The Space Shuttle Disasters and Quality Management
September 7, 2018
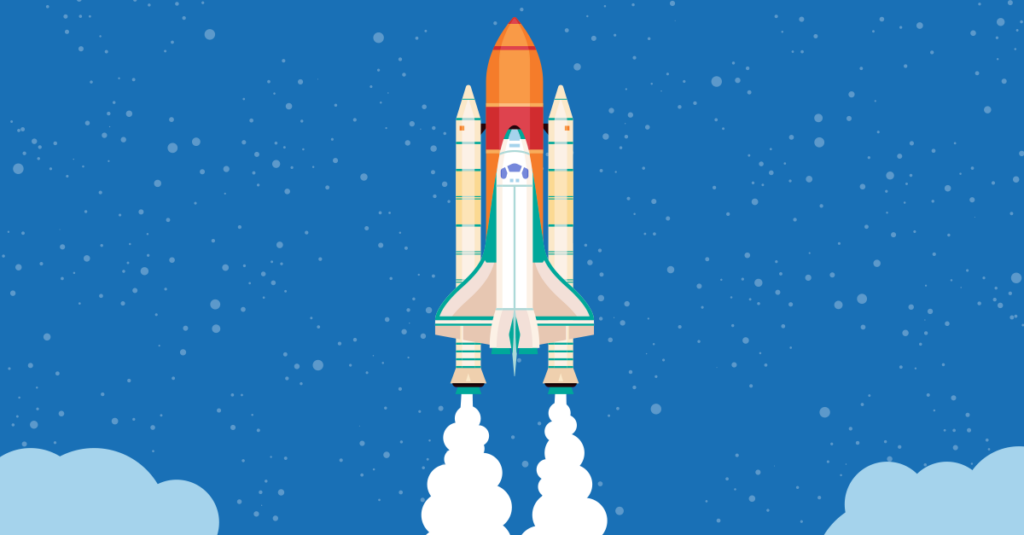
On January 28, 1986, the Space Shuttle Challenger was destroyed 73 seconds after lifting off from Cape Canaveral, Florida. Seven crew members died, a $3 billion-dollar orbital vehicle was lost, and NASA’s Space Shuttle program was suspended for 32 months.
The official cause of the disaster was the failure of an O-ring to prevent hot gases from leaking through the joint in the solid rocket motor during launch. The Rogers Commission – the body tasked with investigating the disaster – found that the O-ring design had been a point of concern for several years prior to the disaster, but that any concerns had been either poorly communicated or ignored in favor of maintaining project delivery on-time and on-budget.
In addition to the faulty initial design of the O-rings, the Commission determined that the unusually cold temperatures at the time of the launch (conditions in which none of the dependent systems on the Space Shuttle had ever been tested) meant that the rubber O-rings became inflexible and allowed the flow of gas to escape and ignite, a failure demonstrated by committee member Richard Feynman on live television during the inquiry. NASA had observed O-rings behaving in unusual and unanticipated ways during previous flights but had made the decision that as long as there was no cataclysmic failure of the equipment, this was an acceptable deviation, a phenomenon referred to as “normalization of deviance.”
Feynman produced an appendix to the final report in which he wrote: “It appears that there are enormous differences of opinion as to the probability of a failure with loss of vehicle and of human life. The estimates range from roughly 1 in 100 to 1 in 100,000. The higher figures come from working engineers, and the very low figures from management. What are the causes and consequences of this lack of agreement?” According to post-disaster analysis, NASA’s management culture in the mid-1980s was strongly biased against the methods of risk assessment that would have highlighted the likelihood of a disaster.
The Challenger disaster is a failure of NASA’s overall Quality Management System (QMS), particularly the Culture of Quality. The fact that the design flaw was a known defect but was incorrectly categorized as an acceptable risk, combined with a management structure replete with communications flaws that allowed managers to bypass Quality Management procedures, meant that NASA’s QMS was ill-equipped to prevent or manage a disaster of that scale.
Several of these QMS failures were cited as having a direct impact on the destruction of the Space Shuttle Columbia on February 1, 2003, the definitive cause of which was the impact of a piece of dislodged foam on the left wing of the vehicle during launch. This impact created a breach in the thermal protection system of the wing which, during reentry, allowed superheated air to enter the panels, which subsequently led to the destruction of the vehicle. The result in this case was the loss of seven crew, the destruction of the Space Shuttle Columbia, and the dismantling of the entire Space Shuttle program.
The report from the Columbia Accident Investigation Board cited poor risk-assessment, lack of managerial interest in promoting safety and Quality, overly simple presentation of complex information required for decision-making, and normalization of deviance as significant contributing factors, showing that even such a cataclysmic event as the Challenger disaster is sometimes not enough to demonstrate the importance of a QMS to organizations with deeply entrenched process failures.
How EHSQ Management Software Can Help
EHSQ (Environment, Health, Safety, and Quality) management software can play a vital role in preventing failures like those seen in the Challenger and Columbia disasters. Here’s how:
- Enhanced Risk Assessment: The software can streamline risk assessment, ensuring all potential hazards are accurately identified, evaluated and addressed before decisions are made.
- Improved Communication: EHSQ software provides centralized platforms for documenting and sharing critical safety and quality information across all levels of the organization, reducing the chances of miscommunication.
- Regulatory Compliance: Built-in compliance tracking ensures that organizations are aware of and adhere to industry-specific regulations, decreasing the risk of oversight.
- Continuous Monitoring and Auditing: Automated tools for monitoring and auditing ensure that deviations, like the O-ring issue, are flagged early, offering proactive opportunities to address concerns before they escalate.
- Normalization of Deviance Prevention: With clear reporting tools, the software enables the early detection of trends that could lead to a “normalization of deviance,” ensuring that any deviation from standard procedures is immediately addressed and corrected.
- Incident Management: When accidents do happen, EHSQ software aids in quick response and thorough investigation, enabling data collection that leads to long-term corrective actions.
Conclusion
The Challenger and Columbia disasters illustrate the dangers of neglecting proper risk management, communication, and quality procedures within an organization. EHSQ management software offers solutions to these challenges, providing tools for risk assessment, regulatory compliance and communication that can prevent disasters. In highly complex industries where safety and quality are paramount, this type of software is essential to ensuring organizational resilience and protecting both lives and assets.
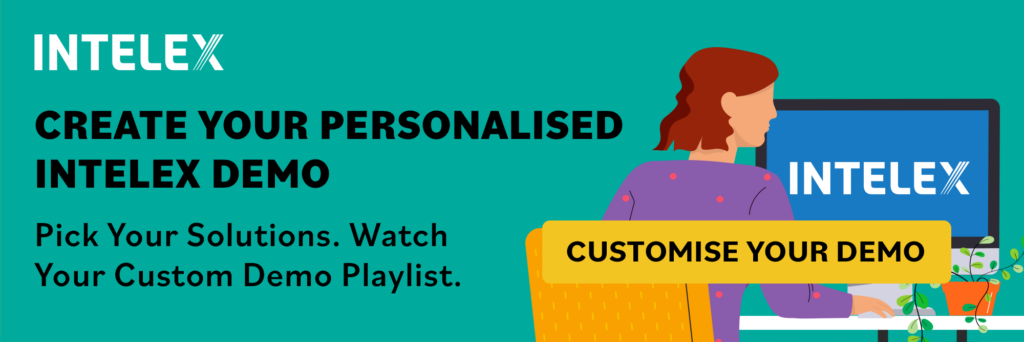