Driving a Strong Culture of Quality in the Automotive Industry: Strategies for Success
September 4, 2018
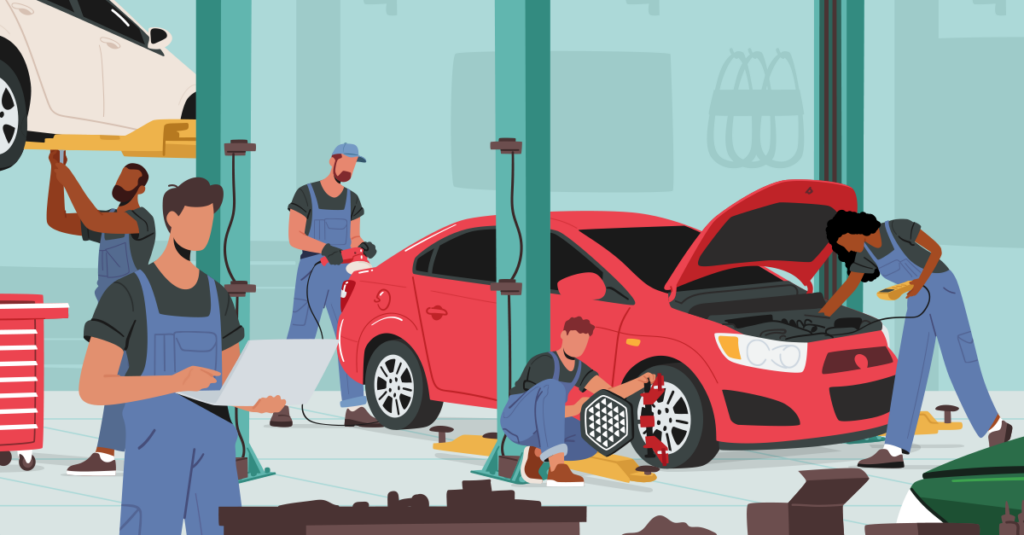
Each industry will have different interpretations of the concept of Quality and how to prioritize its tenets within their own field of practice, expertise and work experience. Perhaps the best fundamental principle is the definition of Quality from the International Organization for Standardization (ISO) as “the degree to which a set of inherent characteristics fulfills requirements where a requirement is a need or expectation.”
Automotive quality management dates to Henry Ford’s vision of a trained workforce assembling mass-produced vehicles with consistency and precision. Today, automotive quality reflects three principles:
- Quality in Product means the ability of the vehicle to fulfil its expected functions and behavior, such as engine efficiency, product features and environmental exhaust standards.
- Quality in Production means producing vehicles of a consistent quality standard while working within defined cost constraints.
- Quality in Ownership relates to customer satisfaction during their ownership of the vehicle. This includes the customer experience during purchase, vehicle reliability and the driving experience, as well as elements that are more difficult to measure, such as the feeling of status and pride the customer might experience while owning the vehicle.
Since 1999, the international standard for automotive Quality Management Systems has been ISO/TS 16949, developed by the International Automotive Task Force (IATF). In 2016, IATF published IATF 16949:2016, which supersedes ISO/TS 16949. IATF 16949:2016 is a supplement to, and fully aligned with, ISO 9001:2015, and is therefore not considered an independent Quality Management standard.
However, quality in the automotive industry is about more than just standards and Quality Control. It is also important to support a culture of quality that permeates every part of the organization.
Systematic Approaches to the Culture of Quality
A culture of quality in the automotive industry does not happen by accident. It requires careful attention and support from frontline workers and the leadership team. Here are some systematic approaches to quality culture that are relevant to the automotive industry.
The Toyota Production System/TPS
The Toyota Production System (TPS) first gained international prominence when James Womack and Daniel Jones set out to determine exactly what factors made the Toyota corporation in Japan such a quality leader. They determined that the Japanese approach to lean production was the culmination of the historical evolution of manufacturing methods in which teams of multi-skilled workers operated in a flexible way to produce larger volumes of standardized products with fewer errors at a lower price.
The Japanese were the first to master quality approaches in mass production. Although Walter A. Shewart had developed Statistical Process Control (SPC) in the 1920s, organizations had not adopted Shewart’s control charts approach very widely. After World War II, W. Edwards Deming gained the attention of Eiji Toyoda, who saw quality methods as the route to gain competitive advantage against his American counterparts. Toyoda used these methods to eliminate manufacturing waste and raise the level of product quality while simultaneously learning how to best meet customer and market requirements, a revolutionary method that became the Toyota Production System.
While some of the initial appeal of TPS was its rich toolbox of methods for reducing waste and enforcing manufacturing consistency through statistical methods, its success was more than simply the sum of its tool-based parts. The culture of quality at Toyota is built not on tools but on adapting the scientific method to the manufacturing environment. With a shared structure for data-driven decision making and a culture that supports adjustment, every worker can dynamically solve problems on-the-spot, and everyone is empowered to use these results to improve performance. Far from being a rigid constraint, the scientific method encourages innovation, learning, creativity and agency. Using just-in-time (JIT) production, which requires maintaining only the minimally necessary amounts of stock and production supplies on hand at any given moment, production facilities can eliminate excess waste and costs associated with large stock.
TPS is not a cultural rulebook to be read and implemented in an authoritarian manner. Instead, it has four distinct features:
- Highly standardized work with trained people that yields desired outcomes.
- A pull-based system where people request tasks and resources as needed to conduct the standardized work process.
- Every process is a continuous experiment subject to changes based on new information.
- Continuous improvement and organizational learning occur at the lowest levels of the organization. Kaizen—a Japanese word derived from “kai” (change) and “zen” (good)—is a critical component of this approach, in which people, processes and tools come together to empower workers, improve processes and eliminate waste across the organization.
Total Quality Management
The concept of Total Quality Management (TQM) derives from the work of Deming, Joseph M. Juran and Kaoru Ishikawa in his 1985 book What is Total Quality Control? The Japanese Way. It was an American response to the success of TPS in Japan and the resulting domination of the marketplace by Japanese automobile manufacturers in the 1980s. Kujala (2004) identifies a core set of fundamental TQM values.
- Organizational mission and shared objectives.
- The organization is dedicated to serving the customer, employees and society, and to exceeding customer requirements.
- Management approach and organizational decision making.
- Management makes fact-based decisions and makes continuous improvement a permanent organizational focus.
- Involvement of management and employees.
- Leadership embodies the focus on quality and ensures the involvement of all employees.
- Planning, coordination and time-related performance.
- The organization maintains a long-range view of the future, designs quality into every product and service, views all processes as contributing to the overall performance and builds strong partnerships.
TQM emphasizes how organizations must continuously monitor the Voice of the Customer (VoC) to meet customer needs, how to use statistical tools and quality methods to satisfy requirements and how leadership should empower the entire organization. TQM is therefore far more than a set of tools for statistical measurement. Instead, it is a wide-ranging and rigorous approach to establishing a culture of quality. Ultimately, a TQM approach will incorporate four elements:
- Quality as a key priority
- Customer focus
- Teamwork and empowerment
- Data-driven decision making using statistical methods
Volkswagen Dieselgate: A Culture of Quality Failure in the Automotive Industry
Quality Management is about more than simply meeting customer requirements and eliminating waste. When an organization lacks a strong culture of quality, there can be catastrophic impacts on consumer confidence and legal compliance. The Volkswagen “Dieselgate” scandal provides an excellent example of this.
In early 2014, the International Council on Clean Transportation began working with researchers at West Virginia University’s Center for Alternative Fuels, Engines, and Emissions (CAFEE) to follow up on reported discrepancies in the emissions of Volkswagen diesel vehicles. The California Air Resources Board (CARB) had previously subjected the vehicles to rigorous emissions testing in the laboratory, and the vehicles had all passed with no indication of any problems. The CAFEE researchers did their emissions test in the field and produced some very different results.
The researchers discovered that when operating in the real world, the vehicles produced emissions that fell far outside the limits allowed for diesel vehicle certification in the United States. After more testing, the researchers discovered a sophisticated software application that used environmental data from the vehicle, such as the absence of movement from the steering wheel, to determine when the vehicle was undergoing testing in a laboratory and when it was operating in the real world. If the software determined the vehicle was undergoing testing, it would turn on the emission control to pass the test. If the software determined the vehicle was operating in the field, it would turn off the emission control, which would increase emissions beyond acceptable levels but would also greatly improve fuel economy and vehicle performance.
After initial attempts at denial, Volkswagen eventually admitted to having knowingly created and installed this software application as a way of intentionally deceiving the testing mechanisms of regulators around the world between 2009 and 2015, affecting about 11 million vehicles.
Due to this deception, Volkswagen announced plans to spend $18.32 billion on fixing the issue. In January 2017, Volkswagen pleaded guilty to criminal charges and agreed to pay a fine of $2.8 billion. Additional criminal charges are pending against a number of former employees, and the case continues to work its way through the courts, causing ongoing brand damage.
The “Dieselgate” case is an example not of the failure of a dysfunctional system but of willful manipulation of that system and a violation of the principles of a culture of quality. By all accounts, Volkswagen had a sterling reputation for quality throughout the organization, and yet reports say that several people at the management level had been aware of the deception for years.
Conclusion
A culture of quality in the automotive industry requires more than just a digital quality management system or a set of sophisticated statistical tools. It requires leadership commitment and frontline involvement to ensure people, processes and tools operate in harmony to produce continuous quality improvement throughout the organization. However, as the Dieselgate scandal shows, poor leadership commitment to a culture of quality can undermine all this hard work and cause long-term damage. Ultimately, a culture of quality depends on supporting and sustaining the shared quality values of the organization at every level to embrace opportunities for innovation and avoid potentially catastrophic risks.
Ready to elevate your safety and quality standards? Sign up for a demo of our manufacturing safety and quality management software and see how it can transform your operations.