Nonconformance vs CAPA: The Intersection of Safety and Quality Management
May 3, 2019
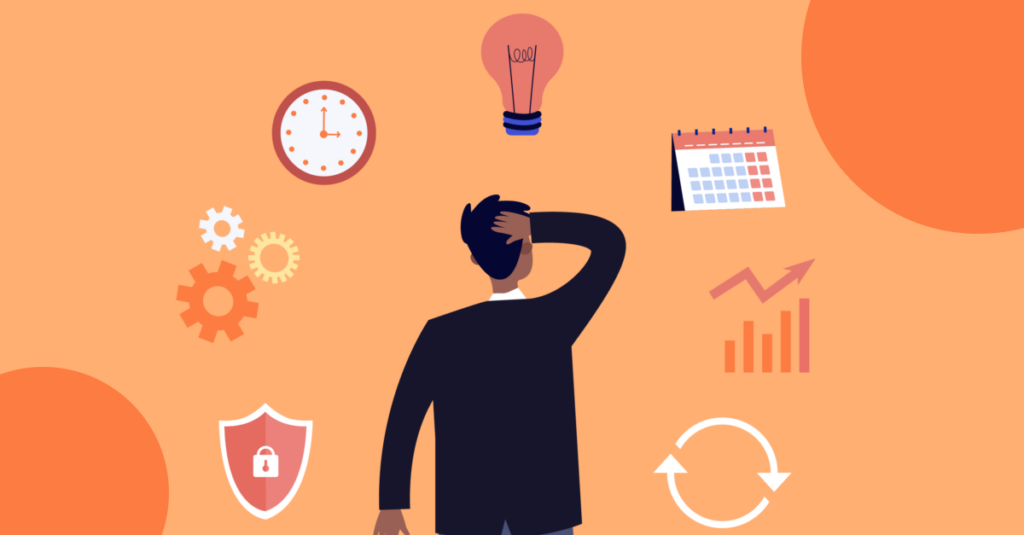
To develop operational excellence, modern organizations are continually striving to blend safety and quality management into a cohesive strategy that ensures employee welfare, customer satisfaction, streamlined processes and ethical leadership. To achieve this, it’s important to understand and implement two critical concepts: nonconformance and Corrective and Preventive Actions (CAPA). This blog post aims to unpack the relationship between these concepts, highlighting their role in developing a strong safety and quality culture dedicated to sustained continuous improvement.
Nonconformance, or nonconformity, refers to the failure to meet specified requirements—be these customer expectations, statutory or regulatory mandates or internal organizational standards like ISO 9001 protocols. Nonconformities are commonly found through an inspection, an audit or as a finding in an investigation. These failures can occur within any process or product and can be analyzed as factors that contribute to deep systemic issues within an organization.
On the other hand, CAPA involves a systematic approach to investigate existing or potential nonconformities. This process is crucial in identifying and eradicating underlying causes, thereby preventing recurrence and fostering a proactive culture of risk management and mitigation. Corrective Actions address existing problems, while Preventive Actions aim to deter future issues.
Blaine Hoffman, the producer of the SafetyPro Podcast, emphasizes the necessity for safety professionals to integrate their understanding across different departments. He suggests, “Do a couple of tours of duty in the quality department or in engineering and look at how they solve problems. What all safety management systems require in the end is the ability to integrate with other business processes. You need to determine that before even considering the implementation of a safety management system. (Ask yourself) do we have the infrastructure built to support the systems approach? That’s key.”
As organizations navigate nonconformances and CAPAs, they not only safeguard their workforce and mitigate risks but also open avenues for innovation and efficiency improvements. This intersection of safety and quality management is not just about compliance but is a strategic process for sustainable success and resilience. Thus, understanding the dynamic interplay between nonconformance and CAPA is fundamental for any organization committed to maintaining high standards of safety and quality.
Defining and Differentiating Nonconformances and CAPAs
By meticulously defining and differentiating nonconformance and CAPA, organizations can more effectively address safety and quality issues, ensuring both immediate problem-solving and long-term preventive measures. This structured approach not only enhances product and process quality but also aligns closely with organizational goals such as continuous improvement, employee welfare, customer satisfaction and ethical leadership.
Nonconformance in the context of safety and quality management represents a deviation from specified requirements, which can include customer expectations, statutory or regulatory standards, internal procedural benchmarks and international standards. Essentially, it captures any instance where processes or products fail to meet predefined criteria, setting the stage for immediate and corrective responses.
Nonconformance reports (NCRs) document such deviations, detailing how the nonconformity occurred, why it occurred, its impact and recommendations to prevent future occurrences. These reports are pivotal in enhancing operational efficiency, as they facilitate faster identification of nonconformities, streamline communication across various organizational levels and bolster overall visibility and accountability.
Corrective and Preventive Actions are distinct from nonconformances by focusing not just on immediate corrections but also on the strategic elimination of causes of potential future nonconformances. CAPA encompasses both actions taken to correct an existing nonconformity and preventative measures designed to forestall potential future problems. This dual approach not only aims to fix issues but also to fortify the system against similar future risks through thorough root cause analysis, implementation of strategic actions and rigorous verification of their effectiveness. It closes the loop by ensuring closure and sustainable change.
The primary objective of addressing nonconformance is to manage immediate issues effectively and efficiently, thereby reducing the cost of poor quality (COPQ), limiting exposure to risks such as warranty and recall costs and maintaining compliance with standards like ISO 9001 and ISO 14001. In contrast, CAPA aims at a deeper engagement with the problem, intending to uncover and address the systemic issues that allow nonconformances to occur, thereby preventing their recurrence.
To further clarify when to employ nonconformance reporting or CAPA, consider these three critical questions:
- Can the problem be fixed immediately within the process without significant consequences?
- Then a nonconformance should be reported.
- Did the problem result in significant negative outcomes such as waste, scrap or customer dissatisfaction?
- Then the root causes will be understood through CAPA.
- Is the issue indicative of a more systemic problem or likely to recur?
- Then both a nonconformance report and CAPA should be conducted to understand which part of your system factors to focus on and fix to ensure sustainable change.
The answers to these questions help determine the appropriate response, whether it be a detailed non-conformance report, a straightforward correction or initiating a comprehensive CAPA process.
The Connection Between Safety and Quality Management
Safety and quality management is not just a regulatory requirement but a strategic enabler of long-term success. Both disciplines fundamentally aim to mitigate risks and drive continuous improvement, making their intersection particularly impactful for operational excellence.
This shared goal is evident in how both systems prioritize identifying, analyzing and mitigating risks in processes and products. Addressing nonconformances and implementing CAPAs are key activities that serve dual purposes—they not only improve product quality by aligning outcomes with standards and expectations but also enhance workplace safety by preventing incidents and accidents.
For example, when a manufacturing defect is detected (a quality issue), not only does it affect product integrity, but it could also pose potential safety risks to end users and handlers that should be called out. Similarly, a safety incident caused by failing equipment could point to a quality issue in maintenance processes or the original manufacturing. Addressing these issues through CAPA means that the root causes are investigated, and measures are implemented to prevent recurrence, thereby improving both quality and safety.
A holistic approach to managing safety and quality recognizes that improvements in one area can significantly benefit the other. Integrating safety and quality management systems can lead to more comprehensive risk assessments, better resource allocation and enhanced communication across departments. When these systems are intertwined, organizations can create a feedback loop where data from safety incidents inform quality improvements and vice versa.
Organizations that adopt an integrated approach to safety and quality management often see several benefits:
- Enhanced Compliance: More effective alignment with regulatory requirements and standards, reducing legal and financial risks.
- Improved Efficiency: Elimination of duplicated efforts and conflicting objectives between safety and quality teams.
- Increased Employee Engagement: A safer workplace and a commitment to quality can lead to higher job satisfaction and morale.
- Greater Customer Satisfaction: Higher quality products and safer practices lead to improved customer trust and loyalty.
- Cost Reduction: Addressing safety and quality together can reduce the costs associated with accidents, defects and non-compliance penalties.
Best Practices for Intelex Nonconformance Reporting and CAPA Software
Effectively managing nonconformances and implementing CAPAs are crucial for maintaining the highest standards of quality and safety in any organization. Tools like Intelex Nonconformance Reporting and CAPA software can significantly enhance these processes. Here are some practical tips and strategies to maximize the effectiveness of managing non-conformance and CAPA systems.
Firstly, it is essential to establish clear procedures for identifying, documenting and addressing nonconformances. Develop standardized criteria for what constitutes a nonconformance across all departments to ensure that all employees can easily identify potential issues. Utilize Intelex’s capabilities to document every detail of a nonconformance incident thoroughly, including time, location and a description of the issue, along with any immediate corrective actions taken. Setting up automated workflows in Intelex ensures that nonconformances are addressed promptly, directing reports to the appropriate personnel and triggering notifications for urgent issues.
Employ structured methodologies like the 5 Whys, Fishbone Diagram or FMEA (Failure Modes and Effects Analysis) within Intelex to conduct effective root cause analyses. This helps in identifying the underlying causes of nonconformances, not just the symptoms. Based on these analyses, develop specific corrective and preventive measures and use Intelex to assign responsibilities and deadlines, ensuring accountability and timeliness. After implementing actions, regularly verify their effectiveness through assessments and audits, using Intelex’s tracking and data visualization tools to review outcomes and adjust actions as necessary.
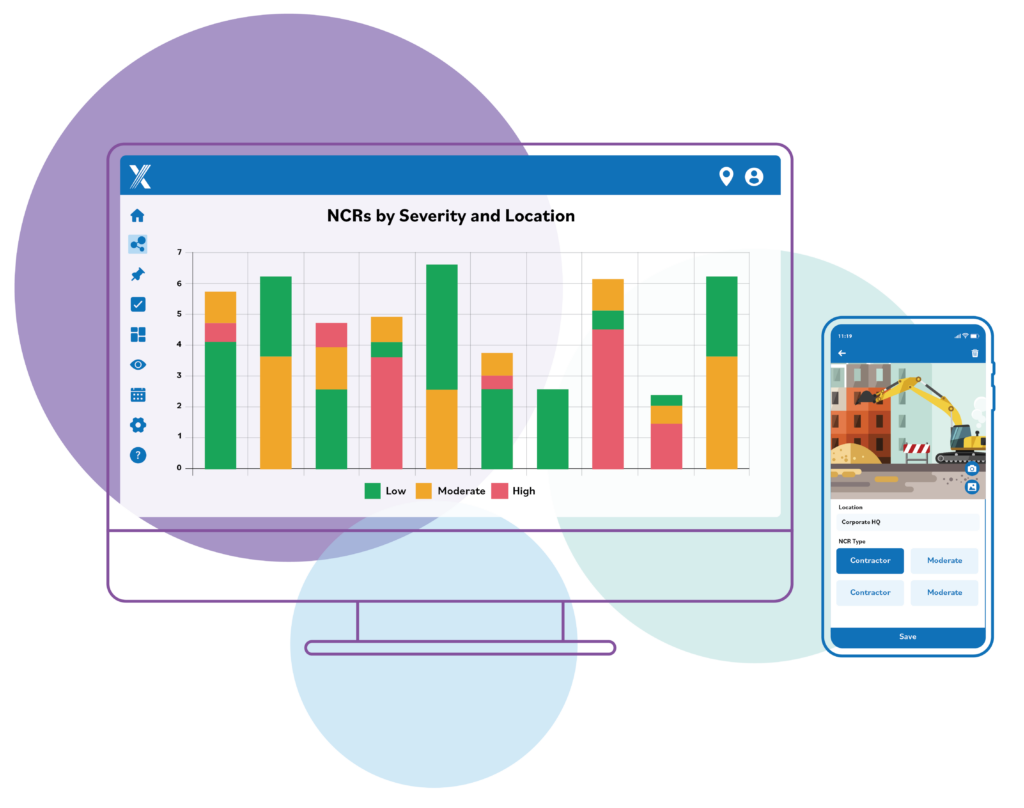
Moreover, emphasizing employee training and engagement in safety and quality initiatives is vital. Create a culture of safety and quality by actively involving employees in these processes, encouraging open communication and allowing them to share insights and suggestions. Recognizing and rewarding employees who contribute to these processes can motivate others to maintain high standards of quality and safety.
Finally, leverage technology for continuous improvement by utilizing Intelex’s robust reporting and analytics capabilities to identify trends in nonconformance and CAPA data. This analysis can provide strategic insights into potential areas for improvement in processes and products. The Intelex system also integrates smoothly with other management systems to enhance the overall effectiveness of safety and quality initiatives.
Ensure Organizational Success through Nonconformance and CAPA
Safety and quality management are not isolated; rather, they are integrally linked, each reinforcing the other to drive organizational success. By addressing nonconformances effectively and implementing robust CAPA procedures, organizations can not only ensure compliance and mitigate risks but also enhance operational efficiency and safeguard their integrity.
Implementing the best practices discussed for managing nonconformance and CAPA, such as using tools like Intelex, and fostering a culture of continuous improvement and employee engagement, is essential to developing strong business operations. These practices help organizations to proactively address issues and prevent them from recurring, thereby building a resilient operational framework. By adopting these strategies, organizations can position themselves to achieve sustained improvements and competitive advantage.
Ready to enhance your organization’s safety and quality processes? Create a custom demo of Intelex Nonconformance Reporting and CAPA software today. Discover how these powerful tools can streamline issue resolution, prevent recurrence, and drive continuous improvement.