated with safety management software to prevent exposure to hazards, increase efficiency, reduce silos and barriers, and create a system that supports business success.
Everything at Coeur Mining is integrated – wearables, fatigue monitors, incident reports, audits, drones and contractor supply chain data – and has created one ecosystem of high-quality data that can be used to make educated decisions and share knowledge cross-functionally among Coeur’s 2,127 employees and 859 contractors at five precious metals mining sites in the United States, Canada and Mexico. The incorporation of all technology sources into Intelex’s integrated management system platform is a key differentiator for Coeur Mining’s EHSQ program.
After all, says Adam Gregor, Coeur Mining’s director of Health, Safety and Loss Control, “Technology has to generate value for a company,” and Intelex’s platform and integrated software solutions has helped contribute to a 75 percent reduction in injury rates and a 68 percent reduction in Total Reportable Injury Frequency Rate (TRIFR) since 2012. The program continues to evolve: From 2017 to 2018 alone, Coeur Mining realized a 70 percent reduction in significant spills, and TRFIR dropped another 25 percent.
Coeur Mining uses the findings of audits and exposure reviews to understand where employees have the greatest exposure, then applies technology to reduce that exposure.
5. Education and Training
When Billy Powell, regional director of Health and Safety – North America, started at Smith & Nephew Memphis, the total recordable rate was 1.50. By the close of the 2018 campaign, they were at a .23. This list of critical EHS Management Systems elements, which closely echoes the one supported by OSHA, has helped Smith & Nephew achieve EHS success:
- Make sure there is management commitment.
- Have safety programs policies and procedures in place so people know what’s expected of them.
- Have a process in place to hold people accountable at all levels.
- Make sure employee involvement, empowerment and engagement is an active piece of process.
- Ensure you have good hazard identification and control in place.
- Good incident and accident investigation is a foundation of a safety management program.
- Educate and train your workforce.
- Continually driving towards improvement.
Of employee engagement and training, Powell says: “There’s so many professionals out there in the EHS environment who are struggling because we don’t balance the technical piece with the behavior piece, which highlights employee involvement, empowerment and engagement. If you don’t balance the two and all you have is the technical piece and not the behavioral piece, you’ll never reach that pinnacle point of safety success.
6. Program Evaluation and Improvement
Demonstrating performance of environment, health, and safety (EHS) initiatives is a challenge. There are the obvious legal compliance and established safety policy obligations, but to truly optimize an EHS management program, there also must be a management-led culture of a commitment to safety, inclusive and open communication among employees, and demonstrated continuous improvement of risk management.
The purpose of ISO 45001, the Occupational Health and Safety Management Standard published by the International Standards Organization (ISO), seeks to provide employers of all sizes worldwide a tool that will enable them to proactively identify and manage EHS risks and specifically evaluate the performance of EHS programs.
Although ISO 45001 is an effective way of enhancing EHS performance, it can be a cumbersome task to fulfill its requirements. This checklist will audit your conformance with the evaluation components in clause 9 of the standard. Even if you are not seeking official ISO 45001 certification, you can use this checklist to perform a self-assessment and identify gaps in how you evaluate the strengths and weaknesses of your EHS program, audit protocols, upper management’s responsibility in system performance reviews, and opportunities for change and innovation.
7. Communication and Coordination for Host Employers, Contractors and Staffing Agencies
Moss is a leader in the construction business in America, building residential, educational, correctional, public assembly and military projects, with a specialization in solar construction. With offices that extend from Florida to Hawaii, the family-owned company has been recognized by OSHA as an elite construction company within the agency’s Safety Recognition Program.
Moss specializes in creating work environments that are safe, secure and supportive. At Moss, safety is recognized as a value and the company expects every partner, vendor and subcontractor with whom they work to value safety.
“If people aren’t safe on sites and we are not mindful of the environment, our entire business is at risk. By choosing to partner with strategic subcontractors, we have grown our business since 2004 from $5 million to $3.5 billion,” says CEO Bob L. Moss. “Safety is a foundation for sustainable growth. Without the efforts of the entire team and our excellent safety record, we could not have grown this quickly. It’s all about keeping people who work on our sites safe and ensuring people who live in the area are also safe. Safety means work gets done — on time and on budget.”